Robots are generally used for visual inspections by remote operation. There are already robot options on the market equipped with video cameras and lighting systems. Additionally, other monitoring technologies are used in robots, such as: structural ultrasound, thermography or electromagnetic systems. Through the use of robots, visual inspections can be made in places with restricted access such as access in dangerous areas for the inspector.
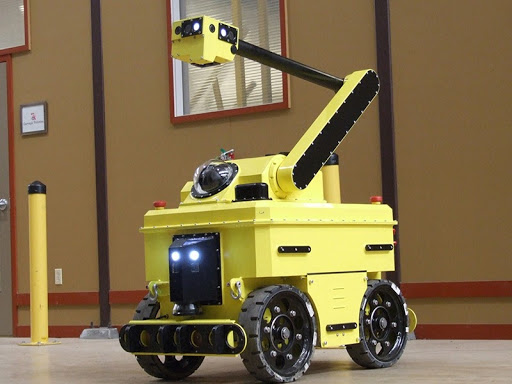
A common use of robots in visual inspections is that of magnetic wheels. This allows access to metal walls to verify welds, joints, and identify surface faults.
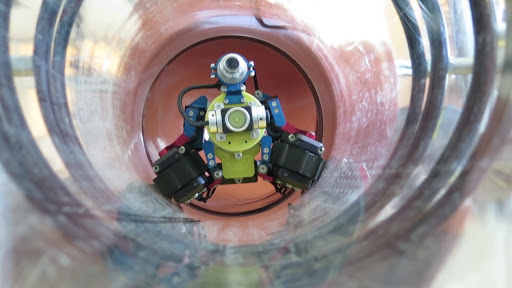
Benefits of using robots for visual inspections
There are two types of benefits robots offer in visual inspections for predictive maintenance:
- Improved inspector safety: avoid exposing the inspector to work in confined spaces, work at heights, work near areas of electrical risk or with harmful gases.
- Access to inspection points remotely: by means of robots, it is possible to visually access points where a person cannot, either due to space limitations or a harmful or high-risk environment.
Robot applications for visual inspections
Among the main applications of robots for visual inspections are:
- Tanks
- Pressure tanks.
- Boiler walls.
- Pipelines.
- Cooling towers.
- Ducts.
- Walls, facades.
- Structures under water.
Considerations for selecting a robot
As it is a non-standard technology in the industry, you may not have experience selecting robots, either for acquisition or for contracting services. Here are some things to consider when selecting a robot for visual inspections for predictive maintenance.
Create a list of all assets and inspection points for which you need the robot. For each case define the distance between the inspection point and the control place, working conditions (indoor/outdoor, submerged, temperature, pressure).
Check with your organization that the robot could not be used for some other purpose. Many times having a robot in the maintenance department requires sharing the robot for purposes for which it is probably not prepared, such as remote manipulation, 3D data collection, thickness inspections with ultrasound, or other visual inspections in processes.
Make an inspection plan for the robot. It is important to know the autonomy, power supply, possibility of jamming. Likewise, establish the periodicity of use (weekly, monthly, semester, or annually).
Define the type of images you want: three-axis, panoramic, narrow focus, video, 4K, thermal imaging. This will allow you to select the appropriate camera and software.
Data management and integration. This is the most overlooked feature when selecting a robot since the proposals always focus on the technical characteristics of the robot. You should never lose focus that you need to integrate the information and images captured with the robot to a repository of predictive maintenance reports unique to the company.
A few last tips for selecting a robot:
- Determine the degree of autonomy required for the robot.
- Take into account the surfaces on which the robot will move.
- Make a pilot plan. You will probably have to hire services at the start to see the feasibility of using the robot.
- Consider ongoing staff training.
- Technical support and stock of local parts.