Uneven temperature, also known as thermal variation, is a common issue in industrial equipment and systems. It occurs when different areas of a surface or component have different temperatures than expected. This thermal variation can be an indication of underlying problems such as fluid flow blockages, uneven wear, insulation issues, component damage or mechanical issues.
Infrared thermography is a valuable tool for identifying uneven temperature. By detecting subtle differences in heat emission, thermography can visualize and highlight areas where temperature is not uniform. This enables technicians to identify problematic zones and take preventive measures before issues escalate.
A practical example of how infrared thermography can identify uneven temperature is in pipeline systems. If there's a blockage in a pipeline, thermography can reveal temperature differences along the pipeline, indicating possible blockages or flow restrictions.
Thermograph allows us to observe the normal operation of an expansion valve in the refrigeration cycle of a chiller. The valve receives refrigerant in liquid state, at high pressure and temperature, and exits at low pressure and temperature, and any changes can be detected.
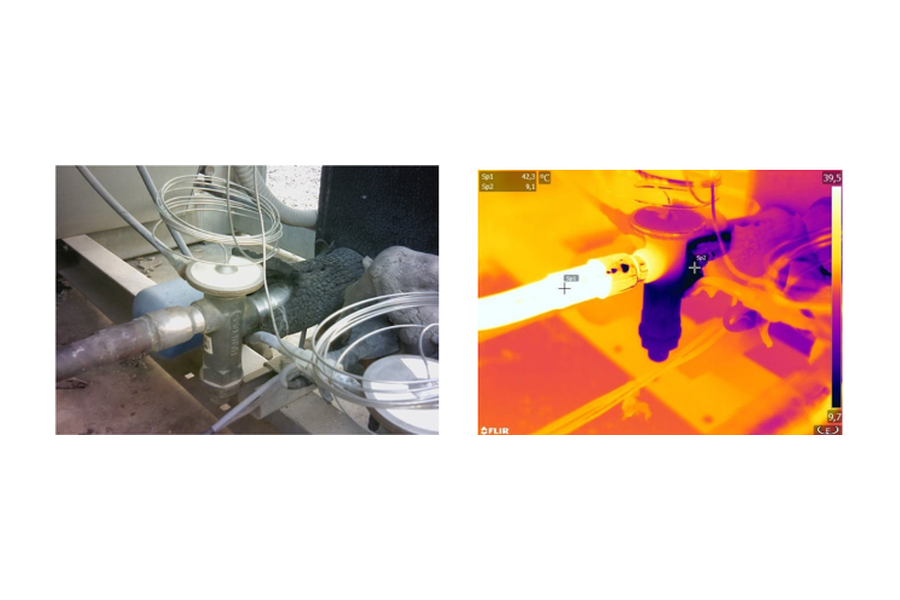
Thermograph enables the identification of defects that often go unnoticed and can reduce the lifespan of machines. In the previous case, it was discovered that the motor rotor was supplied with the fans installed in reverse, causing the air not to reach its cooling system. This led to unexplainable high temperatures deemed unacceptable for such machines' operation.
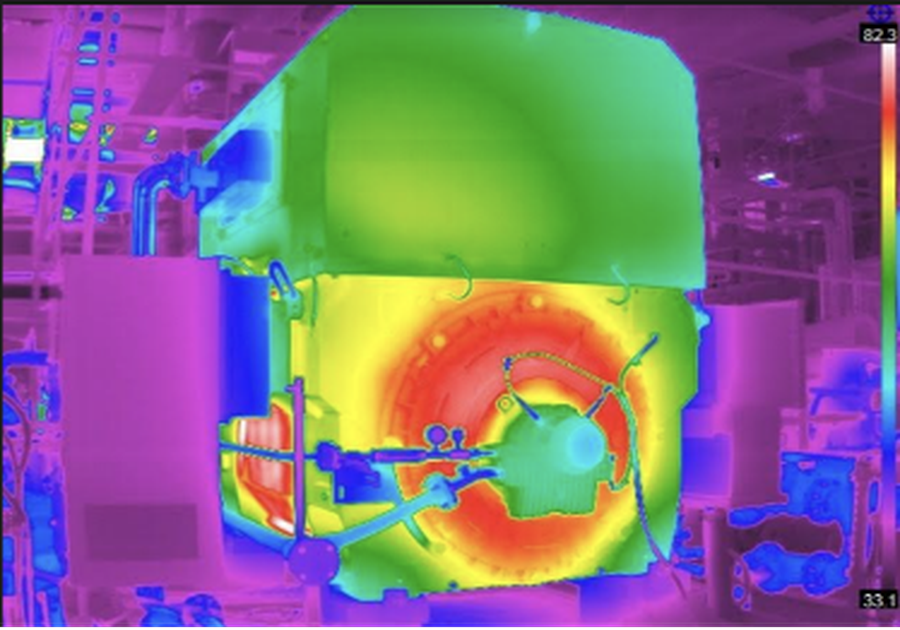
Tanks of various capacities are widely used in industry to store water, fuels, chemicals, food, gases, biopreparations, cement, paints, and other materials.
Through thermography, it is possible to detect temperature differences that reveal the conditions inside the tanks. If a temperature difference exists between the stored material and the air at the tank's top, the content level can be identified.
This technology helps prevent costly and catastrophic damage in processes involving potential leaks or overflows of containers with hazardous materials, thereby avoiding significant losses in time, resources, and environmental damage.
During a thermographic inspection, essential factors to consider include sealing integrity, inlet and outlet valve condition, potential leaks, residue accumulation, unwanted layers of liquids or solids, damaged refractories or coatings, and leaks in tank walls. Regardless of the source of the leak, it tends to manifest as a defect with changes in temperature.
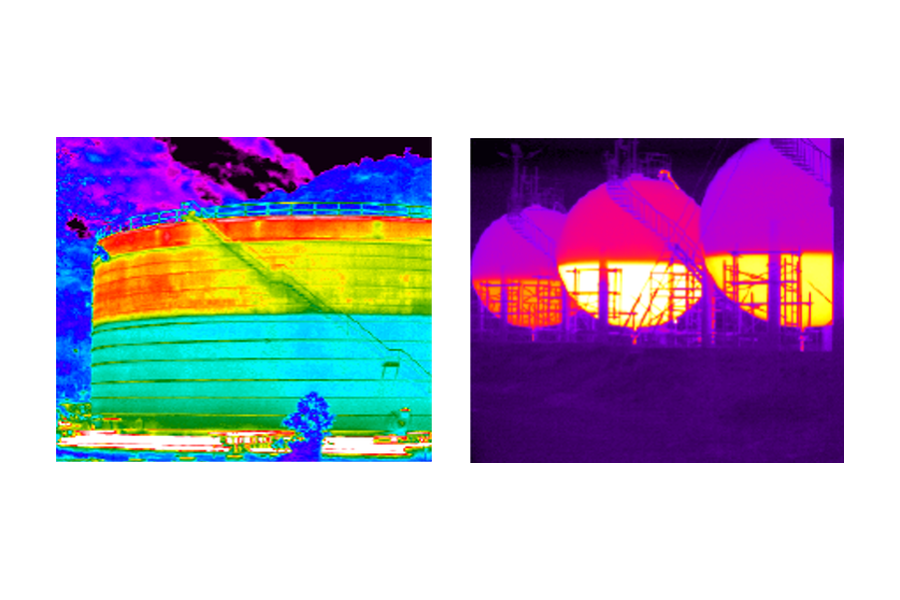
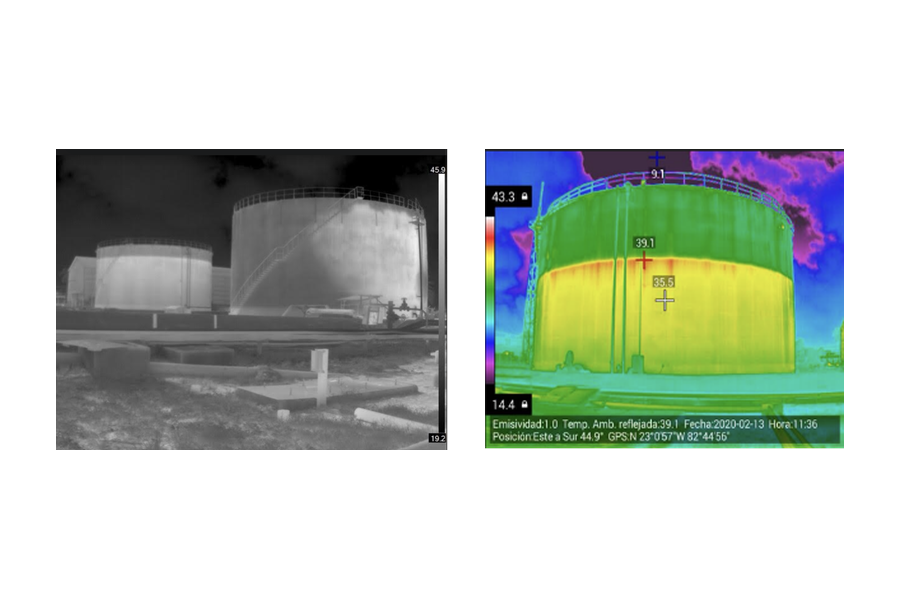
Gears are mechanical systems that transmit rotational motion from one shaft to another through the successive contact of gear teeth.
Like any machine element, their primary cause of failure can be attributed to inadequate design, material, dimensions, tolerances, and strength. Other factors may include incorrect assembly and adjustment practices, improper lubrication procedures, and overstressing due to external factors.
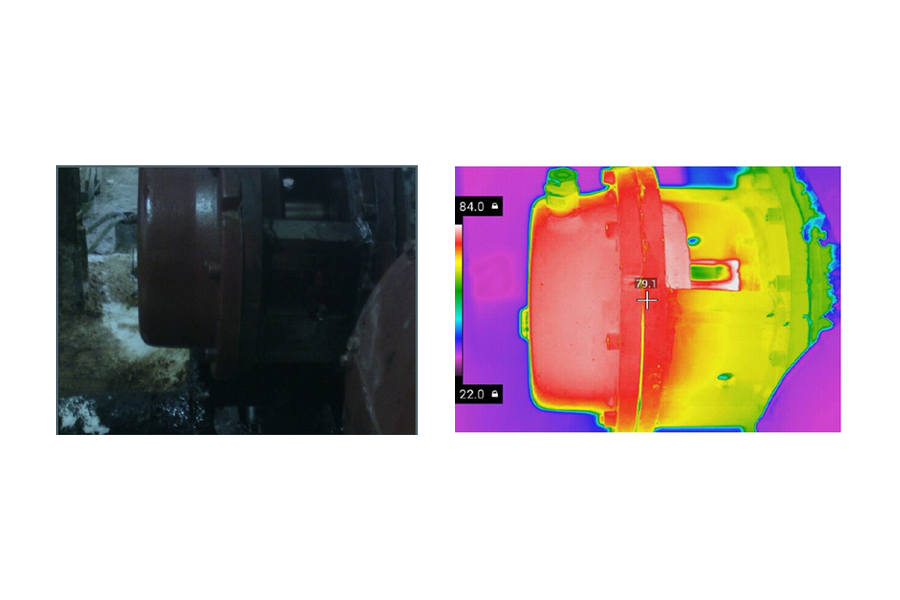
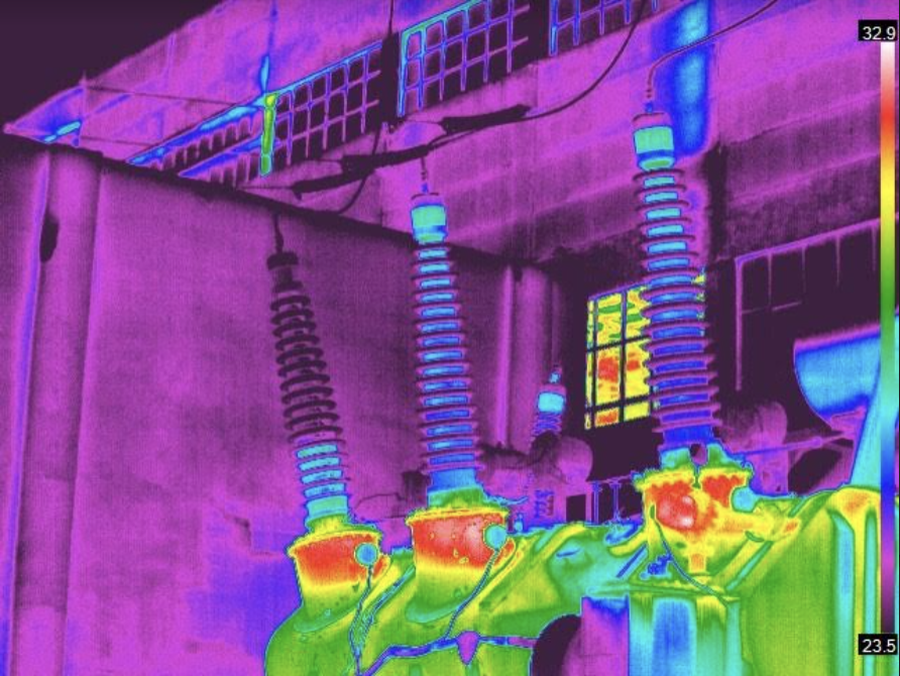
Output transformer of a power generation unit, Phase A with oil leakage into the transformer interior. The dark area on the bushing indicates the amount of missing oil. The cause of the oil loss was partial discharges inside the pressurized container, which caused the inner seal to break and resulted in oil leakage.