En el mantenimiento predictivo o por condición, evaluamos el estado de los componentes mecánicos o eléctricos mediante técnicas de seguimiento y análisis, permitiéndonos programar las operaciones de mantenimiento “solamente cuando son necesarias”. Consiste esencialmente en el estudio de ciertas variables o parámetros relacionados con el estado o condición del equipo que mantenemos, como por ejemplo la vibración, temperatura, aceites, aislamientos, etc. El estudio de estos parámetros nos suministra información del estado de sus componentes y, algo también muy importante, del modo en que está funcionando dicho equipo, permitiéndonos no sólo detectar problemas de componentes sino también de diseño y de instalación. El objetivo del mantenimiento predictivo es la reducción de los costes de operación y de mantenimiento incrementando la fiabilidad del equipo.
La base del mantenimiento predictivo radica en la monitorización de los equipos, ya que debemos evaluar los parámetros antes comentados con la instalación en funcionamiento normal. No es, por tanto, necesario hacer una parada para poder evaluar la condición de los mismos, conocemos el estado de nuestras máquinas mientras están trabajando.
Con las diferentes técnicas disponibles podemos evaluar los fallos en los componentes y seguir su evolución durante largos períodos de tiempo (en ocasiones meses) antes de decidir nuestra intervención, de esta manera podemos coordinar con producción el momento más adecuado para la intervención de mantenimiento.
Para lograr una implantación exitosa de un sistema de mantenimiento predictivo es necesario seguir una estrategia. El fracaso lo tendremos asegurado si pretendemos hacer una implantación del mismo en todos nuestros equipos y más aún cuando queramos implantar varias tecnologías simultáneamente. Si además no tenemos un sistema de gestión de la información adecuado, que nos permita tratar los datos correctamente, conseguiremos tirar a la basura una importante inversión económica y lo que es peor perderemos los beneficios de una buena implantación con una alta rentabilidad económica. Además perderemos la confianza en unas tecnologías que actualmente resultan prácticamente de uso habitual.
Será necesario en primer lugar hacer una selección de los equipos que vamos a monitorizar, y que vendrá condicionada por una serie de factores entre los que se encuentran la criticidad o importancia del equipo, la accesibilidad al mismo y la información técnica que podamos disponer de él. Nos centraremos en un pequeño número de ellos, analizando que técnica podremos aplicar en un primer momento, que normalmente será el análisis de vibraciones, la cual es la de uso más ampliamente extendido. Se realizará un programa piloto con los mismos, localizando defectos, analizando causas y retroalimentando el sistema una vez hayan sido erradicados los defectos.
Después de cada campaña de medición, el resultado del análisis de cada una de las máquinas será plasmado en un informe que alimentará nuestro sistema de gestión de la información. Las soluciones software de colaboración basadas en la nube como Power-MI pueden reducir en gran medida el tiempo y el esfuerzo asociados a la creación de estos informes, proporcionando la información instantáneamente accesible, priorizada y resumida, necesaria para una toma de decisiones correctamente informada. La integración de todo el conjunto de datos disponibles de mantenimiento predictivo en un único repositorio de datos mejora en gran medida las capacidades de diagnóstico. Sin embargo, puede haber beneficios derivados aún más importantes, ya que al mismo tiempo rompe las barreras organizacionales tradicionales que han mantenido a cada grupo de personas centradas en sus respectivas tecnologías o áreas de especialización.
Una vez hayamos obtenido una valoración positiva de nuestra experiencia piloto, pasaremos a realizar una extensión de la aplicación a un mayor número de equipos y así sucesivamente hasta conseguir una implantación total con la integración de distintas tecnologías y una gestión adecuada de los datos obtenidos. Si el proceso se realiza de forma progresiva y sin prisas los resultados económicos no tardarán en ser evidentes y en muchas ocasiones sorprendentes.
Justificación técnica y económica del mantenimiento predictivo
La justificación técnica del mantenimiento predictivo es evidente, basta para ello comparar las actuaciones que realizamos cuando efectuamos un mantenimiento preventivo o correctivo en nuestras instalaciones con las que tendríamos que realizar teniendo monitorizadas nuestras máquinas y realizando un seguimiento de los parámetros a medir.
Cuando únicamente realizamos un mantenimiento correctivo, el término “mantenimiento” es sinónimo de “reparación”. No quiere ello decir que no pueda existir este tipo de intervenciones, de hecho el fin último de todo tipo de mantenimiento es reparar o sustituir componentes dañados, con la finalidad de alargar la vida útil de la máquina, y para ello son inevitables las intervenciones correctivas. Pero sí es un error centrar todas las actuaciones de mantenimiento con esta única finalidad. Ello sólo presenta una ventaja: el coste de la inversión inicial es prácticamente nulo; aunque no obstante presenta los siguientes serios inconvenientes:
-
Paradas inesperadas que normalmente suelen ocurrir cuando la producción debe ser mayor, es decir en el peor momento.
-
Estas paradas suelen ser catastróficas, ya que suelen producirse daños importantes. A veces por la pérdida de un rodamiento podemos tener serias roturas en las transmisiones.
-
Los costes de reparación de las mismas llegan a ser muy elevados.
-
La necesidad de tener piezas de repuesto en almacén se incrementa ante la incertidumbre de qué puede fallar.
-
Los riesgos de accidentes se incrementan.
-
Desconocemos totalmente el estado de nuestras máquinas.
-
Tratamos fallos crónicos como habituales sin descubrir el origen del problema, por ejemplo si un rodamiento se deteriora prematuramente y tomamos la rutina de sustituirlo, estamos ocultando un posible problema de desalineación o de desequilibrio que puede ser la causa del daño prematuro de este componente.
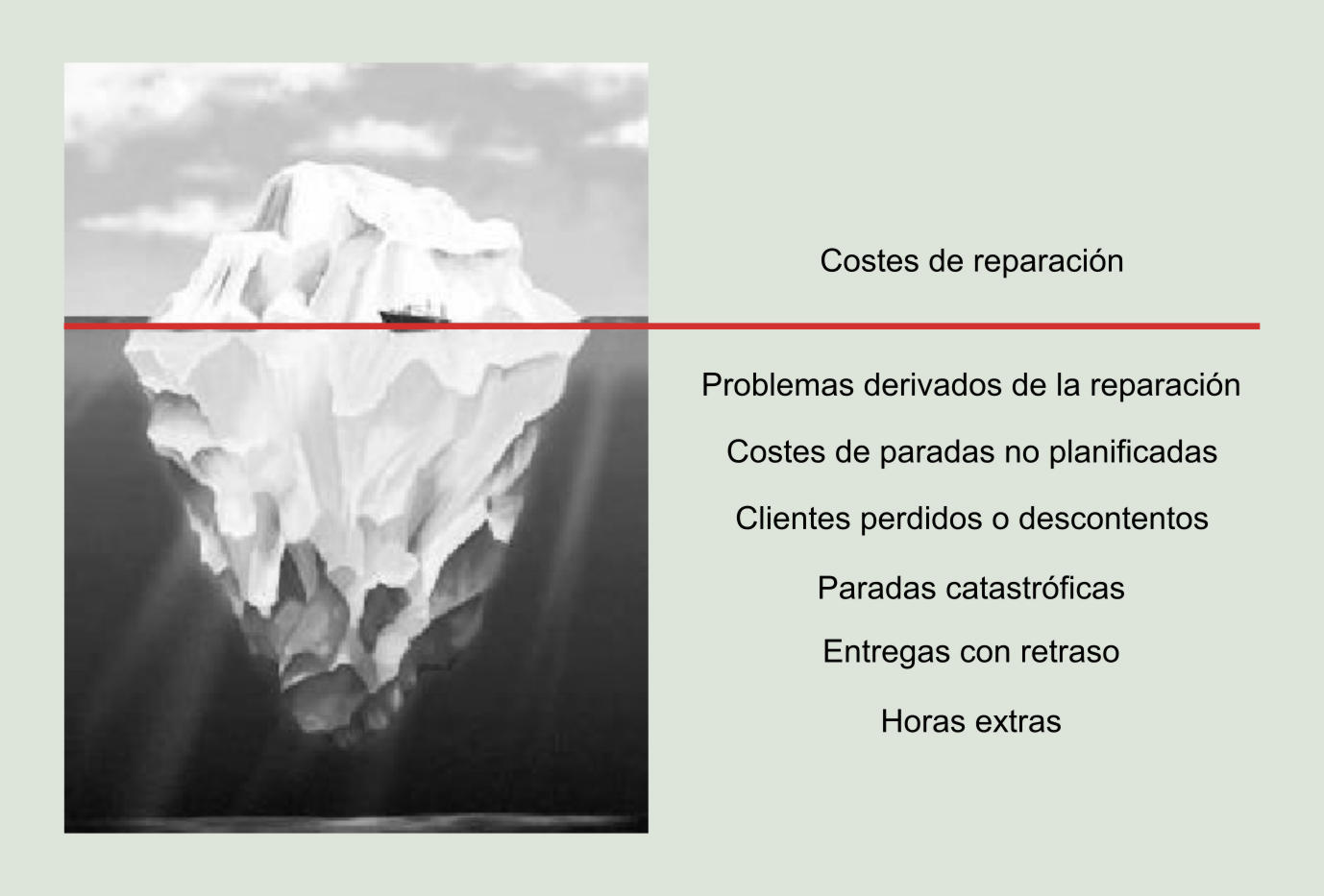
Un paso adelante lo representa el mantenimiento preventivo o programado, que se basa en la sustitución de componentes cuando suponemos que se ha agotado la vida de los mismos. El estudio teórico de sus vidas lo suele suministrar el fabricante del equipo, quien normalmente proporciona una guia de mantenimiento preventivo, con indicación de sustitución de componentes e intervalos de lubricación.
Claramente de esta forma conseguimos evitar averías, pero debemos tener cuidado con su aplicación dado que, por ejemplo, los fabricantes de rodamientos indican en sus catálogos que “la vida media de los rodamientos es aproximadamente cinco veces la vida nominal (Catálogo General SKF 4000/IISp, pág. 27)”. Eso quiere decir que si prolongásemos el uso de los rodamientos a su duración real conseguiríamos quintuplicar la vida útil de los mismos, y este argumento por si solo ya es válido en muchas ocasiones para justificar la monitorización de una máquina.
Por otro lado, el mantenimiento preventivo presenta también una serie de inconvenientes:
-
El principal radica en intervenir una máquina que está funcionando correctamente, simplemente porque le toca una revisión. Las máquinas adquieren con su funcionamiento un equilibrio que es difícil de restablecer una vez que intervenimos en las mismas y con las actuaciones preventivas estamos modificando constantemente este equilibrio de funcionamiento.
-
Cuando actuamos sobre la máquina, cambiamos componentes que normalmente están en buen estado y desconocemos el estado real de los mismos hasta que desmontamos.
-
Podemos cambiar componentes que han agotado su vida teórica y no ver otros que se encuentran en mal estado. No tenemos control sobre los daños ocultos.
-
En cuanto a su coste, puede dispararse como consecuencia de las frecuentes intervenciones en las máquinas, muchas de ellas innecesarias.
Las actuaciones de mantenimiento predictivo pasan por unos inconvenientes iniciales de elevados costes de inversión en tecnología y formación, con una rentabilidad de la misma a medio y largo plazo. Pero las ventajas son evidentes:
-
Conocemos el estado de la máquina en todo momento.
-
Eliminamos la gran mayoría de las averías.
-
Únicamente paramos o intervenimos en la máquina cuando realmente es necesario.
-
Conocemos el daño en los componentes desde una fase inicial del deterioro, permitiéndonos programar su sustitución en el momento más conveniente.
-
Al intervenir en la máquina conocemos el problema, acortando el tiempo de la reparación.
-
Podemos identificar los fallos ocultos, así como la causa raíz de fallos crónicos.
-
Reducimos el número de piezas de recambio en el almacén, adquiriéndolas solo cuando detectamos el problema en una fase inicial.
-
Conseguimos bonificaciones en primas de seguros.
-
Incrementamos la seguridad de la planta.
El gráfico que mostramos a continuación es la mejor forma de entender en que consiste el mantenimiento predictivo. Se trata de un gráfico de tendencia en el que en el eje de ordenadas evaluamos uno de los parámetros que estemos midiendo (severidad de vibración, temperatura, contaminantes, etc.) y en el eje de abscisas medimos el tiempo. Mientras la severidad de nuestro parámetro permanezca estable no tendremos porqué preocuparnos (el equipo está bien), pero cuando ésta comience a aumentar esto será un indicativo de que algo va mal. Con las diversas técnicas de análisis de estos parámetros predictivos podremos determinar con extraordinaria precisión la causa o el origen del daño.
Debido a su clara importancia merece la pena mencionar el modo en que se establecen los límites de alerta y de alarma. Existen diversas formas de establecerlos, siendo necesario siempre disponer de un histórico de medidas que nos permita realizar un estudio estadístico de las mismas.
La rentabilidad económica del mantenimiento predictivo está fuera de toda duda, como puede demostrarse con datos reales de empresas de distintos sectores donde se ha implantado o está en proceso de implantación. La evaluación de esta rentabilidad no es sencilla, y para hacerlo con la una mayor precisión es necesario disponer de una base de datos con información histórica de los activos, aunque siempre es posible realizar una mas simple estimación de los costes directos ahorrados. Incluso sin necesidad de declarar la prevención de “fallos catastróficos” se obtienen rentabilidades atractivas para competir internamente con otros proyectos en la búsqueda de financiación.
Por último, resulta interesante mencionar una aplicación adicional de las técnicas predictivas y que no está directamente relacionada con el mantenimiento y es su uso en la recepción de equipos, como método de verificación del correcto funcionamiento de los mismos o de la bondad de las reparaciones que se les hayan efectuado.