Vibration Analysis of Centrifugal Pumps
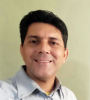
Pumping systems are critical factors in the industrial process; there are different types of pumps to meet the various production needs. Centrifugal pumps are perhaps the most abundant in industrial process applications. Within the classification of industrial pumps, centrifuges are called dynamic pumps and are subdivided into axial flow pumps and radial flow pumps, with one or several stages, horizontal or vertical, with open, semi-open or closed impeller, among other features.
A centrifugal pump is a rotodynamic hydraulic machine that transforms the mechanical energy of the impeller into kinetic or pressure energy by transmitting it to an incompressible fluid. The fluid enters through a suction pipe towards the center of the impeller, which has a series of blades to move the fluid utilizing centrifugal force towards the discharge pipe, passing first through the volute or body of the pump or to other impellers in the case of pumps with more than one stage.
Main parts of a centrifugal pump
The parts that make up a centrifugal pump are:
- Suction pipe
- Impeller or rotor
- Shaft
- Casing or volute
- Bearing
- Bearing housing
- Mechanical seal
- Discharge pipe
Vibration measurement points
As we have already discussed in a general way in our article "Where to place the vibration sensor", in a centrifugal pump, the inspection points for vibrations must correspond to the centerline of the shaft, on the bearing housing. Ensure a stable mounting on a solid part. Whenever possible, make measurements in the horizontal (H), vertical (V) and axial (A) directions of each bearing.
Safety is the priority to select vibration monitoring points. On the coupling side, it should not be measured in the axial direction unless all safety guarantees are available. Some parts of the pump, such as mechanical seals and their pipes, are usually hot, care must be taken not to make contacts with these parts, a cable of the measuring instrument in contact with a hot pipe can burn.
Some analysts take pump bearings at a single measurement point in case of small pumps.
Typical failure modes in centrifugal pumps
Imbalance
In centrifugal pumps, imbalance is usually caused by one of the following causes:
- Non-uniform impeller wear (for example by cavitation) or blade breakage.
- Bad coupling condition, beaten, deformed.
- Bad winding of the motor rotor.
- Wrong balancing procedure in the workshop.
- Standard or inappropriate balancing quality.
When an imbalance is detected in a centrifugal pump, the following actions may be recommended:
- Check impeller wear and analyze the origin of wear.
- Check the coupling runout and its overall condition.
- Check the balancing procedure in the workshop and the degree of quality applied.
Misalignment
In centrifugal pumps, misalignment is usually caused by one of the following causes:
- Bad installation or improper alignment procedure.
- Pipe tension
- Soft foot
- Thermal expansion both in the pump itself or in its pipes.
- Lack of staff training.
- Inappropriate or uncalibrated measuring instruments.
When a misalignment is detected in a centrifugal pump, the following actions may be recommended:
- Verify the alignment procedure used and the standards applied.
- Verify if there are pipe tension and soft foot, both of the pump and the motor.
- If safety conditions permit, measure alignment with the machine just stopped or hot.
- Make a record of alignment displacement during the machine heating process: thermal expansion.
Bearing issues
In centrifugal pumps, bearing issues are usually caused by one of the following causes:
- Bad installation
- Defective lubrication or greasing
- Contamination of particles in grease or lubricant
- High temperature
- Misalignment and unbalance
- Improper bearing selection
When bearing issues are detected in a centrifugal pump, the following actions may be recommended:
- Replace the bearing and make a root cause analysis
- Do a grease study of the bearing
- Review bearing mounting practices
- Review bearing lubrication practices
- Verify pump alignment and balancing
- Check if the operating conditions are suitable for the bearing
Leaks
In most cases, leaks in centrifugal pumps occur in mechanical seals. The causes of the deterioration of the seals can be:
- High vibration due to misalignment or imbalance
- Bad mounting
- Overheating of the seals when operating the pump without load or dry
- Bad seal selection
When seal problems are detected in a centrifugal pump, the following actions may be recommended:
- Check the condition of the alignment and balancing of the pump
- Review mechanical seal installation practices
- Prevent the pump from running dry
- Check if the operating conditions are suitable for the mechanical seal
Rotating looseness
In centrifugal pumps, clearances are usually caused by one of the following causes:
- Excessive bearing wear
- Bad mounting
- Improper selection of bearings or bearing housing
When rotating looseness gaps are detected in a centrifugal pump, the following actions may be recommended:
- Check the condition of the bearing
- Check if the bearing housing has wear or deformation
- Review bearing mounting practices
Structural issues
In centrifugal pumps, structural looseness is usually caused by one of the following causes:
- Bad bench foundation
- Base plate deformed or warped
- Wear of bench supports or silent blocks
- Loose bolts that could also produce soft foot
When structural looseness is detected in a centrifugal pump, the following actions may be recommended:
- Reinforce the structure on which the centrifugal pump is supported
- Recondition the centrifugal pump foundation
- Change bench supports, insulators or silent blocks
- Tighten the fastening bolts of the centrifugal pump with a torque wrench
Fluid dynamics issues
In centrifugal pumps, hydraulic issues are varied and are usually caused by one of the following causes:
- Cavitation
- Recirculation
- Overload
- Flow turbulence
- Pump in operation out of design
When hydraulic issues are detected in a centrifugal pump, the following actions may be recommended:
- Check the suction conditions of the centrifugal pump
- Check the impeller and pump volute for damage
- Check if the operating conditions (flow and pressure) are per the design of the centrifugal pump
Other predictive technologies
The inspection of a centrifugal pump must be comprehensive, including dynamic, thermal, and operational behavior. The following technologies also apply to centrifugal pumps:
Predictive technology | Detectable failures | |
---|---|---|
![]() |
Visual inspections | Leaks, cleaning, abnormal noise, loose parts, instrumentation readings. Operational variables, such as performance and efficiency (pressure, flow, amperage, temperature) can be included. |
![]() |
Thermography | High temperature (mechanical seal or bearings), defective connection. |
![]() |
Ultrasounds | Bearing issues. |
![]() |
Oil analysis or tribology | Degradation of the lubricant (grease), water content, contaminants, bearing wear. |
Norms and standards:
The permissible vibration limits for centrifugal pumps can be found in API 610 standard or ISO 10816-7.
What is Power-MI?
Power-MI is a cloud based solution that allows you to design & manage your condition-based maintenance plan integrating all techniques into one platform. Easy reporting, automatic work orders and CMMS integration.
Read more