The History and Evolution of Condition-Based Maintenance
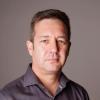
In the rapidly advancing industrial landscape, maintenance practices have significantly evolved to enhance operational efficiency, equipment reliability, and cost-effectiveness. One of the most pivotal strategies that have emerged is Condition-Based Maintenance (CBM). CBM leverages real-time data and advanced analytics to predict and prevent equipment failures, marking a shift from traditional maintenance approaches. This article explores the history and evolution of CBM, tracing its roots from the early days of Predictive Maintenance (PdM) and examining when and how the terminology transitioned, particularly in relation to updates in international standards.
Early Maintenance Approaches: Reactive and Preventive Maintenance
During the initial stages of industrialization, maintenance was predominantly reactive—equipment was repaired or replaced only after a failure occurred. This approach often led to unexpected downtime, increased safety risks, and high repair costs. As machinery became more complex and integral to production processes, the limitations of reactive maintenance became evident.
To mitigate these issues, industries adopted Preventive Maintenance (PM) in the mid-20th century. PM involves performing maintenance activities at predetermined intervals, regardless of the equipment's actual condition. While PM reduced the incidence of catastrophic failures, it was not cost-effective due to unnecessary maintenance actions and did not eliminate unexpected breakdowns caused by unforeseen factors.
The Emergence of Predictive Maintenance
The limitations of PM led to the development of Predictive Maintenance (PdM) in the 1960s and 1970s. PdM focuses on monitoring the condition of equipment to predict when maintenance should be performed, thus preventing failures and optimizing maintenance schedules (NASA Office of Safety and Mission Assurance, 2000). This strategy utilized condition-monitoring tools to detect signs of wear or degradation.
Key technologies enabling PdM included:
- Vibration Analysis: Detects mechanical issues like imbalance and misalignment.
- Thermography: Uses infrared imaging to identify temperature anomalies.
- Oil Analysis: Monitors lubricant quality and detects wear particles.
- Ultrasonic Testing: Identifies flaws or changes in material properties.
These technologies allowed for early detection of potential equipment failures, enabling maintenance personnel to intervene before a breakdown occurred.
The 1970s Energy Crisis and Technological Progress
The 1973 oil crisis prompted industries to seek ways to conserve energy and reduce operational costs. PdM gained prominence as it improved equipment efficiency and extended machinery lifespan. Technological advancements during this period, such as the advent of microprocessors and improved sensor technology, facilitated more precise and reliable condition monitoring.
By the 1980s, the integration of computer technology allowed for better data acquisition and analysis. This era saw the emergence of Computerized Maintenance Management Systems (CMMS), which helped in tracking equipment history, scheduling maintenance, and managing resources effectively.
Transitioning Terminology: From Predictive to Condition-Based Maintenance
When Did the Terminology Shift Occur?
The transition from the term Predictive Maintenance to Condition-Based Maintenance became more pronounced in the late 1990s and early 2000s. This shift was influenced by several factors, including advancements in technology, changes in maintenance strategies, and significant updates in international standards, particularly those set by the International Organization for Standardization (ISO).
Influence of International Standards
The key standard that formalized this transition is ISO 13306, published in 2001. This standard defines Condition-Based Maintenance as a form of preventive maintenance based on performance and/or parameter monitoring, thereby encompassing predictive maintenance as a subset of CBM. This definition emphasized the proactive nature of CBM, focusing on real-time monitoring and data analysis to inform maintenance decisions.
Other significant standards include:
- ISO 17359:2003: Provides general guidelines for condition monitoring and diagnostics of machines.
- ISO 13374 Series: Offers guidelines for data processing and communication in condition monitoring and diagnostics.
Reasons for the Shift
The shift in terminology from Predictive Maintenance to Condition-Based Maintenance reflects an evolving understanding of maintenance strategies:
- Technological Advancements: The rise of affordable, high-precision sensors and the Internet of Things (IoT) enabled continuous, real-time monitoring of equipment. These capabilities aligned more closely with the principles of CBM.
- Holistic Maintenance Approach: CBM represents a more comprehensive strategy, focusing on the actual condition of equipment rather than relying solely on predictive models based on historical data.
- Standardization and Best Practices: The adoption of CBM in international standards, such as ISO 13306, provided a unified framework that industries worldwide could follow, promoting consistency and efficiency in maintenance practices.
Industry Adoption
The terminology shift was further solidified as industries began to implement maintenance programs in line with the new ISO standards. The emphasis on condition monitoring and diagnostics encouraged organizations to adopt CBM as part of their asset management strategies, leveraging technological advancements to enhance operational efficiency.
Understanding Condition-Based Maintenance
Condition-Based Maintenance (CBM) is a proactive maintenance strategy that involves continuous or periodic monitoring of equipment health to perform maintenance only when necessary. By continuously assessing equipment conditions, CBM enables timely interventions, reducing downtime and preventing unexpected failures.
Core elements of CBM include:
- Data Acquisition: Collecting data through sensors measuring vibration, temperature, pressure, etc.
- Data Processing: Converting raw data into meaningful information.
- Condition Monitoring: Analyzing data to assess equipment health.
- Diagnostics: Identifying the root cause of detected anomalies.
- Prognostics: Predicting future equipment behavior and estimating the remaining useful life.
CBM aims to optimize maintenance resources by addressing actual equipment needs, thereby improving reliability and reducing unnecessary maintenance activities.
Technological Innovations Driving CBM
The effectiveness of CBM has been greatly enhanced by several technological advancements:
- Advanced Sensors and IoT Devices: These allow for continuous, real-time monitoring of equipment parameters. Sensors have become more affordable and capable, facilitating widespread adoption.
- Big Data Analytics and Machine Learning: These technologies enable the processing and analysis of vast amounts of data to detect patterns and anomalies that may indicate potential failures. Machine learning algorithms improve prognostic accuracy over time.
- Cloud Computing: Provides scalable storage and computational power necessary for handling large datasets generated by condition monitoring systems. Cloud platforms also facilitate remote monitoring and collaboration.
- Cyber-Physical Systems and Digital Twins: Integrate physical processes with computational models, allowing for simulations and predictive maintenance strategies. Digital twins replicate equipment in a virtual environment for detailed analysis.
Impact Across Various Industries
- Manufacturing: CBM has led to significant reductions in downtime and maintenance costs, enhancing productivity and product quality.
- Aviation: Aircraft employ CBM to ensure safety and reliability, with real-time monitoring systems for engines and critical components.
- Energy Sector: Power generation facilities use CBM to monitor turbines and generators, optimizing performance and preventing outages.
- Transportation: Railways and shipping industries utilize CBM to monitor the condition of vehicles and infrastructure, improving safety and operational efficiency.
Advantages of Condition-Based Maintenance
- Cost Efficiency: Reduces unnecessary maintenance and optimizes the use of resources.
- Increased Equipment Availability: Minimizes downtime through timely interventions.
- Extended Equipment Lifespan: Early detection of issues prevents severe damage.
- Improved Safety: Prevents accidents by identifying potential failures before they occur.
- Data-Driven Decision-Making: Enhances strategic planning and operational decisions based on real-time data.
Challenges in Implementing CBM
Despite its benefits, implementing CBM poses several challenges:
- High Initial Investment: Requires significant expenditure on sensors, software, and infrastructure.
- Complex Data Management: Involves handling large volumes of data and requires robust IT systems.
- Need for Skilled Personnel: Requires expertise in data analysis, condition monitoring techniques, and maintenance management.
- Integration with Existing Systems: May face compatibility issues with legacy equipment and systems.
- Cybersecurity Risks: Increased connectivity can expose systems to cyber threats, necessitating strong security measures.
The Role of International Standards
International standards have played a crucial role in promoting and standardizing CBM practices.
Impact of ISO Standards on Terminology
The publication of ISO 13306:2001 marked a significant moment in formalizing the term Condition-Based Maintenance. By providing standardized definitions and guidelines, ISO facilitated a global shift towards CBM, encouraging industries to adopt the terminology and methodologies outlined in these standards.
Other relevant standards include:
- ISO 17359:2003: Provides general guidelines for condition monitoring and diagnostics of machines.
- ISO 13374 Series: Offers guidelines for data processing and communication in condition monitoring and diagnostics.
- ISO 55000 Series: Addresses asset management, integrating CBM into broader asset management strategies.
Alignment with Technological Advancements
The shift in terminology aligns with advancements in technology and data analytics, allowing for more effective and efficient maintenance practices across various industries. The standards emphasize the proactive nature of CBM, which aims to address potential failures before they occur by continuously assessing equipment conditions.
The Future of Condition-Based Maintenance
CBM is expected to evolve further with ongoing technological advancements:
- Artificial Intelligence (AI) and Advanced Analytics: Will improve fault detection and prognostics, enabling more accurate and timely maintenance decisions.
- Edge Computing: Processing data closer to the source will reduce latency and improve real-time decision-making.
- Augmented Reality (AR) and Virtual Reality (VR): Will assist maintenance personnel by overlaying equipment data and providing interactive instructions.
- Blockchain Technology: Can enhance data security and integrity in maintenance records and equipment history.
Conclusion
The evolution from Predictive Maintenance to Condition-Based Maintenance marks a significant shift in maintenance philosophy. The change in terminology, particularly following the updates in ISO standards like ISO 13306, reflects a deeper transformation driven by technological advancements and the need for more efficient, data-driven maintenance strategies.
CBM focuses on real-time monitoring and proactive decision-making based on the actual condition of equipment, allowing industries to optimize maintenance activities, reduce costs, and enhance equipment reliability. As industries continue to adopt digital technologies, CBM is poised to become even more integral to maintenance management, paving the way for smarter, more autonomous maintenance systems.
Key Takeaways
- Terminology Shift Influenced by ISO Standards: The transition from Predictive Maintenance to Condition-Based Maintenance became prominent in the early 2000s, particularly after the publication of ISO 13306:2001.
- Emphasis on Actual Equipment Condition: CBM makes maintenance decisions based on the current state of equipment rather than predictions or fixed schedules.
- Technological Drivers: Innovations in sensors, IoT, big data analytics, and AI have enhanced CBM capabilities.
- Global Standards: ISO standards have standardized CBM practices, promoting consistency and quality across industries.
- Future Outlook: Emerging technologies like AI, digital twins, and edge computing will further advance CBM, making maintenance more predictive and efficient.
By incorporating detailed research and literature, this article provides a comprehensive overview of the history and evolution of Condition-Based Maintenance. It highlights the shift from Predictive Maintenance, emphasizing the influence of ISO standard updates—particularly ISO 13306:2001—on the terminology and methodologies adopted in modern maintenance practices.
References
ISO. (2001). ISO 13306:2001 Maintenance terminology. International Organization for Standardization.
ISO. (2003a). ISO 17359:2003 Condition monitoring and diagnostics of machines—General guidelines. International Organization for Standardization.
ISO. (2003b). ISO 13374-1:2003 Condition monitoring and diagnostics of machines—Data processing, communication and presentation—Part 1: General guidelines. International Organization for Standardization.
ISO. (2014). ISO 55000:2014 Asset management—Overview, principles and terminology. International Organization for Standardization.
Mobley, R. K. (2002). An introduction to predictive maintenance. Butterworth-Heinemann.
Moubray, J. (1997). Reliability-centered maintenance. Industrial Press Inc.
NASA Office of Safety and Mission Assurance. (2000). Reliability-Centered Maintenance Guide for Facilities and Collateral Equipment. NASA.
Ahmad, R., & Kamaruddin, S. (2012). An overview of time-based and condition-based maintenance in industrial application. Computers & Industrial Engineering, 63(1), 135–149.
Fiorentino, M., Uva, A. E., Gattullo, M., Debernardis, S., & Monno, G. (2014). Augmented reality on large screen for interactive maintenance instructions. Computers in Industry, 65(2), 270–278.
What is Power-MI?
Power-MI is a cloud based solution that allows you to design & manage your condition-based maintenance plan integrating all techniques into one platform. Easy reporting, automatic work orders and CMMS integration.
Read more