Infrared thermography involves sophisticated instruments designed to detect, measure, and visualize the thermal radiation emitted from objects. These instruments play a vital role in predictive maintenance, condition monitoring, and various diagnostic applications across multiple industries.
The available instrumentation for Infrared Thermography can be divided into two types of measurement systems:
Non-imaging Infrared Thermography and Temperature Monitoring
These systems are simpler and known as radiometers, infrared thermometers, or pyrometers. They record the radiation emitted by the body and convert the output voltage of the instrument's detector into a calibrated temperature value displayed as the reading on the screen.
Types of Non-Imaging Temperature Sensors
Infrared Thermometers
Infrared thermometers utilize optical systems and infrared detectors to measure surface temperatures remotely. Essential in scenarios where physical contact is impractical or hazardous, they enable rapid, precise thermal assessments critical for real-time diagnostics.
Pyrometers
Pyrometers specialize in measuring elevated temperatures. They are commonly utilized in industrial applications such as metallurgy, glass production, and thermal process control. These instruments feature narrow spectral bandwidths to maximize measurement accuracy under extreme thermal conditions.
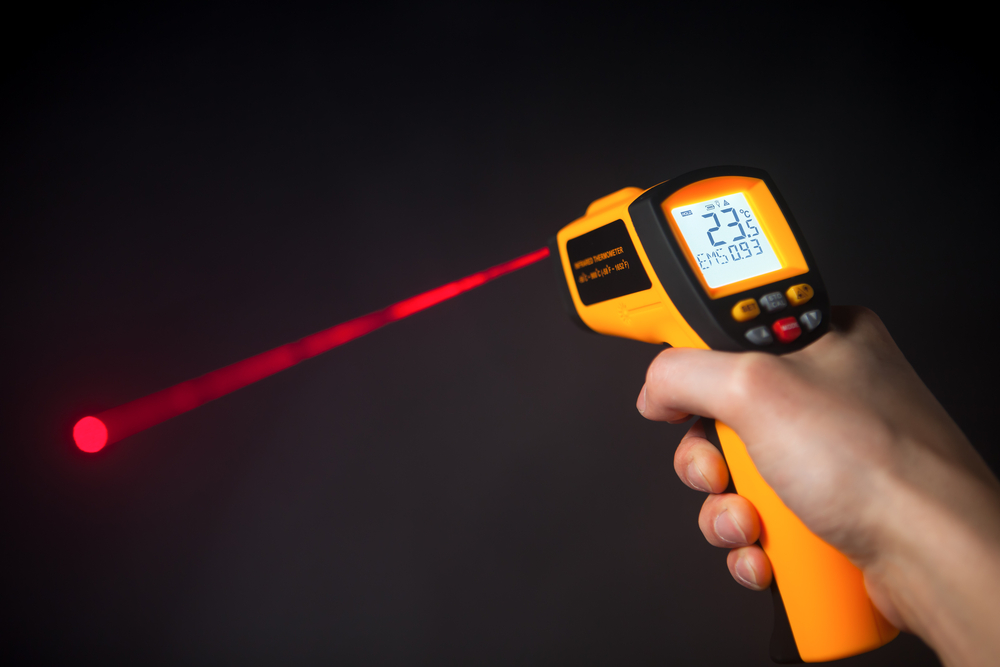
Radiometers
Radiometers detect and measure emitted infrared radiation without generating detailed thermal images. They are primarily applied in controlled laboratory and industrial environments and facilitate quick and precise thermal evaluations.
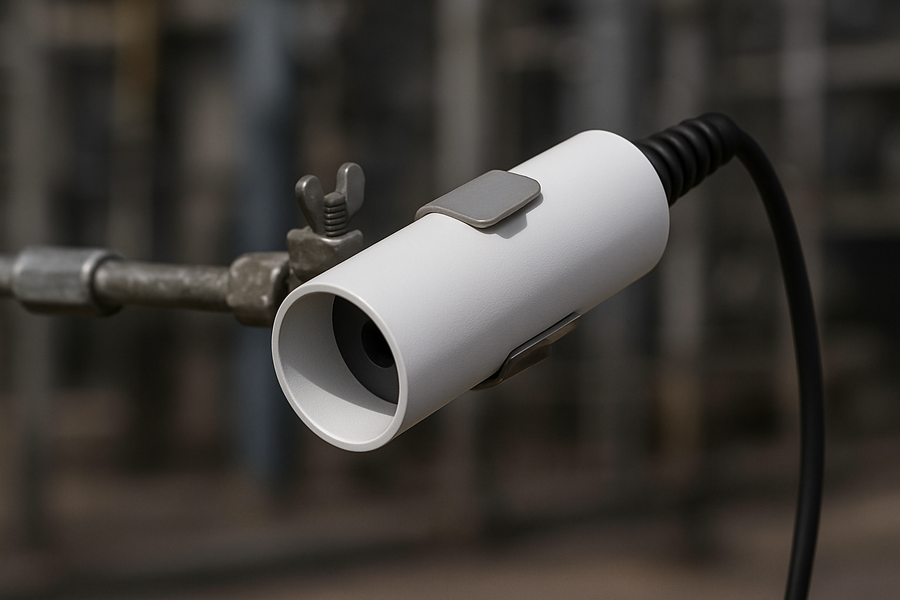
Online Temperature Monitoring Systems for Condition Monitoring
Continuous Temperature Measurement
Online monitoring systems use various temperature sensors to continuously assess thermal conditions in industrial assets. The PT100 (platinum resistance thermometer) is particularly prevalent due to its high accuracy, stability, and suitability for long-term continuous measurements.
Additional Temperature Sensors Used
- Thermocouples: Popular for wide temperature ranges and quick response times.
- Thermistors: Valued for high sensitivity and precise measurements in limited temperature ranges.
Integration with Cloud-Based Condition Monitoring Platforms
Integrating temperature sensors, including the widely used PT100, into cloud-based platforms enables remote access to real-time data, diagnostics, and predictive trend analyses. This capability significantly reduces downtime, enhances decision-making processes, and optimizes maintenance strategies.
Integrated Vibration and Temperature Sensors
Multifunctional Integrated Sensors
Advanced monitoring increasingly integrates vibration analysis with temperature measurement. These multifunction sensors deliver comprehensive data on equipment health, allowing correlation between thermal anomalies and mechanical vibrations, which are essential for predictive diagnostics.
Technical Applications and Advantages
- Early detection of developing faults by correlating temperature and vibration data.
- Enhanced predictive maintenance accuracy, reducing operational downtime and risk.
- Efficient data acquisition and analytics through integrated sensor technology improve overall condition monitoring effectiveness.
Sensor Selection and Installation Guidelines
- Considering application-specific requirements, evaluate sensor specifications, including accuracy, response time, and environmental robustness.
- To achieve precise and representative monitoring data, determine sensor placement strategically using principles of heat transfer, mechanical vibrations, and operational dynamics.
Thermography Cameras
These systems use two-dimensional detectors that measure the radiation emitted by an object and then process the information electronically, generating an image that represents the thermal pattern of the object's surface under study. A thermal camera produces a live image that allows visualizing the information as a thermal radiation photograph. An image produced by an infrared camera is called a thermogram.

Thermal cameras (thermography cameras) have evolved significantly from their initial military applications in the mid-20th century to versatile, industry-wide diagnostic tools. Modern thermography cameras integrate advanced optics, sensitive detectors, and powerful image processing capabilities, enabling precise thermal analysis.
Main Components
- Infrared Lens: Specially designed lenses focus infrared radiation onto the detector.
- Thermal Detector (Sensor): Converts the captured infrared radiation into electrical signals that create the thermal image.
- Optical System: Employs mirrors and prisms to direct infrared radiation to the sensor.
- Display (Viewfinder/Screen): Provides real-time thermal imaging to the user.
- Focusing System: Enables clear and sharp images through adjustable focus.
- Battery: Supplies power essential for camera operation.
- Image Storage: Allows storing thermal images for further analysis.
- Camera Housing: Protects internal components and supports ergonomic usage.
Operating Principles
Thermography cameras operate on the fundamental principle that every object above absolute zero (-273.15°C) emits infrared radiation. The intensity of emitted radiation varies directly with temperature—hotter objects emit more infrared radiation, while colder objects emit less. The camera’s lens captures this emitted radiation, focusing it onto a sensor. The sensor then translates this radiation into electrical signals, creating a visible thermal image displayed on the camera’s screen. These images vividly illustrate thermal patterns, enabling users to quickly identify thermal anomalies, heat leaks, or equipment inefficiencies.
Key Characteristics
When selecting and using thermography cameras, consider these crucial technical characteristics:
Thermal Resolution and Optics
- Detector Resolution: Modern cameras typically use focal plane array (FPA) detectors (e.g., 320x240, 640x480 pixels). Higher resolution provides more detailed images.
- Spatial Resolution (IFOV - Instantaneous Field of View): Determines the smallest detail detectable at a given distance. It defines the camera's capacity to clearly identify smaller objects or thermal anomalies.
- Field of View (FOV): Dictated by lens choice. Wider FOV lenses (short focal length) cover larger areas but reduce detail, whereas narrow FOV lenses (long focal length) provide finer detail at longer distances.
Temperature Range and Thermal Sensitivity
- Temperature Range: Defines the lowest and highest measurable temperatures. Selecting an appropriate range is vital to cover the full extent of the temperatures encountered.
- Thermal Sensitivity (NETD - Noise Equivalent Temperature Difference): Indicates how effectively the camera can detect subtle temperature differences. Lower NETD values (e.g., <0.05°C) imply higher sensitivity and better detection of small temperature variations.
Spectral Range
Infrared cameras operate within specific spectral ranges:
- Long-wave Infrared (LWIR): Most common (8-14 µm). Suitable for general industrial and maintenance applications.
- Mid-wave Infrared (MWIR): Typically cooled cameras (3-5 µm). Best for specialized applications requiring high sensitivity, such as long-range surveillance or research.
Frame Rate and Image Acquisition Speed
- Frame Rate (FPS): Number of images captured per second. Higher frame rates (30-60 fps or higher) are important for monitoring fast-moving or dynamic processes in real-time.
- Image Acquisition Speed: Critical in scenarios where rapid temperature changes must be monitored closely.
Radiometric and Non-Radiometric Cameras
- Radiometric Cameras: Allow precise temperature measurement at every pixel, essential for quantitative analysis.
- Non-Radiometric Cameras: Provide thermal images without exact temperature measurements; useful primarily for qualitative assessments.
Advanced Camera Functions and Analysis Features
Modern thermal cameras offer features enhancing analysis capabilities:
- Adjustable Color Palettes: Facilitate better interpretation of thermal images by applying colors or grayscale to different temperature ranges.
- Span and Level Adjustments: Allow users to manually enhance image contrast and brightness, highlighting temperature differences effectively.
- Analysis Tools: Built-in software functions like temperature profiles, image comparisons, and annotation tools provide deeper insights and simplify reporting processes.
Best Practices for Accurate Thermal Imaging
To achieve reliable results during thermographic inspections, apply these best practices:
- Camera Calibration: Regularly calibrate cameras to ensure accuracy.
- Environmental Considerations: Avoid inspecting highly reflective surfaces or under rapidly changing environmental conditions that may distort readings.
- Optimal Distance and Angle: Maintain recommended camera-to-object distances and angles to minimize measurement errors.
- Multiple Perspectives: Capture thermal images from different angles to verify anomalies and ensure comprehensive analysis.
- Regular Maintenance: Clean lenses frequently, inspect equipment regularly, and store the camera properly.
- Operator Training: Ensure operators understand camera functionality, adjustments, and interpretation of thermal images for accurate diagnosis.