Blockage in critical machinery can significantly impede fluid flow and compromise the overall performance of industrial systems.
Fig. a) illustrates a pump equipped with a discharge valve that has experienced a failure at its seat. This failure has led to an obstruction that hinders the fluid movement throughout the system. Such obstructions can result from wear, debris accumulation, or faulty valve mechanisms. In turn, this obstruction can result in operational inefficiencies, reduced productivity, and even potential safety risks.
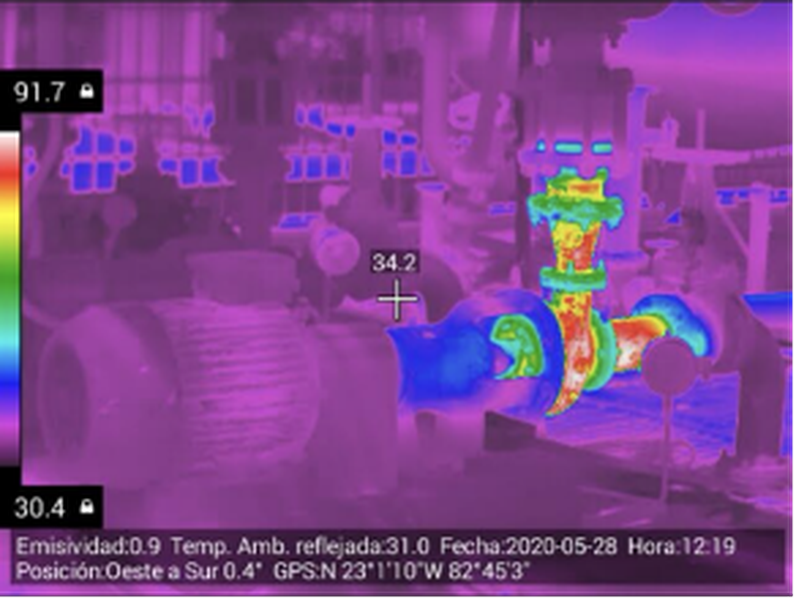
Fig. b) presents another scenario, where a pump is equipped with a suction valve that has suffered a failure at its seat, obstructing the fluid flow. Similar to the previous case, this obstruction can result from a variety of factors, ranging from mechanical wear to unforeseen operational issues. The consequences remain consistent—impeded fluid flow resulting in reduced efficiency and potential equipment damage.
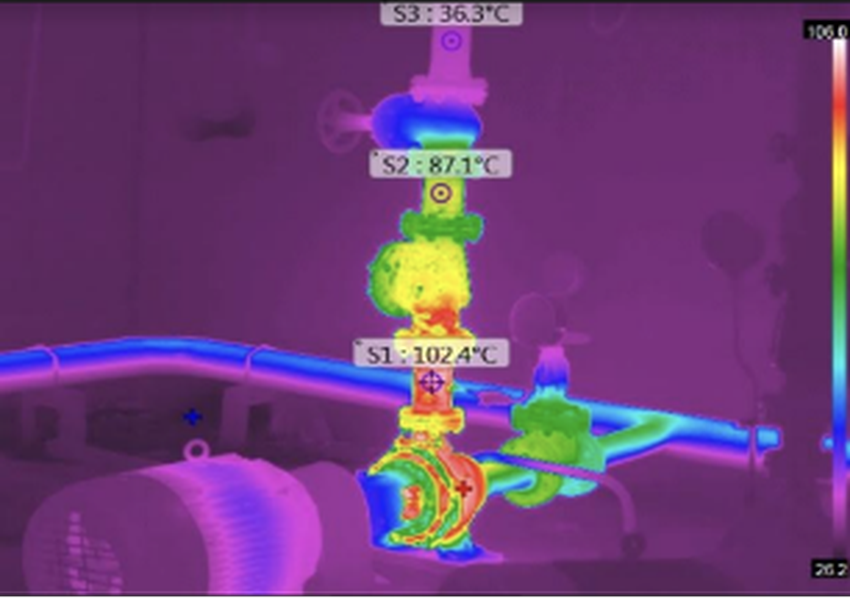
In both cases, thermography emerges as a powerful tool for promptly identifying and addressing such obstructions. By harnessing the capabilities of infrared technology, thermographers can detect temperature variations caused by restricted fluid flow. These temperature irregularities serve as indicators of potential obstructions, providing valuable insights into industrial system health.
Identifying and rectifying obstructions before they escalate can mitigate production downtimes, prevent costly repairs, and safeguard personnel and assets.
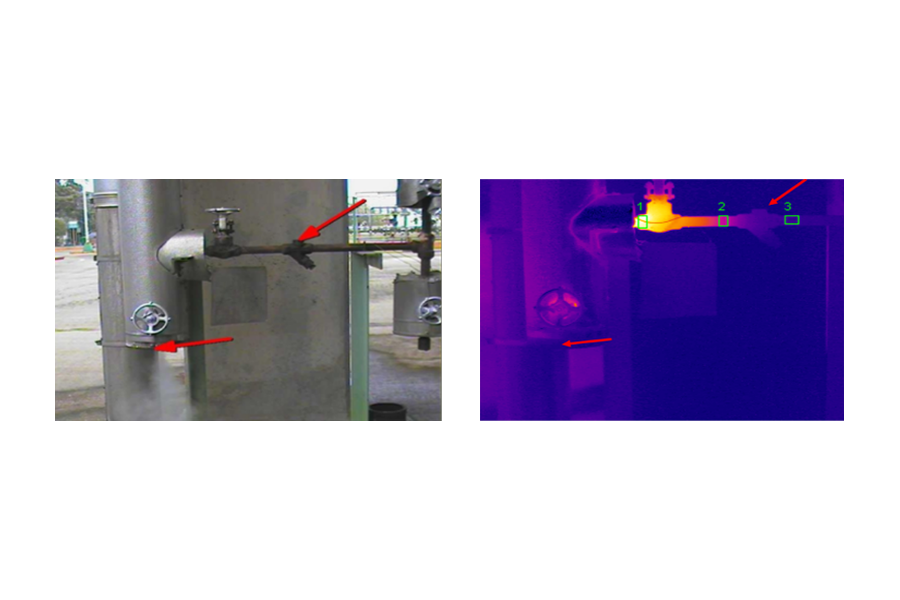
The capacity to identify obstructions through thermographic analysis exemplifies how a preventive approach can translate into optimized performance, minimized risks, and a resilient industrial ecosystem.