Lubrication is an essential action to prevent surface friction and the resulting wear and temperature increases. Incorrect lubrication can be attributed to either insufficient or excessive lubrication. It is crucial to determine the appropriate lubricant and quantities for each application.
Insufficient lubrication often arises from improper lubrication programs or the use of unsuitable lubricants, leading to temperature increases. Conversely, excessive lubrication can cause leaks, seal failures, and unnecessary energy consumption due to increased lubricant viscosity, resulting in higher energy requirements for machine rotation. In motors, catastrophic failures can occur when lubricant enters the stator.
Contamination is a primary factor that affects proper lubrication, mainly caused by the presence of fluids generating oxides that reduce lubrication capacity, particles causing surface wear, and mixing of different lubricants due to seal failure or mishandling and storage of lubricants.
Lubricants should be stored under optimal environmental conditions, avoiding moisture and high temperatures, with containers closed and lubrication tools kept clean.
A successful lubrication program should employ procedures based on best practices, successful experiences, and known methodologies. Documentation, updates, and consistent application are essential to ensure tasks are performed consistently. Inconsistent lubrication methods dependent on individual execution can lead to unpredictable results.
An associated challenge with lubrication activity is personnel training. Large lubrication programs often rely on "lubrication masters," but their knowledge may not be effectively transferred to new personnel. Lubrication tasks should not be assigned to beginners, as even a minor error can lead to significant costs.
Comprehensive procedures should establish the correct sampling points, standardize lubrication guns for easy lubricant quantity control, apply labeling systems to minimize cross-contamination and human errors, provide lubricant information and lubrication intervals, install appropriate respirators to restrict particle and moisture ingress, use constant level lubricators with viewports for inspections, apply high-speed greases to avoid viscous drag in high-speed machines, ensure quality control systems meet maximum oil particle level requirements, and filter all lubricants before introducing them into the machine.
Implementing these measures will lead to better lubrication management in your industry. When combined with a Thermography Inspection program, it will lead to a competitive industry, aligning with the demands of the current times.
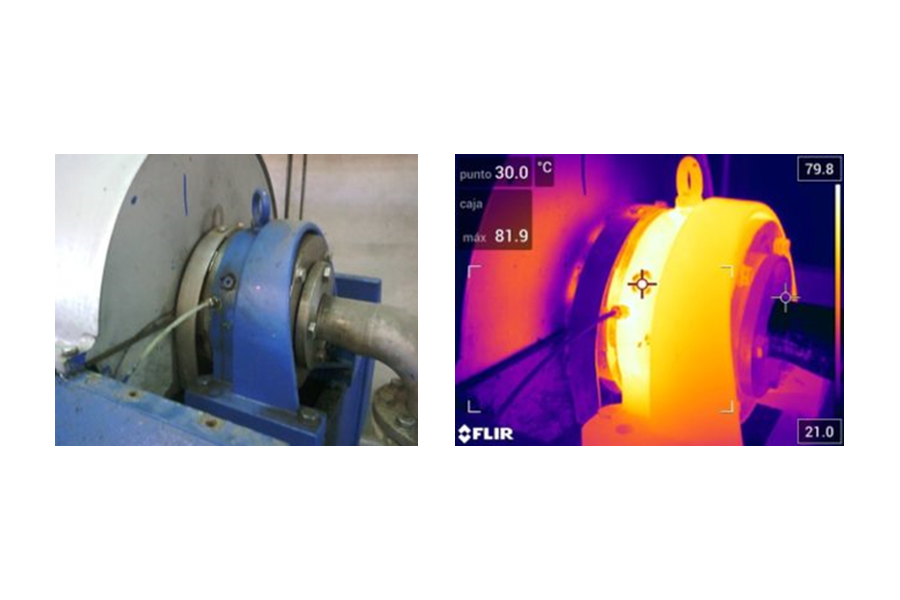