Electrical Thermography for Detecting Failures and Hotspots in Electrical Equipment
This application involves the use of thermography to detect failures and hotspots in electrical equipment. By identifying abnormal temperature patterns, potential electrical issues can be spotted early, preventing failures, and ensuring the safety and reliability of electrical systems.
Electrical systems can primarily be diagnosed by examining the condition of connections, terminals, insulators, transformers, windings, generators, and identifying phase imbalance. For example, a temperature increase of 10 °C halves the life expectancy of bearings and windings. If over-lubrication of a bearing raises the temperature of the winding by 20 °C, the winding will last only a quarter of its potential service life. With a 50 °C increase, a winding that should last 20 years would have a life expectancy of only eight months.
Repair Priority Table: Phase-to-Phase or Component-to-Component Temperature Increase Compared to Normal
- AAA: Above 100°C – Repair or correct immediately.
- A: 50 – 99°C – Repair as soon as possible.
- B: 30 – 49°C – Repair at the next available opportunity.
- C: 11 – 29°C – Schedule for the near future.
- D: 1 – 9°C – Address during the next scheduled maintenance shutdown.
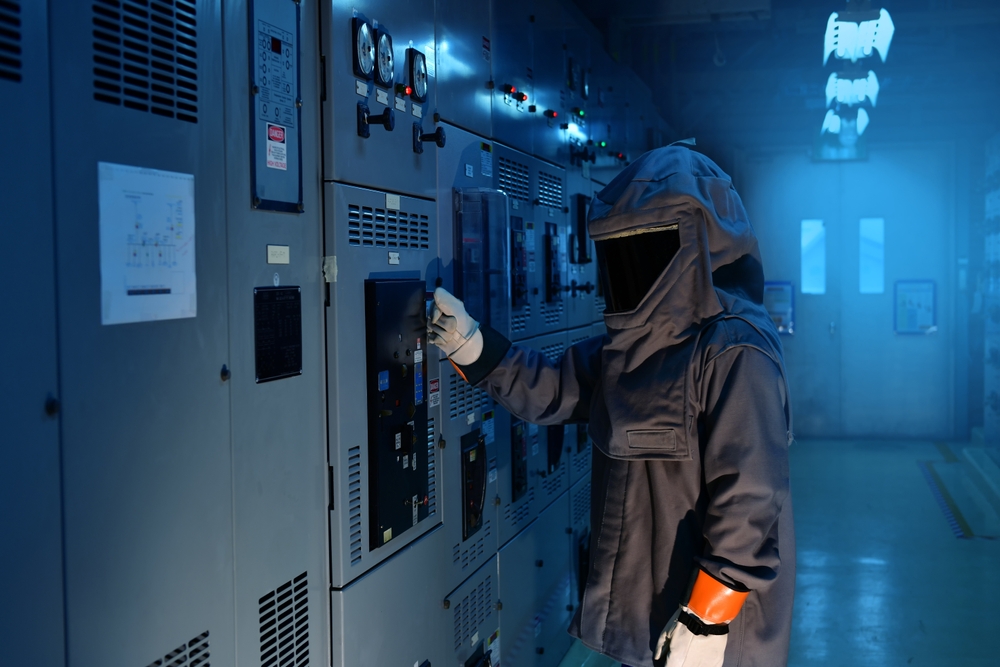
Standards such as NFPA 70E, OSHA 1910, and CSA Z462 in Canada define the use of infrared thermography (IR) for predictive maintenance on electrical equipment. These standards require individuals conducting IR inspections on open electrical panels above 50 V to use personal protective equipment if within the safe distance. The use of personal protective equipment can make it challenging to operate small thermal cameras, emphasizing the importance of using infrared windows.
Infrared windows allow for non-invasive inspection of the interior of electrical cabinets without the need to open them. These windows are made from certified materials specifically designed for this purpose.
An infrared inspection window is used to separate environments with different pressures or temperatures while allowing energy to pass through at a specified electromagnetic wavelength between the two environments. An infrared window, also known as a viewing port, inspection panel, or viewport, is a generic term used to describe an inspection point designed to allow infrared radiation to be transmitted to the external environment. In simple terms, an infrared window (IR) is a data collection point for a thermal camera.
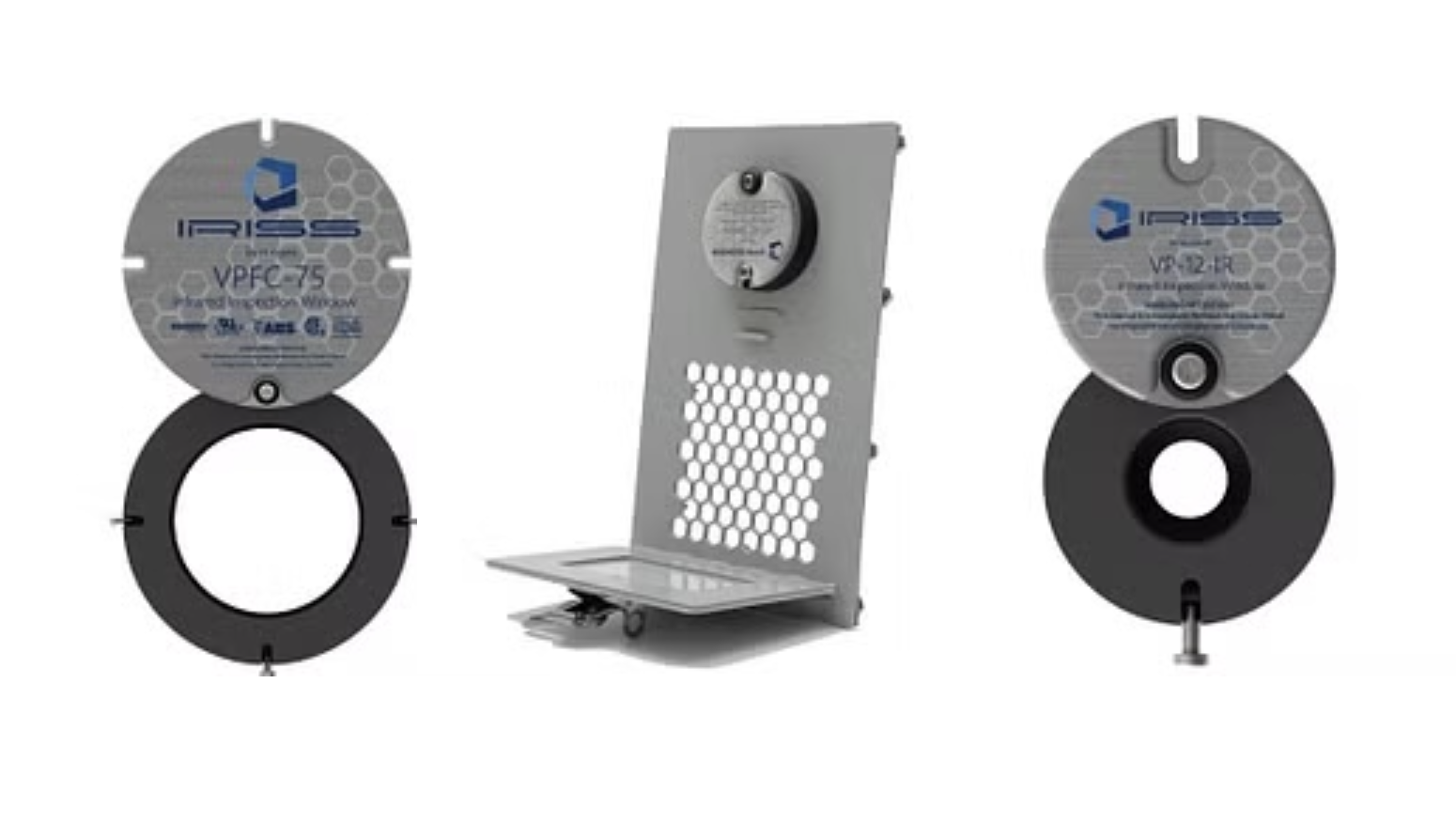
Building Diagnostics and Energy Auditing for Improved Efficiency
Thermography is employed for building diagnostics and energy auditing to assess the energy efficiency of structures. It helps to identify insulation gaps, air leaks, and other building defects that contribute to energy loss. This information aids in improving energy efficiency and reducing energy consumption.
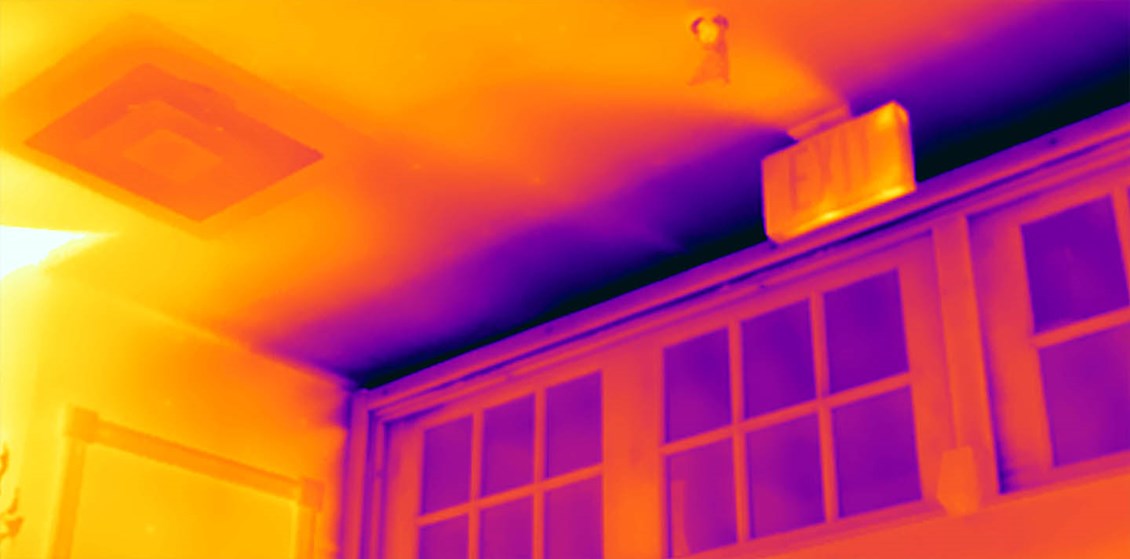
Industrial Applications, Including Process Monitoring and Quality Control
In the industrial sector, infrared thermography is widely utilized for process monitoring and quality control. It allows for non-destructive testing and inspection of equipment, detecting defects or abnormalities in manufacturing processes, ensuring product quality, and optimizing overall productivity.
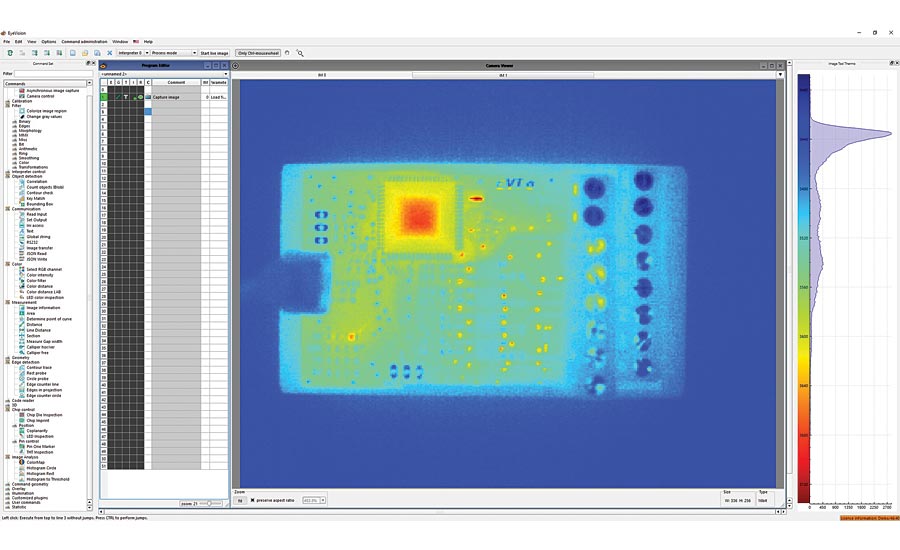
In process analysis, thermography enables the evaluation of valve conditions, detection of underground pipes, measurement of liquid and solid levels in tanks, refractory studies, and assessment of thermal losses, steam leaks, and vacuum losses.
Moreover, thermography proves valuable in diagnosing mechanical systems, leading to reduced maintenance costs, extended equipment lifespan, and improved machinery availability. It enables the study of temperatures in different parts of a moving mechanical system under full load. Various components such as motors, generators, bearings, pulleys, transmission systems, shaft misalignments, and weld conditions can be diagnosed.
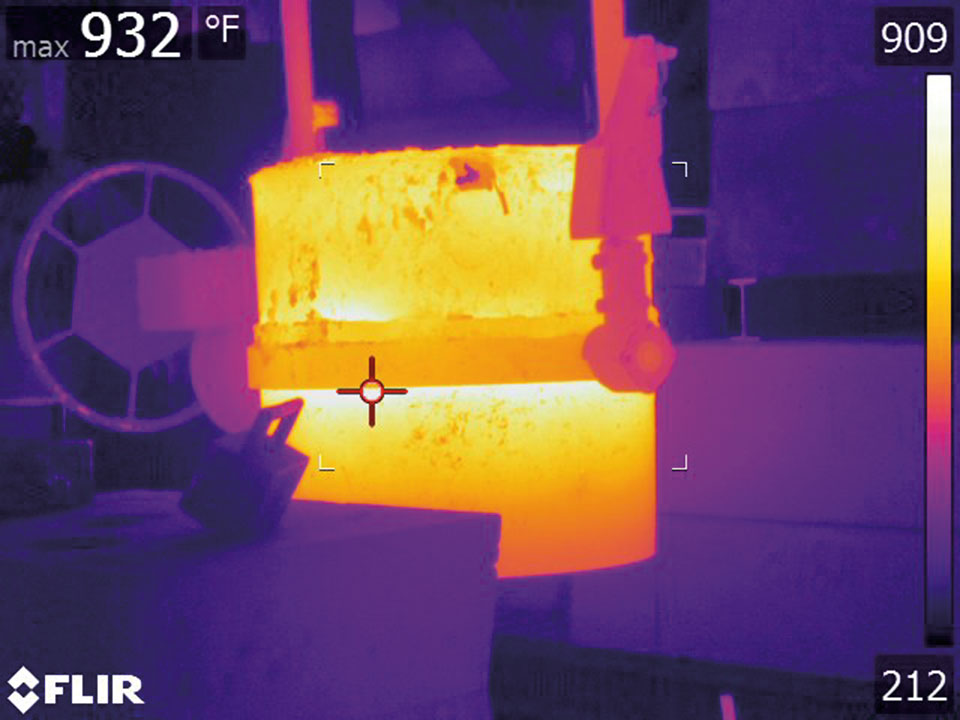
Regardless of the application, diagnosing a defect should be accompanied by root cause analysis to eliminate the true cause of the defect and prevent its recurrence. Only then can thermography deliver the maximum economic impact organizations expect when investing in this technology.