Digitalization and Integration of Predictive Maintenance with CMMS
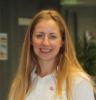
Article published in AEM Review online Mantenimiento: ingeniería industrial y de edificios (in Spanish)
This article explores the digitalization and integration process of predictive maintenance with the Computerized Maintenance Management System (CMMS) at the Cosentino Group, a leading company in the production and distribution of innovative surfaces for architecture and design. Digitalization has enhanced plant reliability and optimized information management and processing time, translating into increased operational efficiency.
The article details how the creation of an asset database, standardization and digitalization of reports, the use of inspection technique catalogs and failure catalogs, as well as analyst schedules, have facilitated the management of a large number of assets and the generation of thousands of annual reports, while also improving accuracy and speed in identifying and resolving failures.
The implementation of Power-MI software, specifically designed for predictive maintenance, has been crucial in this process. An initial pilot program validated its effectiveness before full adoption. The results include better data structuring and processing, as well as stronger preparation for future Industry 4.0 initiatives and data analysis.
Cosentino And Its Focus On Operational Excellence
Cosentino Group is a global Spanish family-owned company dedicated to the production and distribution of innovative and sustainable high-value surfaces for the world of architecture and design. The company stands out for its commitment to operational excellence and sustainability, working closely with clients and partners to provide solutions that inspire people's lives, while acting under responsible and transparent ESG criteria.
In its ongoing quest for operational excellence, Cosentino has implemented a predictive maintenance department within the Maintenance Operational Excellence Center. This approach focuses on digitalization as a key strategy to centralize and structure information, thereby maximizing the benefits of Industry 4.0 technologies.
Description Of Equipment And Assets
The predictive maintenance team at Cosentino consists of three certified specialists holding CAT-II certification in vibration analysis. This highly skilled team is responsible for managing 2,579 assets, applying a variety of advanced predictive techniques to ensure optimal functioning of each one.
Digitalization has been key to efficiently managing such an extensive inventory. The technicians utilize a wide range of tools and methods, including vibration analysis, ultrasound, thermography, oil analysis, and laser alignment. These techniques enable early identification of potential issues, which is crucial for maintaining operational continuity and minimizing downtime.
Each asset is meticulously classified within a taxonomy that reflects the SAP structure, covering factories, sections, and subsections. This detailed classification includes essential information such as asset name, type (motor, pump, fan, etc.), and its criticality. This information not only facilitates daily management but also significantly improves data analysis and performance comparisons among similar assets.
Additionally, digitalization allows documentation of the predictive techniques applied to each asset. Technicians select the potential failures detectable with each specific technique, creating a comprehensive profile for each piece of equipment. This detailed documentation is accessible at a glance, providing complete information on the equipment's condition, the techniques applied, and the report history, along with a health matrix that details all detectable failures and the technology used for each.
Implementation Process
To carry out the implementation, we identified that SAP was not intuitive enough for our needs, so we decided to look for providers in the market who could offer a more suitable solution.
Our priority was to centralize all information in SAP, as it is our Computerized Maintenance Management System (CMMS). After evaluating several options, we found that Power-MI perfectly met our needs. This software is specifically designed for predictive maintenance, avoiding the need to develop an application from scratch and significantly reducing costs.
We began the project with a pilot plan, applying it to a small number of machines to test the tool in a controlled environment. This pilot testing phase is crucial, as it allows us to verify the suppliers' claims about their systems' capabilities and check their effectiveness in practice.
We then significantly increased the project's scope during the rollout phase and later, during the expansion stage, covered all assets within the predictive maintenance plan. The final step was to integrate Power-MI with SAP PM.
Asset Inventory
The first step in the digitalization process is creating a robust database for the predictive maintenance team. This database must be structured following an identical taxonomy to that used in SAP, starting by defining the various factories and their corresponding sections, subsections, and assets.
For each asset, the following must be defined:
- Asset type: Motor, pump, fan, etc.
- Criticality: Classification of the asset's importance.
- Predictive techniques: Vibration analysis, acoustic ultrasound, thermography, etc.
- Detectable failures: Linked to each predictive technique.
Once this information has been gathered and entered, a comprehensive and consolidated view of the asset is obtained, as well as a properly structured information repository. This is key to any digitalization project.
Digitalization Of Reports
The digitalization of reports is crucial for optimizing both time and efficient information management. This process has allowed the predictive maintenance team to generate a large volume of reports in less time and standardize a format that includes all relevant information, regardless of the technology used.
- 10,485 reports generated in 2023
- Monthly average exceeding 700 reports
When creating a report, analysts select the detected failure from the catalog, describe the diagnosis, provide technical evidence, the asset condition, and most importantly for maintenance, the recommendation.
This recommendation serves as the maintenance notification that is transmitted to SAP, maintaining traceability between the report and the work order. This is crucial to ensure that each diagnosis is linked to the corresponding repair, enabling integrated and efficient management of maintenance tasks.
In summary, the well-structured report is the means to collect failure records in a structured way, initiating the predictive maintenance cycle from diagnosis to its correction and savings calculation.
Information Management
One of the main challenges in information management is ensuring that the database is fed with reliable and accurate records for subsequent analysis. The key focus of our digitalization system lies in automating this process. With each generated report, the database is automatically updated. This means that by performing the same work as before, we can now obtain indicators and statistics automatically.
This automation not only optimizes workflow but also ensures the integrity and availability of critical information for decision-making in predictive maintenance.
Condition Indicators And Trends
Automatically, we have indicators of the current status of the equipment for each factory and section, as well as the trend over the last 12 months to monitor their evolution.
Unified Historical Record
For each asset, we have a timeline with information from all reports by predictive technique, as well as work orders created by predictive maintenance and those created by the plant. Thus, we have a complete and unified historical record that allows us to quickly analyze relationships between diagnoses from different technologies or review the latest diagnoses and effective repairs for the next report.
Failure Statistics
Since we have a failure record proactively fed by analysts through the reports, we can analyze which are the most frequent failures by factory or section or which type of asset has the highest failure rate. This type of analysis helps organize information for conducting root cause analysis, quickly identifying which assets require further analysis and what failures need investigation to eliminate the problem or reduce its impact.
We can also derive trends in failures to observe their evolution over time, useful for monitoring the effectiveness of actions resulting from root cause analysis or identifying possible failure patterns related to specific climatic seasons.
Benefits Of Predictive Maintenance Digitalization
- Time Optimization:
Reduced report preparation time.
Greater focus on data analysis and diagnosis.
- Information Management:
- Automatic database updating.
- Generation of indicators and statistics.
- Failure mode and trend analysis.
- Transparency:
- Information for all stakeholders with appropriate detail and format.
- Knowledge Base:
- Retention of business knowledge, reducing dependency on specific personnel or external service providers.
- Record of recommendations and actions taken for specific repairs.
- Predictive Maintenance Savings Calculation:
- Accurate ROI documentation, allowing calculation and justification of savings generated by predictive maintenance.
Next Steps
Looking forward, Cosentino is preparing to take the next step in its journey towards operational excellence. Future initiatives will focus on integrating Industry 4.0 technologies and Data Analytics. Collaborating with the Data Analytics team will enable us to make the most of the collected data, facilitating more advanced and predictive analysis. With a solid foundation already in place, the implementation of emerging Industry 4.0 technologies will further enhance the efficiency and reliability of predictive maintenance, taking the company to a higher level of innovation and operational excellence.
REFERENCES
PhD Luis Amendola, PhD Tibaire Depool. PMM Institute for Learning (2019). Tips for Digital Transformation in Asset Management.
Wienker, Michael & Henderson, Ken & Volkerts, Jacques. (2016). The Computerized Maintenance Management System: An Essential Tool for World Class Maintenance. Procedia Engineering. 138. 413-420. 10.1016/j.proeng.2016.02.100.
What is Power-MI?
Power-MI is a cloud based solution that allows you to design & manage your condition-based maintenance plan integrating all techniques into one platform. Easy reporting, automatic work orders and CMMS integration.
Read more