Power-MI API Connectivity for Seamless CMMS Integration
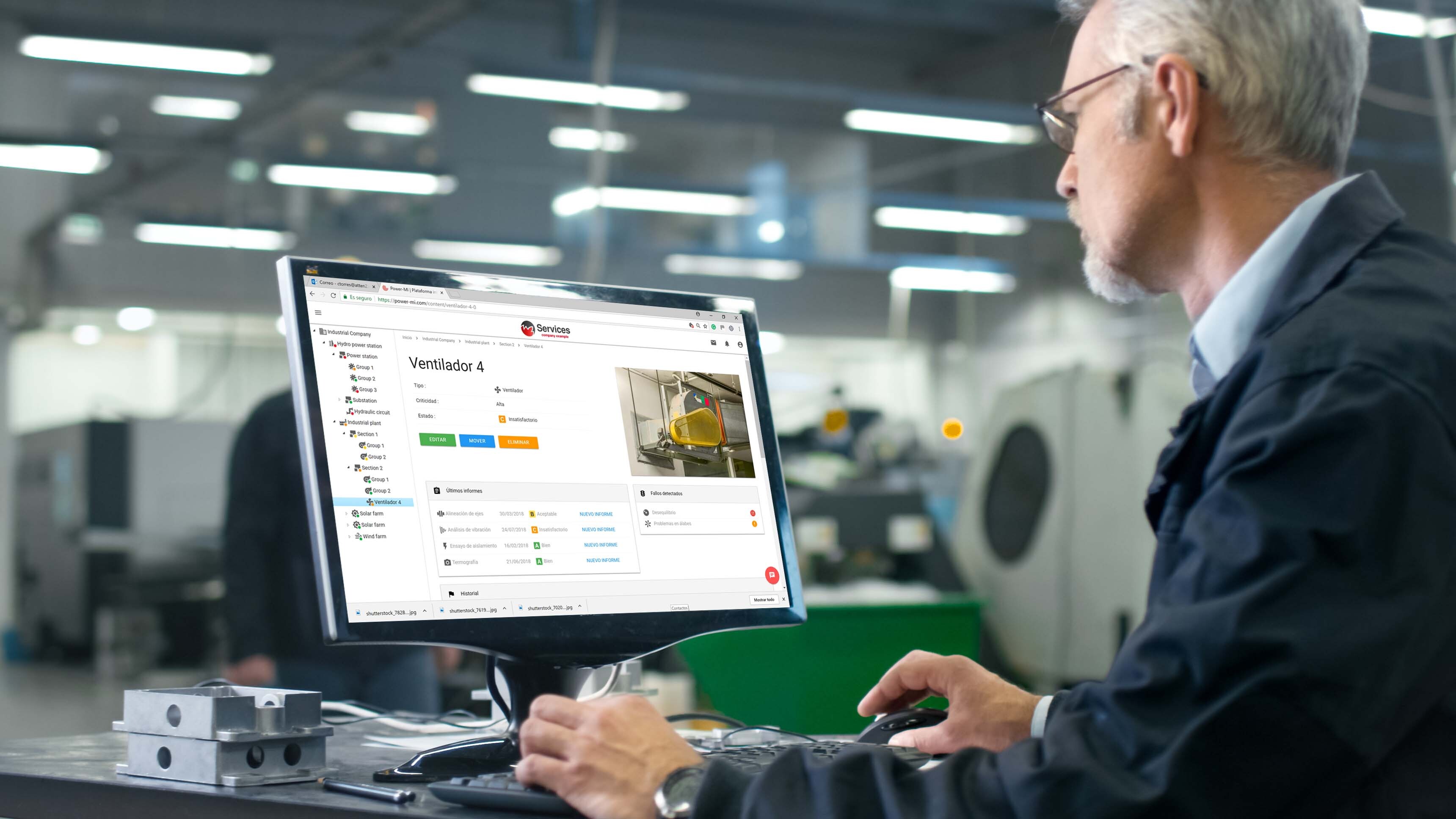
Automate Work Order Integration Between Condition Monitoring and Maintenance Systems
Power-MI complements your existing CMMS or ERP by focusing on predictive analytics and condition monitoring. Unlike traditional maintenance management software, Power-MI specializes in predictive maintenance management and condition monitoring, providing seamless API integration with systems like SAP PM, IBM Maximo, Oracle Maintenance, Infor EAM, Microsoft Dynamics, Fiix, eMaint, and Maintenance Connection. This API connectivity automatically transfers work orders generated from predictive maintenance reports directly into your existing CMMS, closing the loop between predictive analytics and maintenance execution.
Automate Work Order Management
Automatically generate and update work orders
When Power-MI identifies an equipment issue through predictive condition monitoring, work orders are created and automatically transferred to your CMMS, such as predictive maintenance management with SAP PM. This eliminates manual data entry and significantly reduces administrative effort.
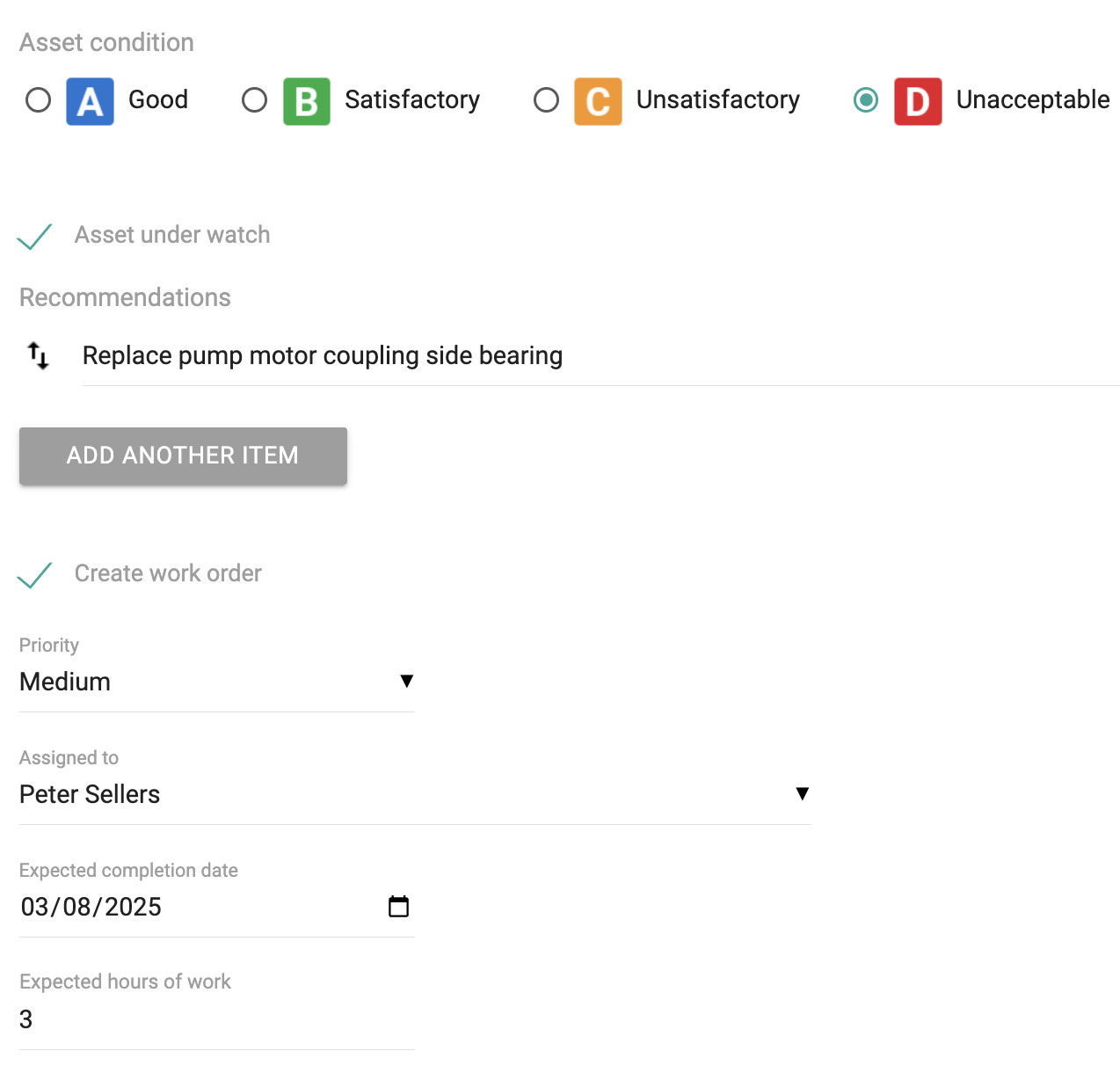
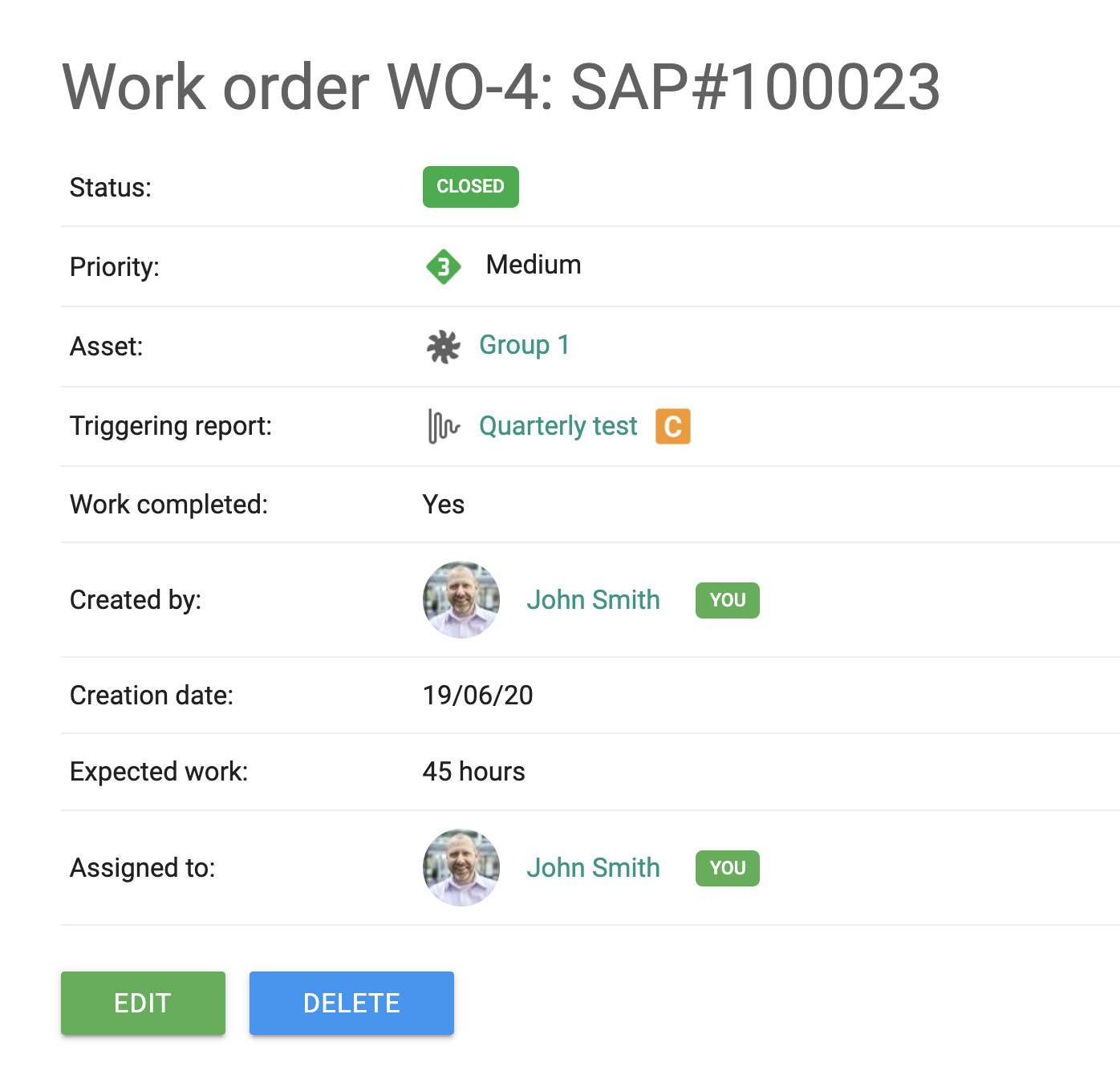
Real-time work order synchronization
As soon as a predictive maintenance report is generated in Power-MI, a corresponding work order is created instantly in your CMMS, such as SAP PM. Maintenance planners no longer need to manually input tasks, significantly streamlining operations.
Bi-directional status updates
When a work order is completed in your CMMS, its updated status is automatically synchronized back to Power-MI. This gives analysts immediate visibility into completed tasks, ensuring timely follow-ups and accurate maintenance recommendations.
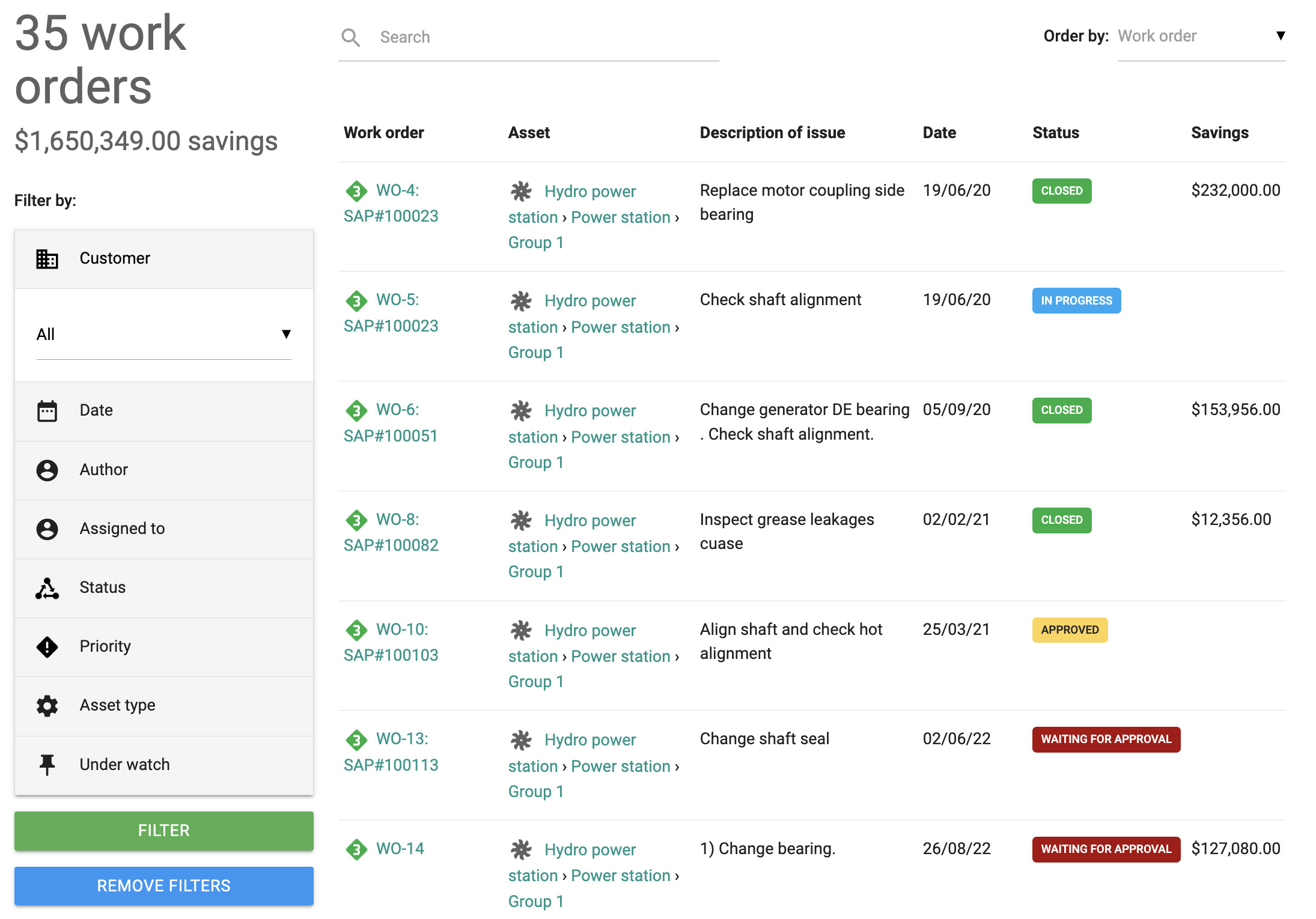
Control predictive maintenance workflows with Power-MI
Power-MI's API connectivity simplifies predictive maintenance management with leading CMMS platforms like SAP PM, enhancing your maintenance team's productivity.
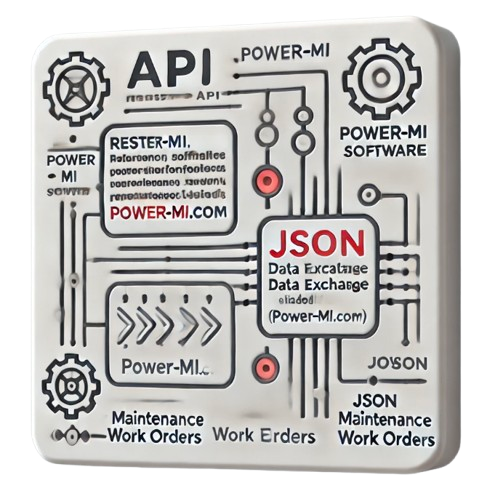
Complete maintenance event tracking
Power-MI captures all maintenance actions, including replacements and preventive maintenance executed in your CMMS. Analysts gain full visibility into the equipment's maintenance history directly within Power-MI, facilitating accurate and informed condition monitoring analyses.
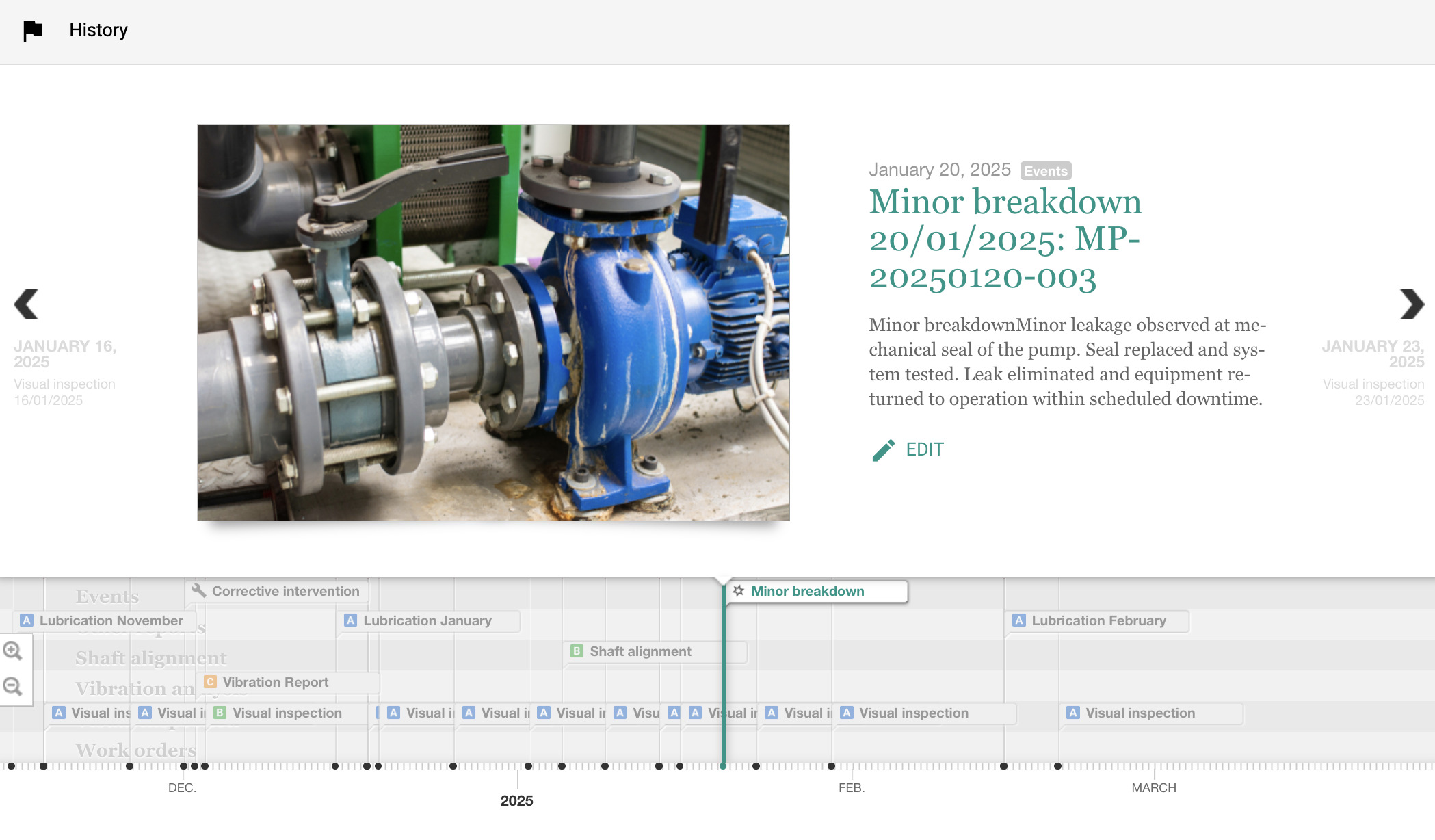
Predictive maintenance management with SAP PM: A typical scenario
- Condition Detection: Power-MI identifies a potential bearing issue from vibration analysis.
- Automated Work Order Creation: A predictive maintenance report triggers an automatic work order in SAP PM.
- Maintenance Execution: Technicians carry out the maintenance task and log details directly into SAP PM.
- Real-time Status Synchronization: SAP PM automatically updates Power-MI when the work order is completed.
- Verification and Reporting: Analysts verify corrective actions in Power-MI through post-repair condition monitoring, documenting the effectiveness of maintenance actions.
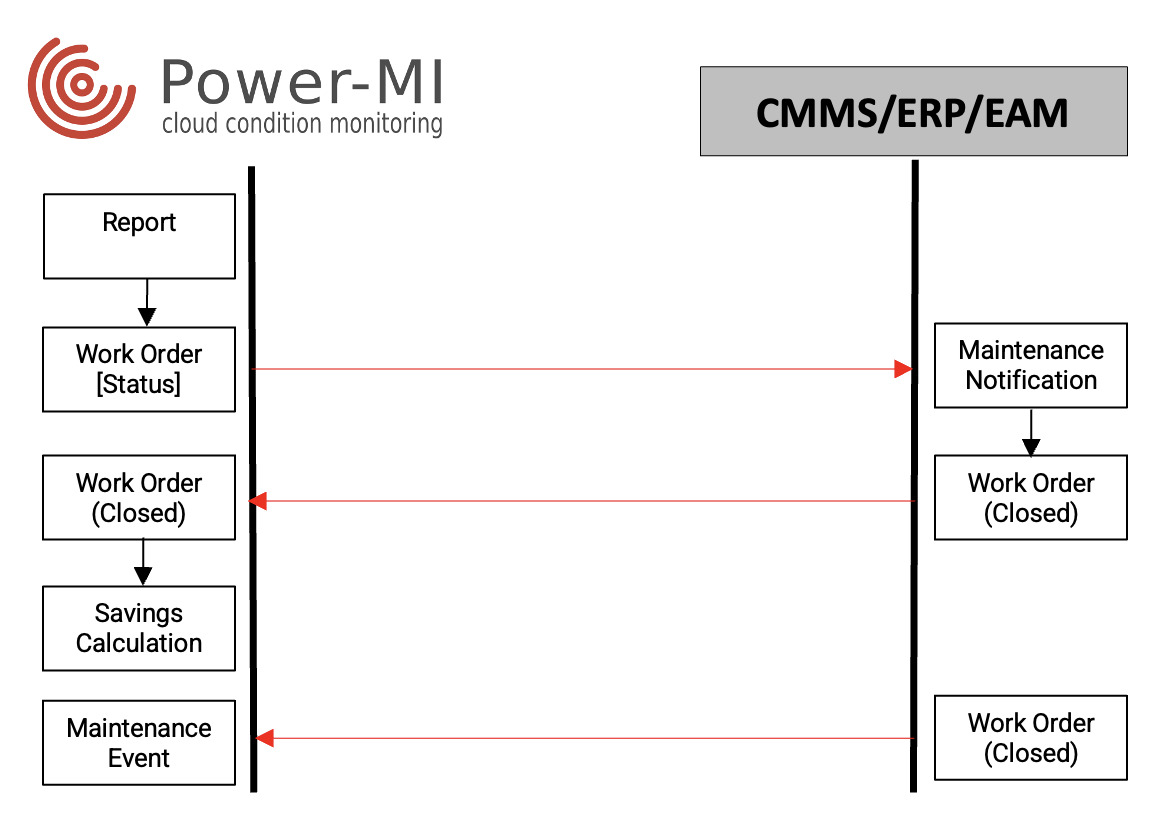
Benefits of API connectivity with Power-MI
-
done
Reduced manual data entry
Eliminate redundant data entry and improve accuracy by automating work order creation and updates between Power-MI and your CMMS.
-
done
Enhanced collaboration
Improve communication and collaboration between predictive analysts and maintenance teams, ensuring timely and informed maintenance decisions.
-
done
Real-time visibility
Gain immediate visibility into the status of maintenance activities, enabling proactive decision-making and optimized asset performance.
-
done
Comprehensive maintenance records
Automatically track and store all maintenance events in one place, providing predictive analysts complete historical context.
-
done
Streamlined maintenance workflow
Efficiently bridge predictive insights with actionable maintenance tasks, reducing downtime and enhancing reliability.
Get started with Power-MI API Connectivity
-
Discover
Schedule a live demo to see how Power-MI integrates seamlessly with your CMMS.
-
Plan
Collaborate with our team to configure API integration tailored to your maintenance processes.
-
Implement
Enjoy our expert assistance to rapidly deploy and integrate Power-MI with your existing maintenance systems.