The P-F Curve: A Cornerstone in Condition-Based Maintenance
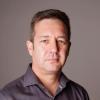
In today's industrial landscape, efficiency and reliability are critical. Unplanned downtimes and equipment failures lead to financial losses, production disruptions, and safety issues. Condition-Based Maintenance (CBM) has become a key strategy to ensure asset reliability and longevity, with the P-F Curve playing a central role. This conceptual tool represents the progression of asset degradation from the initial point of potential failure to complete functional failure.
This blog post is part of a series of academic articles on Condition-Based Maintenance. The P-F Curve concept is particularly important for maintenance managers, plant managers, reliability engineers, and industrial engineers who aim to keep assets performing at their best. In this post, we explore the origins of the P-F Curve, its practical application using an example of bearing failure, and its impact on maintenance strategies. We also highlight the economic benefits of predictive maintenance and how the P-F Curve supports cost optimization.
Origins of the P-F Curve Concept
Originally, maintenance strategies were reactive, addressing failures only after they occurred. This approach resulted in high costs and long downtimes. Preventive maintenance marked progress by implementing scheduled interventions, but it still lacked precision. The introduction of Reliability-Centered Maintenance (RCM), pioneered by experts like John Moubray, emphasized understanding failure modes and developing tailored maintenance strategies. Within this framework, the P-F Curve emerged as a key visual tool representing the condition deterioration process, enabling better prediction and preventing failures.
Bearing Failure: A Practical Example of the P-F Curve
To understand the P-F Curve, let's consider a bearing in an industrial machine.
- Point P (Potential Failure): This is when an anomaly becomes detectable through condition monitoring techniques but hasn't yet affected the asset's performance. For a bearing, this could be the beginning of micropitting, which may only be detected through advanced techniques like vibration analysis.
- Point F (Functional Failure): This occurs when the machine can no longer perform its primary function properly. Under the RCM concept, functional failure means the machine's performance is compromised to the point where it fails to meet its intended purpose. If the machine shuts down, it may also cause secondary damage. In the bearing example, this could mean damage to the bearing housing or even a broken shaft, escalating repair costs and downtime.
The P-F Interva
The P-F Interval is the time span between Points P and F, representing the window of opportunity for maintenance intervention. In the bearing example, early detection allows maintenance teams to repair or replace the bearing during scheduled downtimes, preventing unexpected shutdowns.
Maintenance Implications of the P-F Curve
- Optimizing Inspection Intervals: Understanding the P-F Interval helps optimize inspection schedules to maximize the chances of detecting issues early. A common practice is to schedule inspections at less than half of the P-F Interval to ensure multiple chances to identify potential faults.
- Economic Benefits: Addressing issues at Point P is much more cost-effective compared to dealing with failures at Point F. The cost savings (Savings = Cost_F - Cost_P) include personnel, parts, and unplanned downtime expenses, making predictive maintenance a financially sound approach.
Implementing Condition-Based Maintenance
The P-F Curve emphasizes the importance of proactive maintenance strategies:
- Data Collection: Use condition monitoring tools to collect data on asset health.
- Analysis and Reporting: Analyze the data to detect potential failures and issue actionable recommendations.
- Maintenance Execution: Address issues within the P-F Interval to prevent unexpected downtime.
Enhancing Collaboration Between Analysts and Maintenance Teams
A common challenge in predictive maintenance is the disconnect between analysts and maintenance teams. To improve collaboration, analysts should provide clear, actionable recommendations and companies should use integrated systems that streamline the process of turning analysis reports into work orders.
Technological Advancements Impacting the P-F Curve
- IoT and Smart Sensors: Real-time data from smart sensors allows for early anomaly detection, providing immediate insights into asset health.
- Machine Learning: Predictive algorithms improve the accuracy of P-F Interval estimates and help optimize maintenance schedules.
Conclusion
The P-F Curve is a fundamental tool for predictive maintenance, enabling organizations to prevent failures, reduce costs, and improve asset reliability. By focusing on early intervention, optimizing inspection intervals, and leveraging technology, maintenance teams can enhance efficiency and contribute to a stronger bottom line.
Key Takeaways
- The P-F Curve is a concept to understand how to anticipate failures and schedule timely maintenance.
- Acting within the P-F Interval minimizes costs and downtime that can be counted in terms of money.
- Technological integration, including IoT and machine learning, enhances the effectiveness of predictive maintenance.
To maximize the benefits of predictive maintenance, establish clear processes, enhance team communication, and focus on the economic impact of early interventions.
References
Moubray, J. (1997). Reliability-Centered Maintenance. Industrial Press Inc.
Smith, A. M., & Hinchcliffe, G. R. (2003). RCM: Gateway to World Class Maintenance. Elsevier.
Mobley, R. K. (2002). An Introduction to Predictive Maintenance. Butterworth-Heinemann.
Wienker, M., Henderson, K., & Volkerts, J. (2016). The Computerized Maintenance Management System: An Essential Tool for World Class Maintenance. Procedia Engineering, 138, 413-420.
Gupta, P., & Mishra, D. K. (2016). Predictive maintenance of industrial machines using IoT. International Journal of Computer Applications, 975, 8887.
Torres, C. E. "How to Calculate Condition-Based Maintenance Savings." Reliable Plant [online]. Available at: www.reliableplant.com/Read/31988/how-to-calculate-conditon-based-maintenance-savings, accessed October 29, 2024.
What is Power-MI?
Power-MI is a cloud based solution that allows you to design & manage your condition-based maintenance plan integrating all techniques into one platform. Easy reporting, automatic work orders and CMMS integration.
Read more