Most of the predictive maintenance by vibration analysis performed today, falls into one of the following groups:
- Periodic measurement of overall values and spectra.
- Online vibration monitoring.
Periodic measurement of overall values and spectra
Periodic vibration readings (also called in route) are made with portable equipment, these equipment according to their analysis capabilities can be grouped as:
- Overall value vibrometers: analog or digital.
- Frequency analyzers: Analog band-adjustment and FFT digital real-time.
Vibrometers are instruments that receive the electrical signal from a transducer and process it, applying filtration and integration, to obtain the overall vibration level value in velocity. Most of them are designed to take measurements according to certain standards of vibration severity. For example, according to ISO 2372, the vibration value in RMS velocity must be measured in a frequency range between 10 and 1000 Hz.
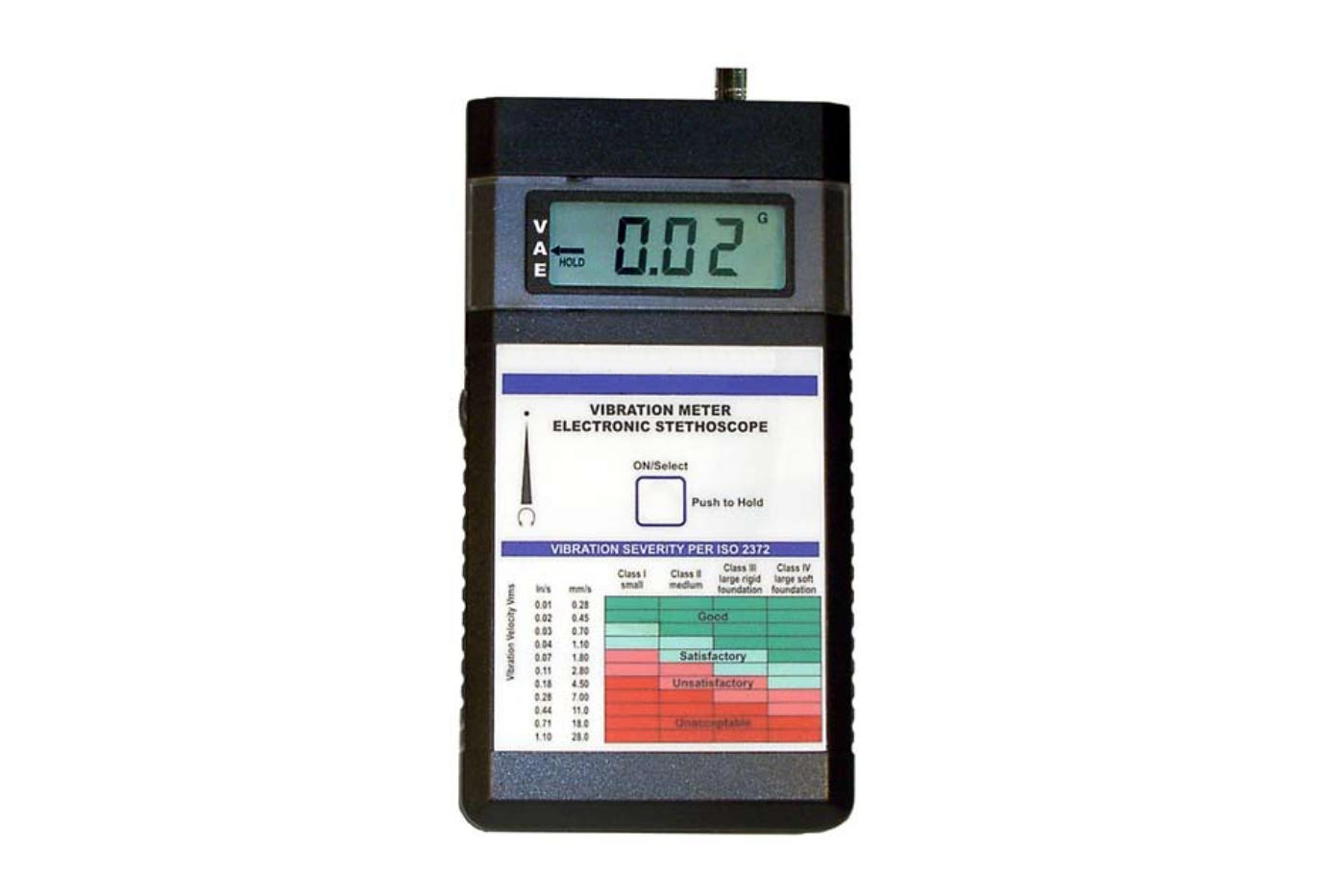
The main advantages of these instruments are their ease of use, light weight and an affordable cost. Their limitations are important, given that they only allow measuring amplitudes, since they do not provide any information relative to frequency. Another limitation is related to the extent of their working frequency range, limited in the low end preventing the measurement of sub-harmonic frequencies (related to problems of belt wear, oil whirl, friction, etc.) and limited in the high end (for defect frequencies in gears, bearings, cavitation, lubrication, etc.).
But the most important limitation of vibrometers is their impossibility of determining the frequency at which vibration occurs and hence its mechanical origin. At present, the development of vibration measurement instrumentation has advanced so much that there are many compact devices available in the market that, for a very affordable cost, are capable of performing the FFT analysis and obtaining the frequency spectrum, allowing to distinguish amongst specific machine issues.
Frequency analyzers are in essence small laptops. Its main virtue is the great ability to diagnose problems associated with characteristic frequencies related to mechanical problems in rotating elements. Nowadays these analyzers are digital equipment with integrated microprocessors for the computation of the FFT. They are able to obtain the spectrum in real time and have a multitude of functions to aid the analysis.
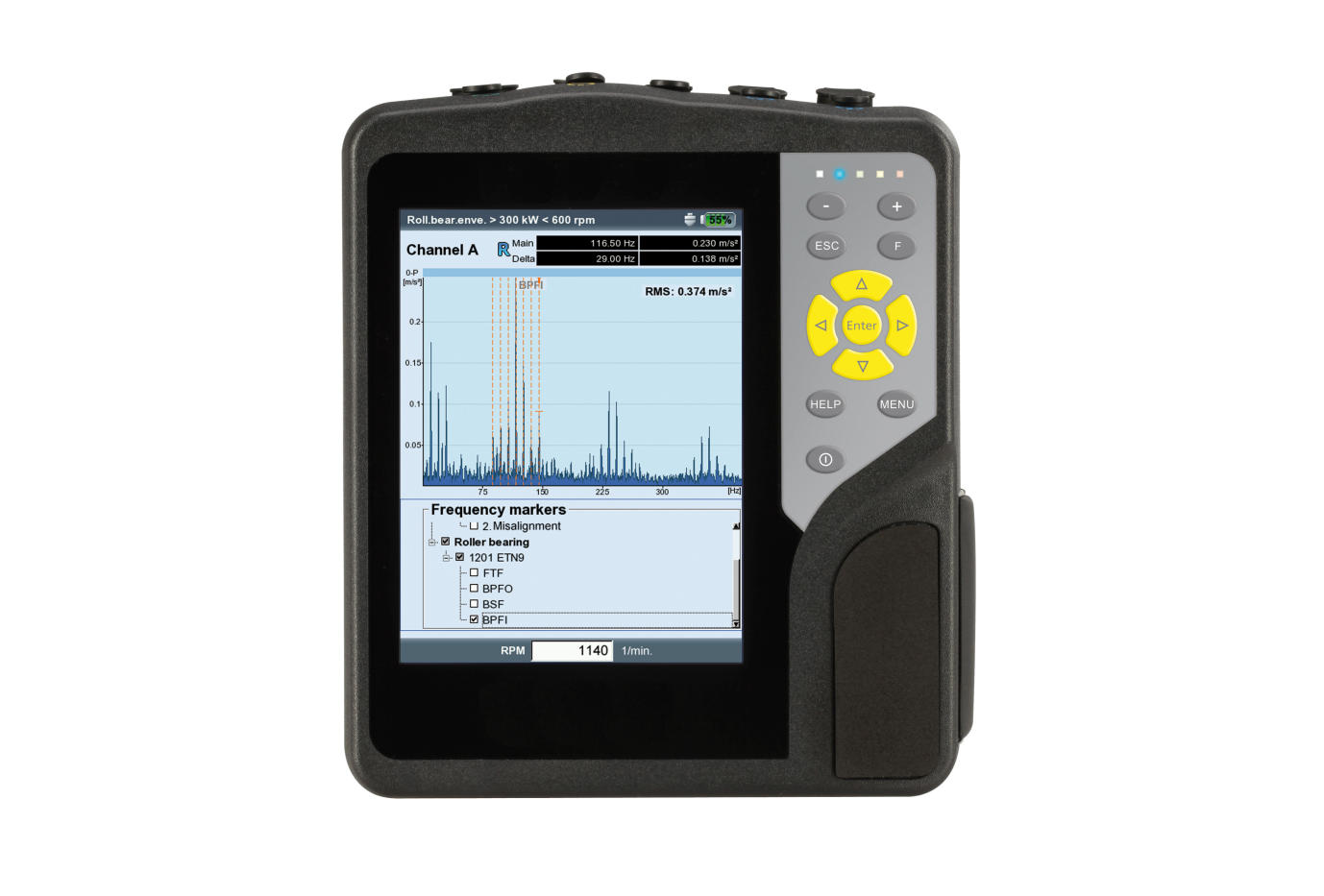
These computers are usually very robust, but the price of their robustness (apart from the purely economic) is that their performance is inferior to what one would expect. Typically these collectors are based on processors with low processing speeds, and with little memory available for measurement storage. Among the brands that dominate the market stand out Pruftechnik, CSI, Predict, Bently Nevada, Entek IRD, Bruel & Kjaer, Diagnostic Instruments, Framatome, Schenck.
In route readings are usually made with a sensor (usually an accelerometer) that is placed at the different measurement points located along the machine. The identification of these points in the machine can be done simply with paint, although it is more advisable to use a fixed base to ensure the repeatability of the readings. Likewise, the fastening method with which the accelerometer is attached to the machine is decisive in the quality of the vibration measurement obtained. The manual mounting, widely used until a few years ago, has given way to other higher quality mounting methods, such as the use of magnets or the rigid connection to quick disconnect receptacles in the machine itself. The identification of measurement points has also been improved by the introduction of aid tools, such as the use of bar codes.
Whatever the system used for the measurement, all data is stored in the data collector memory. This memory is usually, as already mentioned, quite limited, and sometimes volatile (lost when the batteries run out). Therefore, in order to evaluate vibration trends (fundamental element in predictive maintenance), these measurements must be downloaded to a desktop computer equipped with a specific software package. This download is normally done through the computer's USB port. The time used in the measurement of vibrations, as well as the time used in the processing of these data by the computer, tends to be minimized, since it is a time that does not imply any added value. It is necessary to take into account that the key value provided by the predictive maintenance program, comes from the vibration analysis and not from the vibration measurement, and therefore is in the analysis where most of the time possible should be invested. As a consequence, several methods have been developed to reduce the vibration reading time (triaxial sensors, special sensor quick connections, etc.), as well as to make a preliminary vibration analysis (automatic diagnostic systems) to guide the human analyst to the most relevant issues. Those measuring points that are difficult or dangerous to access, are usually equipped with permanently installed sensors. These sensors are wired to a junction box, to which the collector is connected during route measurement.
Online vibration monitoring
Vibration data acquisition in industrial machinery evolves towards automated systems (continuous or on-line systems) which in many cases offer greater benefits than the data acquisition with portable data collectors:
- Drastic reduction of data collection intervals. Since these are taken continuously. Allows to detect immediately any changes in the machine vibration.
- Lower operating cost. As the automatic data acquisition eliminates the labor cost associated to collecting the machine vibration data.
- Higher quality data collection. The data measurement accuracy is higher, since the data is always measured at exactly the same location and with the same sensor, and in addition we can condition the data collection to certain machine operating conditions (speed and load).
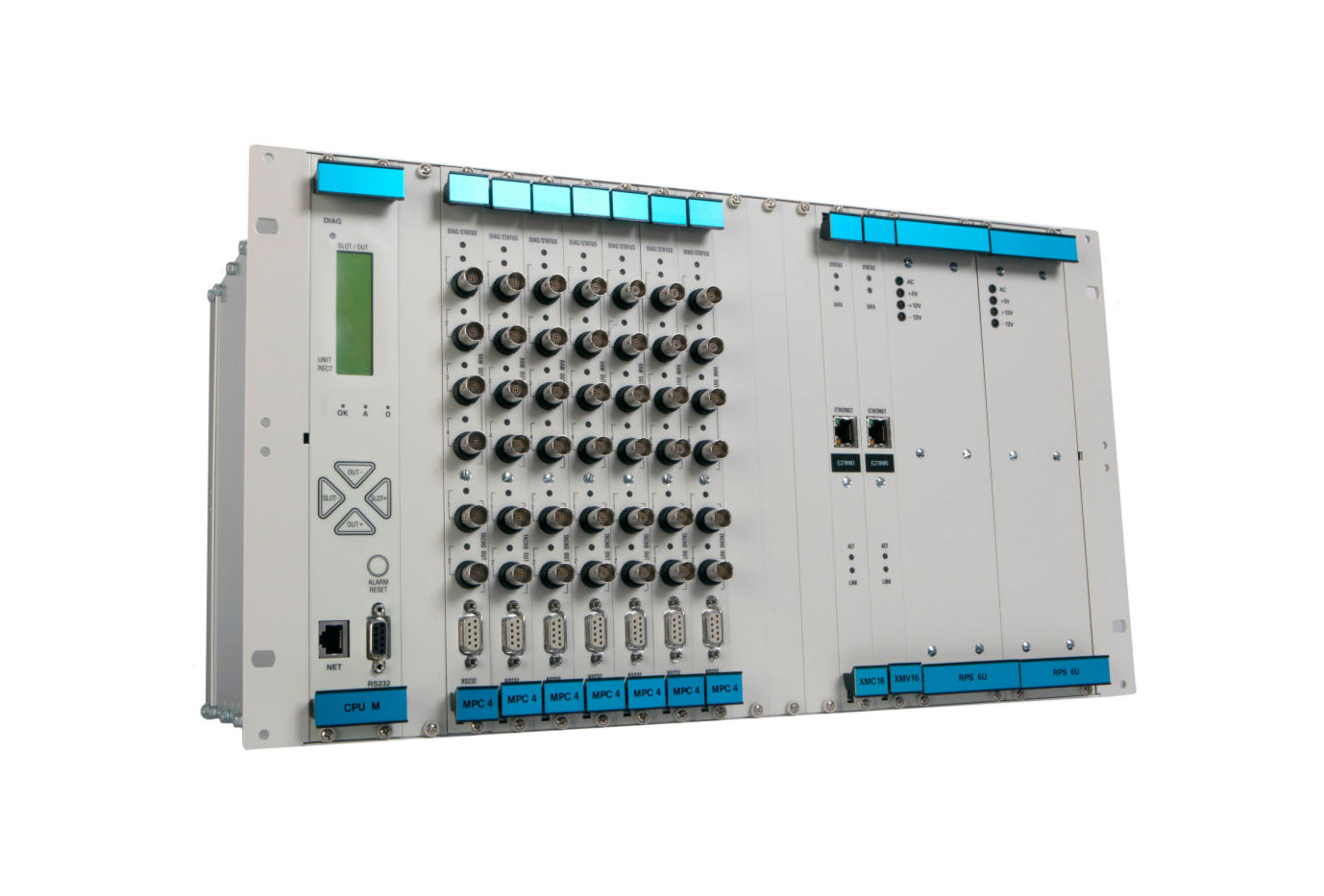
Online monitoring systems usually have the problem of the high cost of installation, compared to a portable system. This cost includes the sensors, the wiring in the plant, as well as the expenses of the measurement equipment itself. Particular attention must be paid to the wiring of the accelerometers, as it is important that the vibration signal degrade as little as possible on the way from the machine to the measuring equipment. To do this, avoid sources of electromagnetic interference (mainly high voltage cables), as well as excessively long cables.