In predictive or condition-based maintenance, we evaluate the state of the mechanical or electrical components through monitoring and analysis techniques, allowing us to schedule maintenance operations "only when necessary". It essentially involves evaluating the state of mechanical or electrical components through monitoring and analysis techniques, such as vibration, temperature, oil contaminants, and insulation, among others. The study of these parameters provides us with information on the state of the components and importantly, the way in which the equipment is operating, allowing for the detection of not only component problems, but also issues related to design and installation. The goal of predictive maintenance is to reduce operating and maintenance costs by increasing the reliability of the equipment.
The basis of predictive maintenance lies in monitoring the equipment since we must evaluate the above parameters with the installation in normal operation. Therefore, it is not necessary to stop the assets to evaluate their condition, as we can continuously monitor the condition of our machines while they are in operation.
With the different techniques available, we can evaluate the faults in the components and follow their evolution for long periods of time (sometimes months) before deciding to trigger an intervention, so we can schedule together with production the most appropriate time for maintenance interventions.
To achieve success in implementing a predictive maintenance program, a clear strategy must be followed. Implementing it across all assets without a plan, or attempting to implement multiple technologies simultaneously, is likely to result in failure. Additionally, it is important to have an adequate information management system to handle the data correctly, as this is essential to effectively manage the program and avoid wasting a significant economic investment.
It will be necessary first to make a selection of the assets that we are going to monitor; this will be driven by a series of factors amongst which are the criticality or importance of the asset, its accessibility and its related technical information available. We will focus on a small number of them, analyzing which technique we can apply first, usually vibration analysis which is the most widely used. A pilot program will be carried out with this selected group of assets, locating defects, analyzing root causes and feeding the system with feedback once defects have been eradicated.
After every measurement campaign the result of each machine analysis will be written into a report to feed our information management system. Cloud-based collaboration and delivery solutions like Power-MI can greatly reduce the time and burden related to the creation of these reports, providing instantly accessible prioritized and summarized information needed for insightful decision making. Integrating the whole set of condition monitoring data available onto a common data repository greatly improves the diagnostic capabilities. However, there may be even more important benefits to this process, since at the same time it breaks down the traditional organizational barriers that have kept each group of people focused on their respective technologies or areas of expertise.
Once we have obtained positive results from our pilot experience, we will proceed to gradually expand the program to more assets, ultimately achieving comprehensive implementation with the integration of different technologies and effective management of the data obtained.
Technical and economic justification of predictive maintenance
The technical justification of predictive maintenance is pretty obvious, because it allows for a comparison of the actions taken during preventive or corrective maintenance with those that would be necessary with continuous monitoring and surveillance of measured parameters.
When we only perform corrective maintenance, the term "maintenance" is synonymous with "repair". This does not mean that this type of intervention should not happen. In fact, the ultimate aim of any maintenance work is to repair or replace damaged components to extend the machine's life; corrective interventions are inevitable. Nevertheless, focusing all maintenance actions on this sole purpose is a mistake. This approach only offers one advantage, a low initial investment cost, but comes with significant drawbacks:
- Unexpected stops usually occur when production must be higher, i.e., at the worst time.
-
These stops are often catastrophic, as they often lead to significant damage. Sometimes for the loss of a bearing, we can seriously damage the transmissions.
- The costs of repairing them become very high.
-
The need to have spare parts in storage increases with the uncertainty of what can fail.
- The risk of accidents increases.
-
We are totally unaware of the actual condition of our machines.
- We accept chronic failures without investigating the root cause; for example, if a bearing deteriorates prematurely and we simply replace it, we may be overlooking a problem of misalignment or unbalance that could be causing the premature damage.
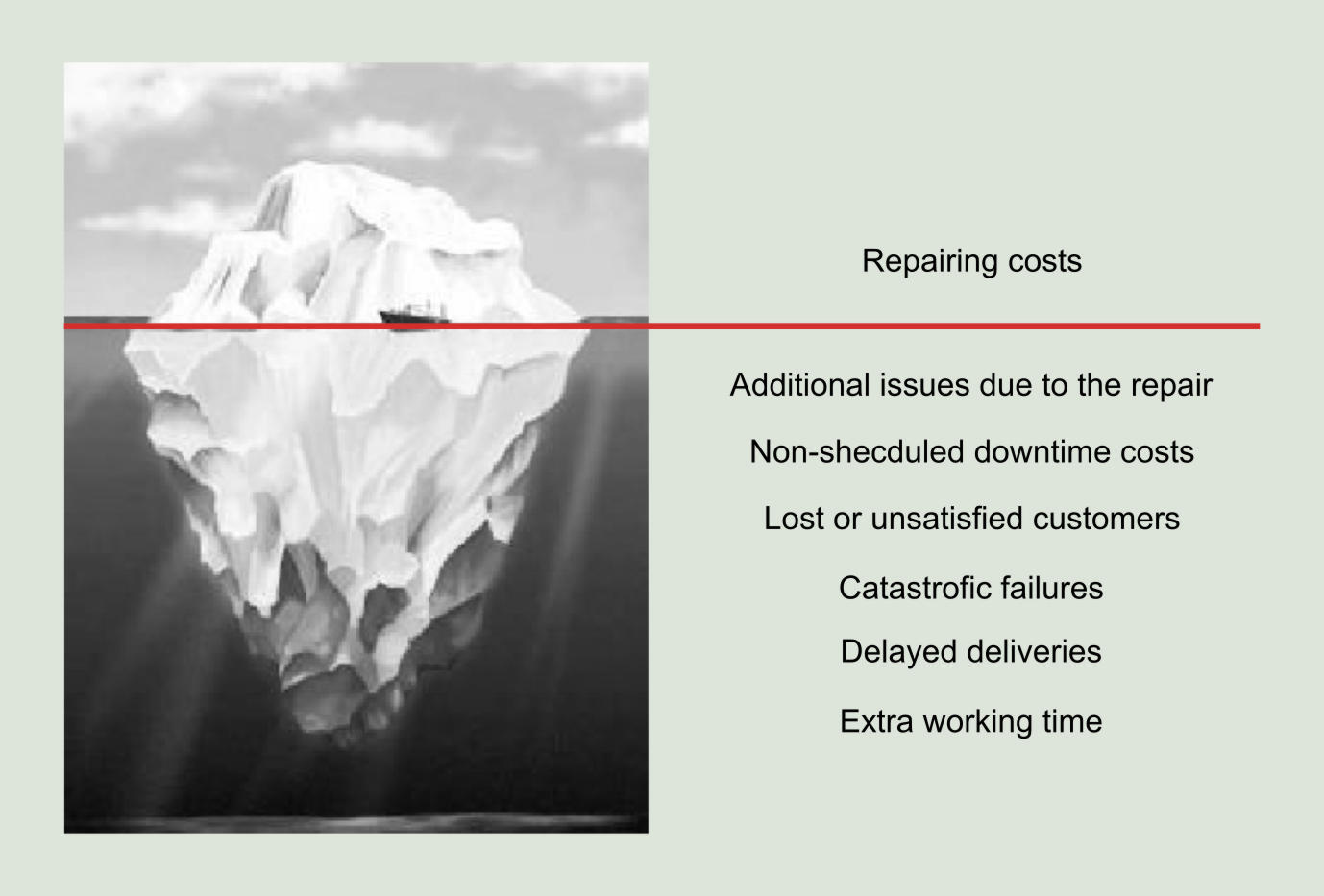
Another approach is preventive or scheduled maintenance, which involves replacing components based on the assumption that their useful life has been reached. The expected lifespan of each component is typically provided by the original equipment manufacturer, who also usually provides preventive maintenance guidelines, including recommended intervals for component replacement and lubrication.
Clearly, this way, we can avoid failures. Still, we must be careful with the application of this approach since, for example, rolling element bearing manufacturers indicate in their catalogs that "the average bearing life is approximately five times the nominal life (SKF 4000/IISp General Catalog, Page 27)". This means that if we extend the usage of bearings to their actual duration, we will increase five times its useful life, and this argument alone is, in many cases, enough to justify the monitoring of certain machines.
However, preventive maintenance also has its drawbacks:
-
The main issue is to intervene in a machine that works properly simply because it is time for an intervention. Machines in operation reach a certain operation balance that is difficult to reestablish once we intervene on them, and with preventive actions, we are constantly disturbing this operation balance.
-
When we act on the machine, we change components that are typically in good condition, but we only know its actual condition once we disassemble it.
-
We can change components that have exhausted their theoretical life and not be aware of others in poor condition. We have no control over hidden damage.
-
Regarding cost, it can grow rapidly due to the frequent interventions in the machines, many of which are unnecessary.
Predictive maintenance may involve initial challenges such as higher investment costs for technology and training, but it ultimately yields a return on investment over the medium and long term. Nevertheless, the advantages are obvious:
-
We know the machine's condition at all times.
-
We eliminate the great majority of faults.
-
We only stop or intervene in the machine when it is really necessary.
-
We know the damage in components from an initial phase, allowing us to schedule their replacement at the most convenient time.
-
When intervening in the machine, we already know the problem, reducing the repair time.
-
We can identify hidden faults as well as the root cause of chronic failures.
-
We reduce the number of spare parts in the warehouse by purchasing them only when we detect the problem in an initial phase.
-
We get bonuses on insurance premiums.
-
We increase the safety of the plant.
The best tool to understand predictive maintenance is a trend plot in which, on the ordinate axis, is evaluated one of the parameters we are measuring (vibration severity, temperatures, contaminants, etc.), and on the abscissa, time is displayed. While the severity of our parameter remains stable, we do not have to worry (the asset is ok), but from the moment when it starts rising we have an indication that something is wrong. With the different analysis techniques applied to these parameters, we can determine with extraordinary precision the root cause or origin of the damage.
Due to their clear importance, it deserves a particular mention of the definition of alert and alarm limits. Although there are several ways of establishing them, it is necessary always to have a history of measures that allows us to carry out a statistical study of them.
The economic benefit of predictive maintenance is beyond any doubt, as can be demonstrated with real data from companies from different sectors where it has already been implemented or is in the process of implementation. The evaluation of this profitability is not simple, and to be more accurate is necessary to have historical asset information, although it is always possible to make an estimation of the direct costs that have been avoided. Still, without the need to declare "catastrophes" being avoided, attractive returns are produced to allow competition with other projects searching for funding.
Finally, it is interesting to mention an additional application of predictive techniques, and one not directly related to maintenance, that is, its use in the reception of equipment as a method of verification of its correct operation or the quality of repairs that have been carried out.