Corrosion is the wear, deterioration or alteration of a metal or alloy by a direct chemical attack or by electrochemical reaction with the environment or other material.
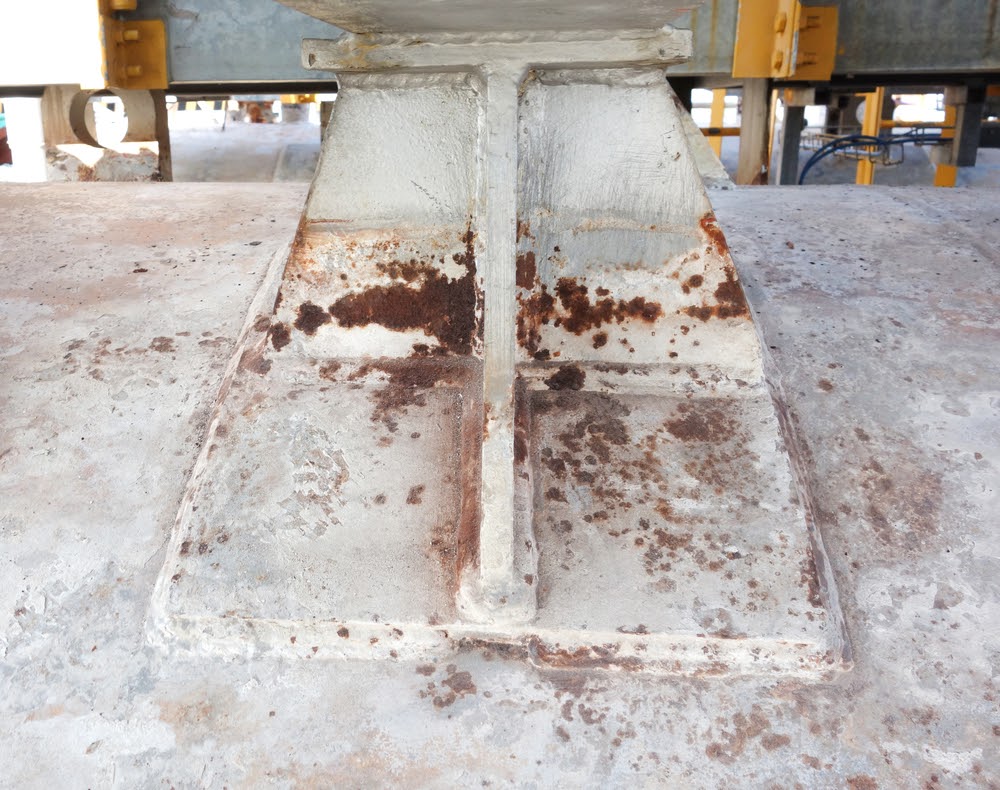
Causes
Corrosion can be broadly atmospheric and chemical. In both cases it is preceded by an oxidation process caused by a current of electrons that occurs when there is a potential difference between the two elements. The most common causes of corrosion detectable by visual inspection are:
- Lack of paint on metal surfaces.
- Lack of lubricant on metal surfaces.
- Contact between two incompatible metals (galvanic corrosion).
- Corrosive environments.
- Cracks and fissures.
- Humidity.
Cases
Through visual inspections the most common cases of corrosion that are diagnosed are:
- Structures in industrial buildings, tank support, cooling towers.
- Machine bases.
- Electric transformers.
- Electric connections.
- Metal towers.
- Bolts, washers, and nuts.
- Pipes, flanges, and their supports.
- Ceilings and their supports.
- Ground wires.
- Springs, springs, couplings, pulleys.
- Guides and rails.
- Internal and external surfaces of tanks, vessels, and pipes.
Diagnosis
Detection of corrosion in visual inspections is by direct observation or by effects of corrosion under paint or discoloration, wear, or spills.
Points to consider:
- When reporting corrosion include a photograph of it in your report.
- Mention in the report if the corrosion has caused the loss of visible material.
- Try to specify the effect of corrosion in the report (for example spots, corroded part, paint loss, leaks)
- If the corrosion is in a safe and accessible location, take a linear corrosion measurement if that better describes the failure.
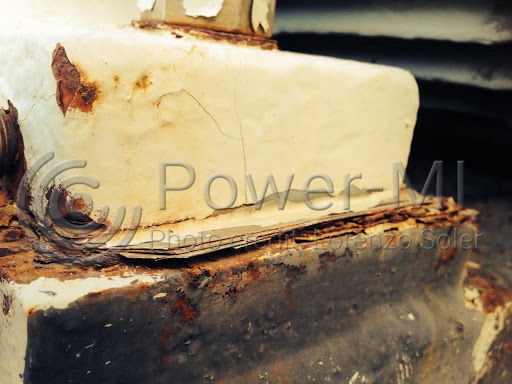