How Much Money Can Predictive Maintenance Save An Industrial Company?
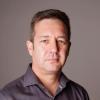
The amount of money that an industrial plant can save using predictive maintenance can vary depending on several factors, including the size and complexity of the plant, the type and number of machines and equipment being used, and the effectiveness of the predictive maintenance program.
Benefits of predictive maintenance
Predictive maintenance can potentially save manufacturing plants a significant amount of money through these benefits:
-
Reduced downtime and improved equipment uptime
-
Reduced maintenance costs
-
Increased productivity
-
Extended equipment life and reduced replacement costs
-
Improved operational efficiency and productivity
-
Increased safety of people and processes
-
Better resource planning
A study by PWC found that “the main drivers for our (Predictive Maintenance) success are factory uptime and safety. Downtime costs can amount to half a million euros (or dollars) per day in missed revenue, so we have reached a point where the benefits of reducing maintenance costs by a few percent are rather insignificant compared to those gained by improving uptime”.
According to the PWC study, Predictive Maintenance improves uptime by 51%
Additionally, the following objectives can be fulfilled: cost reduction (11%), risk reduction associated with safety, health, environment, and quality (SHEQ) (8%), extending the lifetime of assets (7%) and improving customer satisfaction (12%).
The biggest savings from predictive maintenance, however, come from reduced downtime.
The cost of a downtime
There are several factors to consider when calculating the cost of an industrial plant downtime. Some of the key factors to consider include:
- The duration of the downtime: The longer the downtime period, the greater the overall cost will be.
- The impact on production: If the equipment that is taken offline is critical to the production process, the cost of downtime will be higher due to lost productivity.
- The cost of repairs and maintenance: The cost of repairing the equipment and getting it back online will also need to be considered.
- The cost of lost sales and revenue: If the equipment failure leads to missed sales or lost revenue, this should be included in the overall cost calculation.
- The cost of lost customers and reputation: Downtime can also lead to lost customers and damage to a company's reputation, which can have long-term financial impacts.
According to The True Cost Of Downtime report, large plants on average lose 323 production hours per year. The average cost of lost revenue, financial penalties, idle staff time, and restarting lines is $532,000 per hour or $172 million per plant annually.
The average cost of downtime is $172 million per plant annually
It is logical to ask why not all industrial plants have a predictive maintenance program or why predictive maintenance programs do not translate into economic results.
Barriers to implementing predictive maintenance
There can be several barriers to implementing a predictive maintenance program, including the following:
- Limited availability of information and resources: There may be limited information and resources available on predictive maintenance, making it difficult for organizations to learn about it and implement it.
- Lack of awareness: Predictive maintenance benefits may not be well understood by some individuals mainly because it’s a relatively new concept and not all industries and organizations may have been exposed to it.
- Misconceptions about predictive maintenance: There may be some misconceptions about predictive maintenance, such as the belief that it is too complex or expensive to implement. These misconceptions can discourage organizations from considering predictive maintenance.
- Lack of expertise: Implementing a predictive maintenance program requires knowledge and expertise in data analytics and machinery diagnosis. If the necessary expertise is not available within the organization, it can be difficult to implement a predictive maintenance program.
- Cost: Implementing a predictive maintenance program can require significant investment in data collection and analysis tools, as well as training and personnel to operate the program. This can be a barrier for organizations with limited budgets for investments.
- Resistance to change: Changing from a traditional reactive maintenance approach to a predictive maintenance approach can be challenging, as it requires a shift in mindset and processes. This can lead to resistance from personnel who are accustomed to the traditional approach.
What happens to companies with a predictive maintenance program?
Most predictive maintenance programs have been implemented following Reliability Centered Maintenance (RCM) analysis techniques and not with the objective of reducing plant downtime.
During implementation, maintenance departments strive to apply the inspection techniques (vibration analysis, thermography, oil analysis, etc.) most appropriate for their industrial assets and to train personnel to execute these inspection techniques properly.
Once implemented, predictive maintenance management is limited to analyzing data from sensors, instruments or laboratory data and generating work orders when there are early signs of failure.
Predictive maintenance programs rarely quantify and record savings or reduced plant downtime. This means that results are not visualized.
In conclusion, the biggest savings from predictive maintenance is the reduction of plant shutdowns, which can be reduced by up to 50%. However, predictive maintenance programs are not implemented based on this objective, but on RCM analysis techniques and their management is focused on machine data analysis.
This leads to the need for predictive maintenance implementation and management tools focused on financial results. Power-MI is a process-focused predictive maintenance management tool for asset inspection management, failure recording and savings documentation.
What is Power-MI?
Power-MI is a cloud based solution that allows you to design & manage your condition-based maintenance plan integrating all techniques into one platform. Easy reporting, automatic work orders and CMMS integration.
Read more