My First Predictive Maintenance Implementation
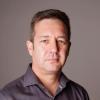
In May 2001, I was hired by the Steel Processing of El Salvador (Proaces) as a maintenance engineer with the main objective of implementing predictive maintenance at the plant. Proaces was known to me as they were clients of my previous company, so I had previously done some work such as vibration analysis, onsite balancing and electrical measurements in their plant. However, the Proaces managers explicitly wanted me to start from scratch.
The implementation of predictive maintenance was to buy an instrument and go out to measure the machinery. I learned that this is what more than 90% of maintenance departments do. But how did we decide to go down that road?
"Buy an analyzer and go out to measure now!"
That slogan that my boss, a steel industry veteran, gave me seems simplistic and hasty; but the order made sense.
On my first day of work, I realized that many of my colleagues did not know that someone was going to be hired for maintenance. That day, they introduced me to the maintenance department in an impromptu meeting. Although my position in the company was unclear, they explained that I would be in charge of implementing predictive maintenance and "other things" that they were delegating to me little by little. At that meeting, I understood that the reason for my being hired was major production downtime that had caused the company to lose "a lot of money". The origin of the setback had been a failure that is typically detected with vibration analysis.
My mission was to implement a vibration monitoring plan to anticipate these failures, with the emphasis on critical machines. The predictive maintenance plan was so far limited to the vibration collection routes and the respective analysis.
We bought SKF equipment from the only local supplier offering these products. The technical supply company that sold the equipment was represented in Proaces by a Mr. Polanco, a friendly technical salesperson, who invited me to lunch after doing some field tests with his demo equipment. Seeing that I declined, he convinced me by telling me that his company was covering the expense.
I noticed that the equipment delivery was delayed because the purchasing department was negotiating with Mr. Polanco. Mr. Polanco’s offer included onsite training in the use of the equipment and a basic course on vibration analysis. My surprise was that the training would be given by an SKF Colombia engineer and not Mr. Polanco himself, who seemed to know so much about vibrations and equipment. We finally negotiated a discount in exchange for abiding by the trainer’s schedule and their internal SKF agenda. Nevertheless, we did not wait for the trainer but decided to start our measurement routes before the visit of the trainer.
When the equipment arrived at Proaces, I showed off my experience in vibration analysis, and we decided to unpack it and get it going. Without waiting for the training, we installed the software with the CD that came with the instrument, and we stumbled into creating our first route. Back then, the only way to follow instructions was by reading the equipment manual, a practice which is obsolete in maintenance 20 years later. We received the training a few months later, and we learned a few new things.
The start of the predictive maintenance plan
I got help from Beto, a mechanical maintenance supervisor, a man with obvious experience, in good physical condition and good decision-making skills. The day the maintenance manager introduced him to me, he seemed to be saying goodbye to his favorite son. Together with Beto, we designed the measurement routes and began to collect the vibration data. We agreed that we would do the analysis together, and thus, I would teach him the details of spectral analysis and various tricks to pinpoint the causes of vibrations in rotating machines.
The many failures we detected drew the attention of the maintenance and production managers. Seeing their skepticism about our diagnosis, I explained how we could detect failures in vibration spectra and for that I was dubbed "NASA," in graceful allusion to the US space agency and its space technologies.
Doubts cast at predictive maintenance
After approximately two months of executing the predictive maintenance plan, one morning after my shower, I saw various missed calls on my cell phone between 5 and 7 am from the engineering manager's office and other coworkers. At that time, I was not used to sleeping with the cell phone, and was not in the habit of checking it all the time. When I returned the call, the department secretary recommended that I arrive at the plant as soon as possible; something serious had happened and they were looking for me.
When I arrived at the plant, I realized that they were looking for me not to solve the problem but to ask why I had not anticipated it. The bridge-crane over the rolling mill (the heart of the plant) had failed. The bridge had got stuck in a section, and finding the cause of the immobility of the bridge-crane under the operator's orders took several hours; solving the problem took almost a day. But the true cause of the trouble was unknown.
That day, given the situation, I realized that not only did they doubt "the predictive" element but I was guilty of not having warned them of the problem in advance. Instead, I had given them the impression that everything was under control and that we would not have any more standstills in the plant. I said this because we had done vibration tests on the cranes and never detected symptoms or signs of crane failure. So by now even I was doubtful of my knowledge and technology.
Later, we proved that the crane stop was caused by the misalignment of the parallelism of the rails and the wheels of the bridge. That was beyond the scope of a vibration analysis that did run-up and cost-down tests on the hoist. However, these clarifications went practically unnoticed since there were other problems to attend to at that time. My colleagues had already viewed the recommendations of NASA and Beto with eyes of skepticism, and asked sarcastically, "Are you sure?".
On our part, I cannot say that we diagnosed all the detectable faults with vibration analysis because we missed some. But what was evident was the number of failures that we had detected in time. Moreover, thanks to the corrective maintenance carried out, we avoided several breakdowns and costly machinery repairs.
The essence of predictive maintenance
The usual thing in El Salvador was to also work on Saturdays until noon. However, the effects of Friday night partying and the tendency to leave the plant exactly after 4 hours of work on Saturday motivated me to use those days to do predictive maintenance statistics so as not to go out to the plant for measurements. Therefore, Beto and I got together to go over the week's reports one by one and classify the faults that we had detected. It was evident that most of the failures were not due to the vibration analysis but to Beto's observations while collecting data. Thus, we began to consider whether it would not be better to start with visual inspection routes than by using vibration instruments.
Likewise, it was common for some puzzled production coworker to come up to us complaining that there had been a serious failure and I had not told him anything in advance. This would happen regardless of where the failure was – in an electrical panel, PLCs, or even in the emulsion oil. To that, my explanation was simple: "I do vibration analysis; I don't have a crystal ball". At the same time, the colleague’s concern remained valid: why was the predictive maintenance only limited to vibration analysis?
I quickly understood that the essence of predictive maintenance is not in buying instrumentation, taking a course and going out to measure. The essence is to analyze critical machines, the probability that they will fail, the consequences of their failure, and the possible failures they may have and, with that information, decide on the technologies with which they should be analyzed and the frequency of their inspection. I soon learned that, with the combination and cross referencing of information from several predictive techniques, we would usually end up with better diagnoses.
What is Power-MI?
Power-MI is a cloud based solution that allows you to design & manage your condition-based maintenance plan integrating all techniques into one platform. Easy reporting, automatic work orders and CMMS integration.
Read more