Pressure and vacuum measurements are used in visual inspections in predictive maintenance to assess the tightness of tanks and systems, or to monitor the operating conditions of an asset itself.
Pressure and vacuum can be measured by various techniques and gauges. The pressure gauge and pressure transmitter are commonly used in the industry.
Any pressure measuring instrument is commonly called a manometer. However, the manometer is an instrument that uses a column of liquid to measure pressure. A vacuum gauge is used to measure the pressure within a vacuum space, that is, below atmospheric pressure.
The pressure gauge is a low-cost instrument, it does not provide an electrical output signal and is used to take field measurements, which is why inspectors are charged with collecting its reading during a visual inspection.
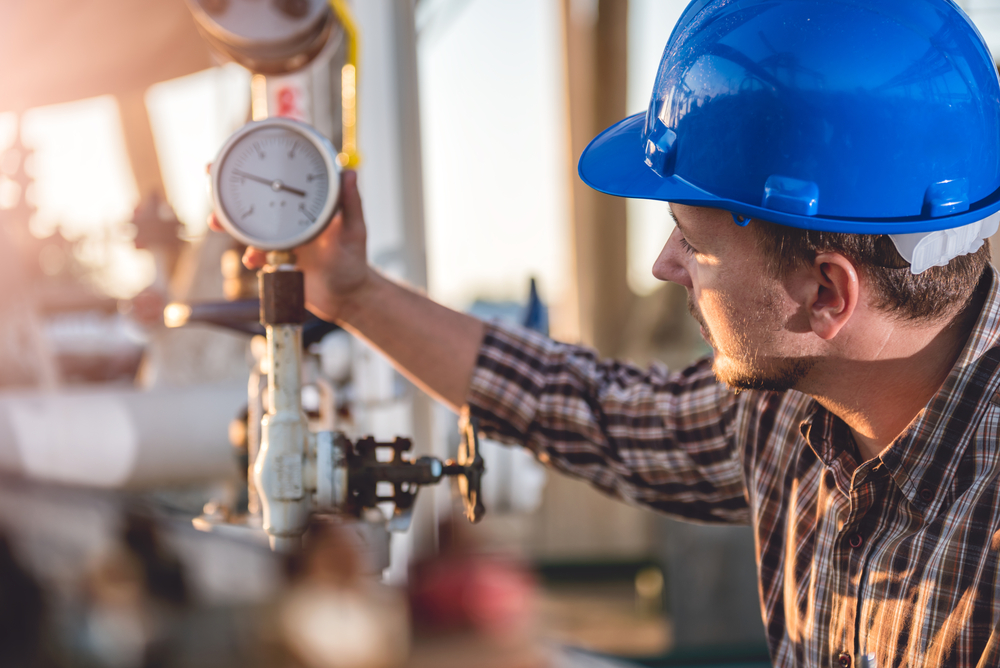
The pressure transmitter does provide an electrical output signal either analog (most common 4-20 mA) or digital. That is the reason why pressure transmitters are used in industrial process control, automation, and monitoring systems, although they can also be used to display pressure in the field using a screen.
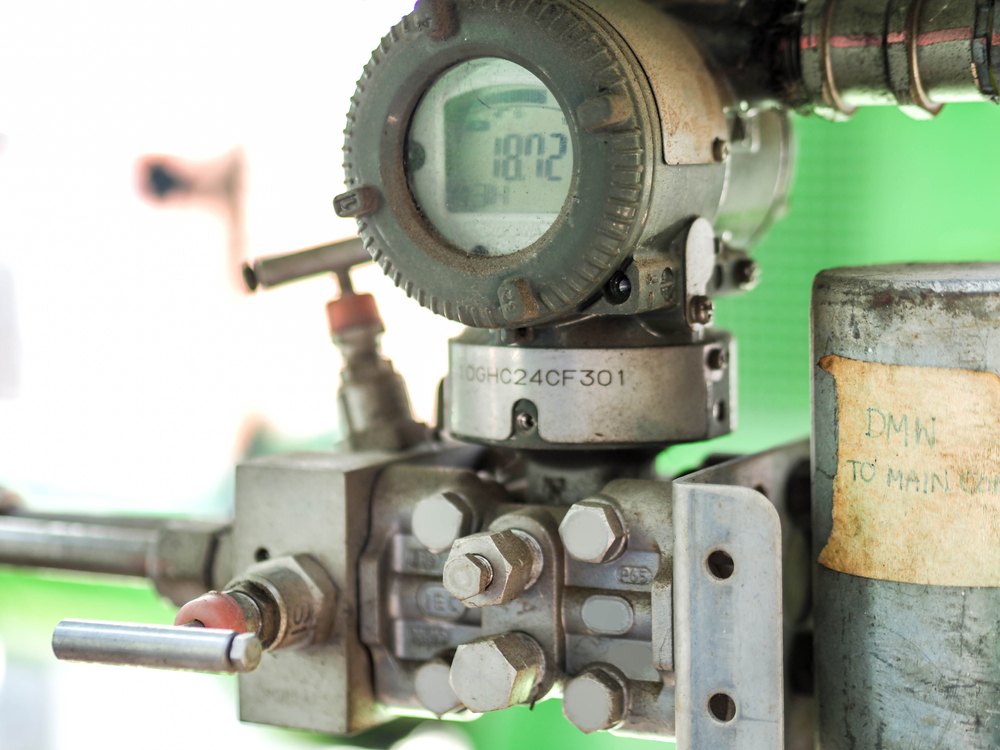
The pressure is a parameter that the visual inspector cannot measure with portable instrumentation that they carry with them.
When taking a reading of pressure parameters from a pressure gauge, the inspector must consider two sources of error:
- Parallax error: due to the distance between the needle and the base of the dial where the graduation or measurement is displayed.
- Movement of the needle (or indicator): they are due to mechanical vibrations in the pressure gauge or due to pressure fluctuations. Short fluctuations and vibrations can be attenuated by using glycerine pressure gauges.