Una parte importante de un programa de mantenimiento predictivo fiable es tener la capacidad de verificar una avería con más de una tecnología. Esto no sólo asegura la validez del diagnóstico, sino que también ayuda a hacer recomendaciones de reparación más concretas y precisas.
Son muchas y muy variadas las tecnologías que se pueden aplicar al campo del mantenimiento predictivo, entre las cuales podemos enumerar las más comunes:
-
Análisis de vibraciones
-
Termografía infrarroja
-
Inspección visual
-
Análisis de aceite
-
Ultrasonidos
-
Alineación láser
-
Análisis de gases disueltos
-
Análisis de corrientes de motores
-
Ensayo de aislamiento
Cada una de ellas tiene un campo de aplicación más o menos concreto, existiendo complementariedad, prácticamente entre todas. A continuación comentaremos brevemente algunas de ellas.
Análisis de vibraciones
De las distintas tecnologías aplicables al mantenimiento predictivo, el análisis de vibraciones es la más popular. La razón la encontramos en la posibilidad de determinar una gran cantidad de defectos, en una amplia gama de máquinas con una inversión económica inicial razonable. La vibración es uno de los indicativos más claros del estado de una máquina. Bajos niveles de vibración indican que el equipo se encuentra en buen estado, y cuando estos niveles se elevan está claro que algo comienza a ir mal.
Los equipos utilizados para la adquisición de datos de vibraciones en maquinaria abarcan desde los colectores portátiles o de campo hasta los equipos de monitorización en continuo u “on line”.
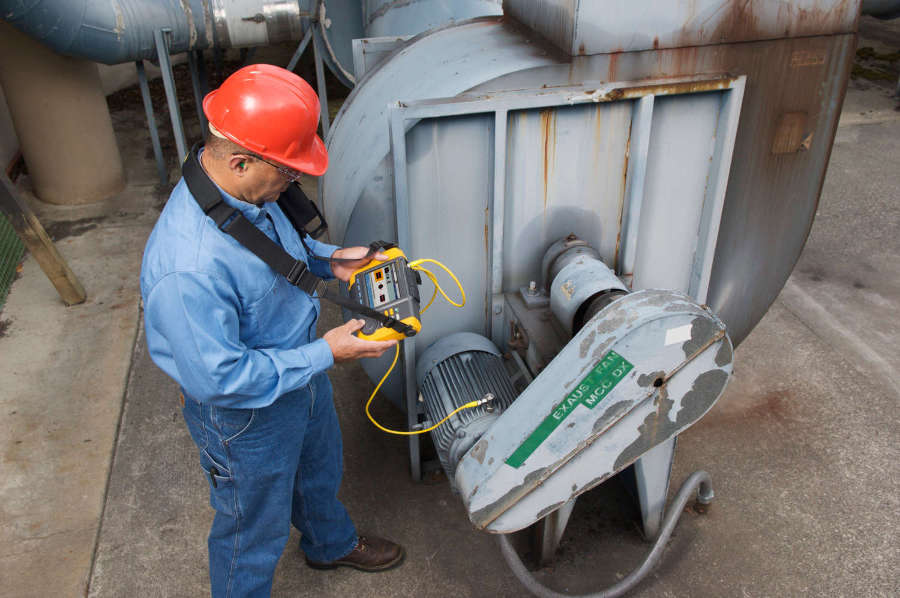
Producción y mantenimiento son las dos áreas de actividad más vinculadas al rendimiento de la empresa. El control de los parámetros de proceso (presión, temperatura, caudal, etc.) de los equipos ha sido objeto de automatización desde hace más de una década en base a sistemas de control distribuido y redes de autómatas programables con interfaces Scada. Por otro lado, el control de los parámetros de mantenimiento (vibración, temperatura, etc.) de los mismos equipos tiene todavía un largo camino por recorrer antes de lograr una implantación generalizada y una integración dentro del proceso de planta.
El análisis espectral de vibraciones consiste simplemente en realizar una transformación de una señal en el tiempo al dominio de la frecuencia, donde podemos identificar la vibración característica de cada uno de los componentes o defectos que puede presentar nuestro equipo.
No es este el momento de entrar en profundidades sobre cada una de las tecnologías que vamos a presentar, cada una de ellas es motivo en si de una formación específica. Basta por el momento comentar algunos de los problemas que se pueden detectar fácilmente con un análisis de vibraciones: desequilibrio, desalineación, holguras, aflojamientos, problemas de lubricación en cojinetes, daños en rodamientos, en engranajes, en motores eléctricos, problemas hidráulicos, etc.
Además un gráfico de tendencia del nivel de vibración en valor global o bien en un rango frecuencial dado es una excelente herramienta para la supervisión de nuestros equipos. Por último queremos volver a insistir en la importancia de la definición de los niveles de alerta y de alarma en los mismos para optimizar los análisis.
Termografía infrarroja
La termografía infrarroja se podría definir brevemente como una técnica que permite, a través de la radiación infrarroja que emiten los objetos, la medida superficial de su temperatura. El instrumento que se usa en termografía para medir, es la cámara termográfica.
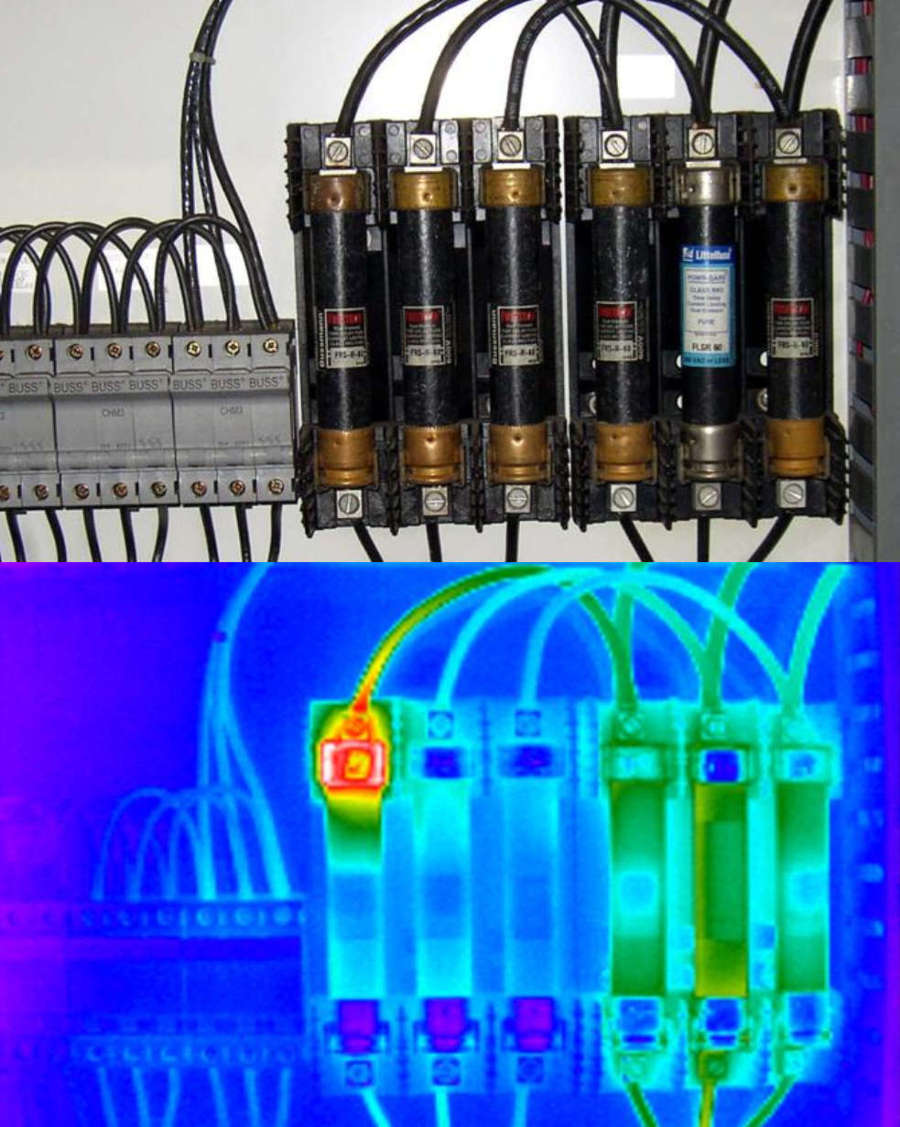
La principal ventaja de la medida de temperatura mediante termografía, es que es una técnica de medida sin contacto, por lo que no afecta en modo alguno al funcionamiento de los activos inspeccionados. Esta cualidad la hace especialmente interesante en el control y mantenimiento de elementos bajo tensión. Entre las principales aplicaciones de la termografía podríamos citar:
-
Detección de puntos calientes en maquinaria.
-
Medidas de espesores y detección de discontinuidades en productos aislantes térmicos y refractarios.
-
Inspección de tubos y tuberías.
-
Inspección en soldaduras.
-
Posicionamiento de componentes y fallos en circuitos eléctricos.
-
Aplicaciones de prevención y detección de incendios.
-
Medición en tanques de almacenamiento.
-
Control de calidad en procesos de producción.
De todas las posibles aplicaciones, las instalaciones eléctricas son excelentes candidatas naturales a la aplicación de la termografía infrarroja. Podremos detectar puntos calientes en los termogramas realizados a las mismas. Las causas de estos puntos calientes pueden ser varias:
-
Reflexiones
-
Radiación aportada por el sol
-
Carga
-
Variaciones de emisividad
-
Calor inducido por corrientes de Eddy
-
Aumento de resistencia, ocasionado por:
-
Conexión floja
-
Conexión con suciedad
-
Conexión con corrosión
-
Conexión con ajuste deteriorado
-
Componente incorrecto
-
Instalación incorrecta
-
Será labor del analista de termografía saber discernir, filtrar y evaluar los puntos calientes encontrados en los termogramas, buscando la causa y el origen de los mismos.
Inspección visual
Una de las formas más simples, pero a menudo olvidadas, de obtener información valiosa para el mantenimiento predictivo es la inspección visual de la maquinaria, que se entiende de manera más general como a hacer uso de nuestros propios sentidos. Sus ojos, oídos y nariz pueden ser valiosas herramientas de monitorización de la condición y a diferencia de otros instrumentos de medición, requieren poco entrenamiento para ser empleados de manera efectiva. Aunque aportan una valoración de carácter subjetivo, es posible obtener una idea bastante acertada de donde el problema es más severo. Sin embargo resulta importante remarcar que, en general, no es posible determinar de esta manera la causa raíz de los problemas.
Un procedimiento de inspección visual eficaz incluye el examen de cada uno de los siguientes aspectos en la máquina y su área circundante:
-
Limpieza general
-
Aceite / fluidos en las inmediaciones de la máquina
-
Aceite / fluidos en la carcasa de la máquina o soportes de rodamientos
-
Aceites / fluidos en la protección de acoplamiento
-
Marcas inusuales
-
Fugas visibles (lubricantes, agua de refrigeración, etc.)
-
Condiciones de iluminación
-
Indicadores locales de niveles, temperaturas, caudales y amperaje adecuados
-
Rozamiento y partículas de desgaste
-
Corrosión
-
Señales de sobrecalentamiento
-
Funcionamiento adecuado de sellos laberínticos
-
Condensación / agua en cojinetes
-
Variaciones de temperaturas, presiones y caudales
-
Piezas o componentes sueltos
-
Estado de la protección o de la cubierta de la máquina
Otra forma simple de monitorización de la condición es la inspección auditiva de la máquina. Si bien esto también aporta una valoración subjetiva, a menudo se puede obtener una buena idea aproximada de el área donde se origina el sonido. El uso de estetoscopios, sondas y otros dispositivos de escucha puede permitir a un profesional experimentado detectar problemas tales como roces, defectos en cojinetes, cavitación, etc.
Cuando esté escuchando una máquina, trate de determinar si el sonido es complejo o simple, de alta frecuencia o baja frecuencia, y de donde el sonido parece estar llegando.
Los procedimientos de inspección auditiva efectivos incluyen el examen de los siguientes aspectos en la máquina y su área circundante:
-
Sonidos fuera de lo común
-
Zumbidos
-
Chirridos
-
Rozamiento
-
Cavitación
-
Sonidos de arco eléctrico / estallidos
-
Sonidos repetitivos / Pulsaciones
-
Ruido por fugas
-
Comparación de ruido entre rodamientos
-
Golpe de ariete
-
Válvulas de aviso / válvulas de alivio de presión
-
Flujo a través del sistema / componentes
Otro método de inspección o sentido que puede no haber sido considerado es el olfato. El sentido del olfato humano es potente y puede utilizarse para identificar varias condiciones adversas de la máquina y problemas de lubricante. Entre los problemas comunes de lubricantes detectables por el olfato están ciertos tipos de contaminación, tales como disolventes, combustible, refrigerantes y otros productos químicos de proceso. Además, el aceite que se ha oxidado significativamente tiene un olor distinto que una vez conocido, es fácilmente identificable. También son detectables mediante el olfato otros tipos de problemas de la máquina. Las correas flojas o los componentes sobrecalentados a menudo presentan un olor alarmante que exige una investigación.
Análisis de aceite
El análisis de aceites consiste en la realización de tests fisico-químicos en el aceite con el fin de determinar si el lubricante se encuentra en condiciones de ser empleado, o si debe ser cambiado.
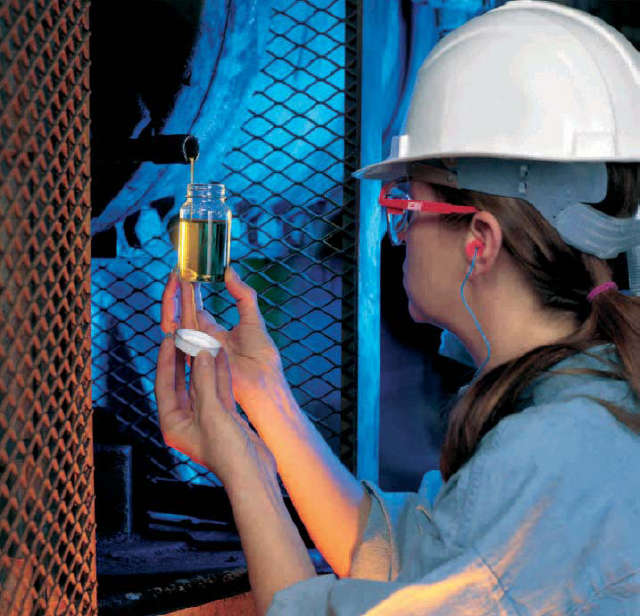
La ferrografía, o análisis de partículas de desgaste, sin embargo, utiliza el lubricante como un medio para determinar el estado de la máquina lubricada.
El análisis de aceites en instalaciones industriales tiene dos objetivos claros: conocer el estado del aceite y conocer el estado de la máquina. Tradicionalmente éste último se obviaba, centrándonos siempre en determinar únicamente el estado del lubricante, para lo cual se realizan una serie de ensayos rutinarios de viscosidad, acidez, basicidad, análisis de aditivos, inspecciones visuales, etc. No es este el principal objetivo de la analítica del aceite como técnica de mantenimiento predictivo.
Las espectrometrías, ferrografías y contenidos de partículas aportan valiosa información del estado de los componentes de las máquinas que bañamos con nuestros lubricantes. Podemos detectar defectos con una antelación mucho mayor que con otras técnicas como podría ser el análisis de vibraciones.
En casos de maquinaria critica debe emplearse como técnica complementaria para verificar un diagnóstico realizado, por ejemplo, con un análisis de vibraciones. Por ejemplo, defectos en rodamientos, cojinetes o transmisiones pueden corroborarse al encontrar partículas de los mismos en un ferrograma.
Análisis de corrientes de motores
El análisis de motores eléctricos puede realizarse mediante termografías o análisis de vibraciones, pero otra de las técnicas que pueden utilizarse para detectar problemas eléctricos o mecánicos en motores de corriente alterna es el análisis espectral de corrientes del motor (también conocido como MCA por sus siglas en inglés).
MCA es simplemente el proceso por el cual las lecturas de las intensidades de corriente en las fases de alimentación del motor son registradas y analizadas en el dominio de la frecuencia. Se emplea desde mitad de la década de los 80 y se ha empleado con éxito durante años para localizar fallos en el rotor y problemas de entre hierro en motores.
A nivel práctico puede realizarse en paralelo con el análisis de vibraciones, utilizando los mismos colectores de datos, pero reemplazando el sensor de vibración por una pinza amperimétrica.
Los fallos mecánicos relacionados con correas, acoplamientos, alineación y otros se detectan fácilmente mediante el uso del espectro de corriente demodulado, donde es posible identificar y monitorizar la tendencia de frecuencias tales como la correspondiente a la velocidad de giro del eje, el paso de polo, el paso de correa o el paso de pala.
MCA ha demostrado ser una herramienta de mantenimiento predictivo de gran valor. Aunque es una tecnología relativamente joven y poco empleada, a día de hoy está ganando rápidamente una mayor aceptación en la industria.
¿Por qué deberíamos preocuparnos en diagnosticar problemas mecánicos con una señal de corriente demodulada si podemos ya hacerlo mediante tecnologías como el análisis de vibraciones o la termografía infrarroja?
Hay muchas razones por las que el uso de MCA para buscar problemas mecánicos puede resultar beneficioso para un programa de mantenimiento predictivo. Por ejemplo, cuando se trata de problemas en correas y acoplamientos, la corriente dará una indicación de fallo con mayor anticipación y a menudo con más precisión que el análisis de vibraciones. La cantidad de energía producida durante las primeras etapas de este tipo de fallos es relativamente baja. Cuando las correas o acoplamientos comienzan a desgastarse, a menudo no se observa ninguna anomalía en un espectro de vibración hasta que el fallo se acerca a la condición de fallo catastrófico. Un espectro de corriente demodulado tiene la capacidad de detectar el fallo con la suficiente anticipación como para proporcionar el tiempo suficiente para planificar y programar las reparaciones necesarias. Sin embargo, el MCA no pretende sustituir a un programa de monitorización de vibraciones. Su uso más acertado es como una tecnología complementaria a un buen programa de monitorización de vibraciones.
Un beneficio adicional de esta tecnología es su empleo en maquinas ubicadas en lugares apartados o zonas donde el equipo no es accesible durante su funcionamiento. En este tipo de equipos, las inspecciones visuales pueden ser difíciles, y la capacidad de realizar análisis de vibración limitada. Dependiendo de los resultados de una evaluación de riesgos, la instalación de sensores de vibración permanentes y el cableado hasta un punto de fácil acceso pueden ser demasiado costosos. En este caso, el MCA podría ser una solución mas adecuada debido a su capacidad analizar el equipo desde el armario eléctrico de control del motor.