Flow indicators are used in visual inspections of predictive maintenance both to measure the flow (or flow) of air, gas, steam or liquids, and to measure the volume of fluid consumed, transported or produced. Flow indicators are known as flowmeters, flow meters, flowmeters, or flow meters. When they are used to measure volume they are often called volumetric flowmeters.
Flow indicators can be mechanical or electronic. Likewise, they can be online or external. In-line they are when they are inside the pipe or interact directly with the fluid.
The most common type of mechanical flow indicator is the rotameter, which allows reading through an analog scale or through a tube. There are rotameters that additionally provide an electrical output signal.
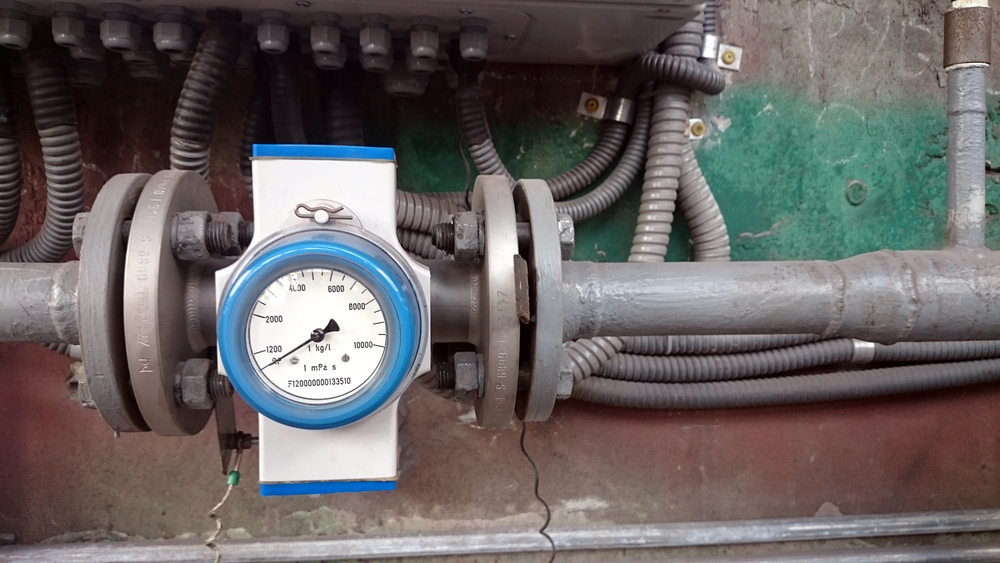
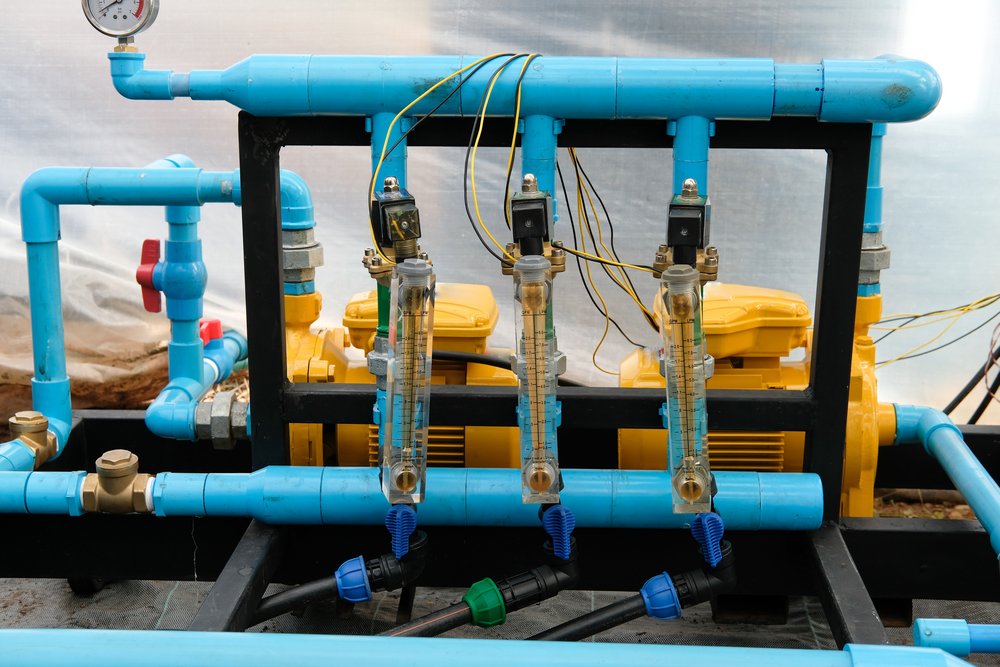
Electronic flow indicators provide an electrical output signal either analog (most common 4-20 mA) or digital. That is the reason why electric flowmeters are used in industrial process control, automation and monitoring systems, although they can also be used to show flow in the field using a screen.
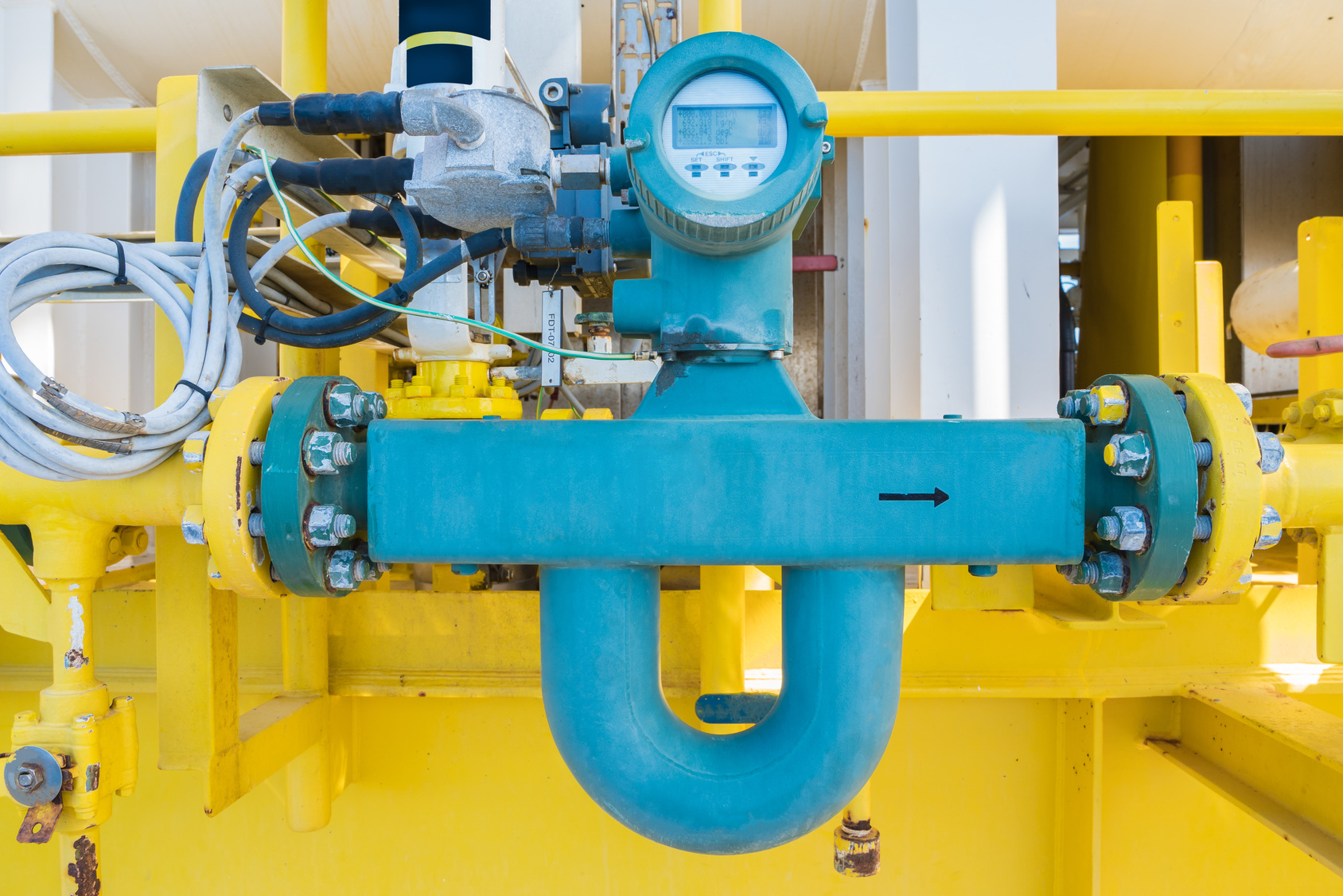
Flow can also be measured with portable instrumentation that the inspector can take with him. These work by the Doppler effect of suspended particles or gas bubbles (discontinuities) within the fluid. A disadvantage for visual inspections is that not all portable flowmeters work in all applications, since the measurement only works for liquids, and depends on the size and quantity of particles in the liquid, minimum and maximum flow, temperature, size and thickness of the pipe, and the pipe must run full and with laminar flow. Different probes or equipment may need to be purchased for different applications.
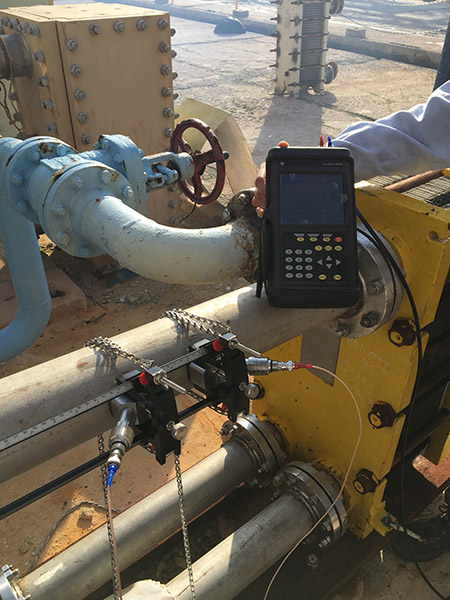