Leaks are accidental gas, vapor, or liquid outflows through a hole, joint, or opening in your container, pipe, channel, or drive system (pump or compressor).
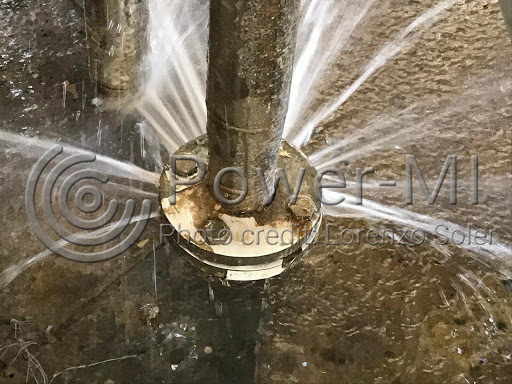
Causes
The most common leaks detectable by visual inspection are:
- Mechanical seals, packing, or packing failures.
- Welding failures.
- Cracks due to material wear.
- Bad assembly of joints.
- High porosity.
- Overpressure.
- Corrosion.
- Overloads in pipes or joints.
- High vibration.
- Settlement of land.
Cases
Through visual inspections the most common cases of leaks that are diagnosed are:
- Pump seals. These are usually due to seal wear, misalignment, or high vibration.
- Joints between pipes.
- Wear of material in pipes.
- Steam outlets in pressure vessels.
- Tanks and containers.
- Oil in hydraulic systems.
Diagnosis
Detection of leaks in visual inspections is by direct observation of the place of the leak, the liquid or the leaking vapor as well as by observing bubbles. It is also diagnosed by abnormal noise in cases of compressed air, steam, or pressurized liquids.
Points to consider:
- When you are not looking at the leak point or zone or the liquid or vapor directly, consider diagnosing moisture.
- Document the source of the leak with photographs if it is visible.
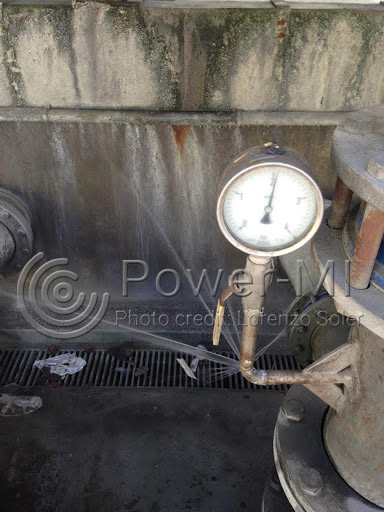