Air Gap Monitoring in Motors and Generators
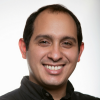
Before talking about air gap monitoring in motors and generators, it is essential to clarify an electric motor or generator's air gap and what it does.
What is the air gap?
A simple way to define the air gap is to say that it is the air in the space between the stator and the electrical machine's rotor.
Being more specific, we can have similar definitions for alternating current or AC electrical machines and direct current or DC machines.
According to The Electro-mechanical Authority (EASA), in AC machines, the air gap is the air space between the rotor cores and the stator. On the other hand, it is said to be the space between the inter-poles and the armature for a DC machine.
What is the working principle of the air gap?
To understand the working principle of the air gap, it is first necessary to remember that both electric motors and generators are rotating electrical machines.
This means that both electric motors and generators have very similar operating principles. The difference is that an electric motor transforms the supplied electrical energy into mechanical energy. In contrast, the electrical generator takes advantage of specific mechanical energy and converts it into electrical energy.
In both cases, the energy transformation process happens when the stator and rotor work together to generate a magnetic flux through the copper windings that each one has. And this is where the air gap comes into play.
A magnetic field is formed in the air gap, and one of the windings mentioned above is responsible for generating the flux that must move through the air gap and cross it two times for each pole that the electrical machine has for each phase.
Some critical factors related to air gap operation are:
- The magnetic force is inversely related to the square of the distance. The magnetic attraction force is reduced and is more difficult to control as the size of the air gap increases.
- Increasing the air gap's size increases the magnetizing current, which represents the amount of current needed to drive the magnetic flux through the air gap.
- The greater the number of poles on the motor or generator, the greater the number of times the flux must cross the air gap for each revolution.
All these factors lead us to conclude that a small air gap is better. However, a smaller air gap means less separation between the rotor's moving parts and the stator. This is why it is crucial to monitor the air gap in motors and generators since the slightest variation in its uniformity with these characteristics can generate operating problems in the machine.
How is the air gap monitoring carried out on motors and generators?
Monitoring the air gap works very well to determine the condition and dynamic behavior of the machine. Since the air gap is a central part of the motor or generator and is the interface between mechanical and electrical forces, it is straightforward to identify problems by monitoring them.
Next, we will see some of the sensors, instruments and equipment used to monitor the air gap in motors and generators:
Capacitive Sensor Systems
Systems with capacitive sensors can be installed on the stator to measure the air gap under different operating conditions. These sensors are resistant to extreme environmental conditions and the induction of eddy currents.
Through these systems, different tests such as load rejection tests can be performed, which are carried out to verify the machine's mechanical rigidity and balance during the commissioning tests of new or rebuilt units. This test shows the rigidity of the rotor and stator, the shaft's alignment, and the machine's vibrational behavior.
Other tests include:
-
Evaluation of the relative thermal expansion of the stator.
-
Stator collapse of bulb-type generators.
-
Behavior of the air gap during start and stop.
Sideband Frequency Spectrum Analysis System
Using systems with conventional current sensors and other types of meters, such as Rogowski coils, it is possible to measure sideband frequency spectra to determine both mechanical and electrical failures in motors and generators.
With these systems, it is possible to perform the Current Signature Analysis, also known as CSA. It is possible to detect variations in the air gap that can mean eccentricity problems; in other words, a misalignment of the rotor to the magnetic center of the stator.
Systems With Accelerometers
These types of systems that use sensors called accelerometers are the most common in vibration analysis. As explained in the article Vibration Analysis of Electric Induction Motors, vibration analysis allows diagnosing electrical problems related to an uneven air gap between rotor and stator.
The following image shows some of the problems detected by the Motor Current Signature Analysis (MCSA), vibration analysis, and other types of analysis both in motors and in the equipment attached to them.
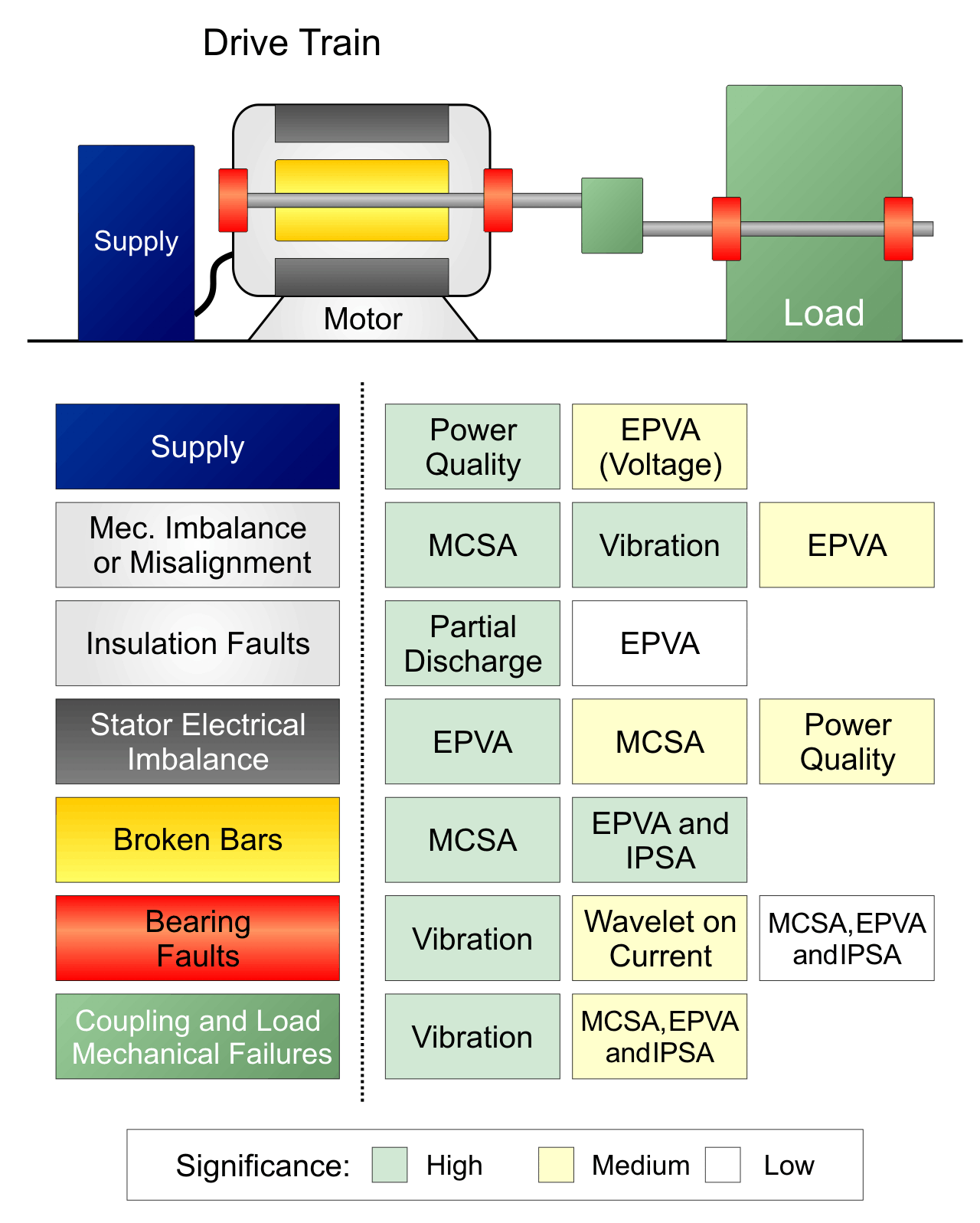
What failures can be detected by monitoring the air gap in motors and generators?
As mentioned above, the monitoring of the air gap in electric motors and generators allows detecting both mechanical problems and electrical problems, among which are:
- Eccentricity (static and dynamic)
- Imbalance
- Misalignment
- Bearing issues
- Abnormal noise
- Deterioration
- Electrical issues
- Faulty connection
- Open circuit
- Abnormal process parameters
What is Power-MI?
Power-MI is a cloud based solution that allows you to design & manage your condition-based maintenance plan integrating all techniques into one platform. Easy reporting, automatic work orders and CMMS integration.
Read more