Soft Foot in Rotating Machinery
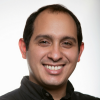
Although it is usually completely ignored during maintenance activities, the soft foot in rotating machinery is a significant problem that must be detected and corrected before it creates bigger problems and severe damage to the machines.
What is the soft foot?
The soft foot is a problem found in rotating machinery, which can be compared with the problem found in a chair that has a longer or shorter leg than the rest. In the case of a soft foot in rotating machinery, it is also possible to find a foot with a different angle, bent, warped, twisted, or damaged baseplate.
As it happens to the chair, this problem generates instability. This instability results in the machine operating at very high and harmful vibration levels.
There are four types of soft foot, which are:
- Parallel soft foot: in this case, there is, at least, one foot that is not in contact with the same plane as the rest. This generates a visible gap between the foot and the baseplate.
- Angular soft foot: it is found when the foot is bent, and it only touches the base at one point, whether it is the inner or the outer side of it. A visible angle is formed between the bottom of the foot and the baseplate, hence the name.
- Squishy soft foot: it refers to a soft foot resulting from using too many shims or generated by extreme corrosion and excessive dirt under the foot. It usually happens after the bolts are loosened to perform the alignment of the shafts, which allows sediments and residues to accumulate in that area.
- Induced soft foot: as the name suggests, this type of soft foot is generated by external forces. It is usually found in machines that are attached to pipes that generate high tensions.
Causes of soft foot
There are different causes of a soft foot in rotating machinery, which can be grouped depending on the type of soft foot generated.
Causes of the parallel soft foot
This type of soft foot in rotating machinery is generally a result of:
- One of two feet being too short.
- The baseplate or the installation pads are not on the same plane.
- Insufficient shimming under one foot or two diagonally opposite feet.
- Loose bolt.
Causes of the angular soft foot
In this case, the possible causes are:
- A machine that has been dropped or has suffered any kind of strong blow.
- Mishandling of the machine during transportation, installation or any maintenance activity.
- Badly machined or bent baseplate.
- Severe misalignment generates tension on the feet of the machine.
- Welded foot.
- Damaged foundation.
- Cracked foundation as a result of temperature changes and other environmental effects.
Causes of the squishy soft foot
The following causes produce this type of soft foot in rotating machinery:
- Weathering or chemical processes that damage (generate corrosion) the feet.
- Excessive shimming.
- Damaged or bent shims.
- Dirt and debris accumulated under the foot.
- Shims with burrs or thread marks.
Causes of the induced soft foot
We can mention the following causes for this case:
- Tensions in the case of pumps attached to pipes that tend to lift the equipment.
- External forces that affect the machine frame, such as the stress generated by the coupling.
- Tensions due to overhang installation.
- Loads generated by belts and chains on pulleys and gears.
- Jacking bolts which are left fully tightened by mistake.
Effects of the soft foot
Although it may seem that the soft foot is not a serious issue, the effects that result from it are quite important. The most relevant effects of the soft foot in rotating machinery are:
- Mechanical and quality issues.
- Misalignment.
- High levels of vibrations can generate other faults.
- Accelerated wear and tear of inner components and the structure.
- Metal fatigue and distortion.
Issues related to not detecting the soft foot
Detecting soft foot while performing alignment is vital since it allows to avoid different issues, including but not limited to:
- Increased energy consumption.
- Bearings and seals early failure.
- Unplanned downtime may affect efficiency and productivity.
- Time and money losses.
- Health and safety issues.
How to detect a soft foot
Detecting a soft foot while performing alignment is possible by following these steps:
- When using the alignment equipment, the laser and the sensor are placed on the shaft, and the function to measure the vertical displacement of the equipment is selected. This will measure the displacement resulting from loosening a bolt in the base.
- Repeat the process for the 4 or 6 feet the machine may have.
- The alignment equipment calculates the distance the machine is moving and determines whether there is a soft foot. If the result is in the range of 0.002 inches (0.0508 millimeters) to 0.003 inches (0.0762 millimeters), then there is a soft foot.
Another way to detect soft foot is by observing whether there is shaft deflection or not or utilizing vibration analysis since the soft foot in rotating machinery generates high levels of vibrations. Also, phase analysis can be useful by studying the relative movement between two parts of the machine, such as the frame and the foundation.
When studying the machine’s current, a peak at 2X of the alternate current line frequency may indicate a soft foot.
Correcting the soft foot
At this point, it is important to highlight that, to correct the issues mentioned above, the correction of the soft foot must come before the alignment of the shafts.
There is a formula used to calculate the necessary adjustment to correct the soft foot. This is usually integrated into the majority of the alignment systems. Using feeler gauges is also possible to determine the gap between the foot and the baseplate, especially in the case of a parallel soft foot.
Once the type of soft foot and the necessary adjustment are determined, the following recommendations should be applied:
- Shimming the foot or feet according to the necessary adjustment. If any shim(s) is protruding, trimming and eliminating the protrusion is recommended.
- Machining the foot, the baseplate or both if necessary.
- Cleaning the area between the foot and the baseplate to eliminate any type of dirt or sediments may harm the machine’s feet.
- Replacing damaged and bent shims.
- Performing any modification required to eliminate possible external forces affecting the machine.
What is Power-MI?
Power-MI is a cloud based solution that allows you to design & manage your condition-based maintenance plan integrating all techniques into one platform. Easy reporting, automatic work orders and CMMS integration.
Read more