Inspecciones visuales como la piedra angular del Mantenimiento Basado en Condición: un marco completo para la integración en programas de monitoreo de condición
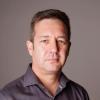
Cuando hablo con gerentes de mantenimiento, muchos se sorprenden cuando les digo que las inspecciones visuales son la primera herramienta de monitoreo de condición que debería utilizar cualquier empresa antes de invertir en instrumentos más sofisticados y sistemas en línea. Es rara la empresa que tenga un plan de inspección visual plenamente integrado con los datos del mantenimiento basado en condición. En la mayoría de los casos, las inspecciones visuales se llevan a cabo de manera informal, a menudo por personal de producción que utiliza listas de verificación en papel. Estas listas generalmente se archivan sin un análisis posterior, sin un almacenamiento sistemático de datos, y sin comunicación con el equipo de mantenimiento predictivo. Rara vez los hallazgos anómalos se documentan de una forma que informe y mejore la toma de decisiones de mantenimiento.
Cuando una empresa con uso intensivo de activos quiere comenzar su camino hacia el mantenimiento basado en condición sin un gran presupuesto, la mejor recomendación es empezar por digitalizar sus inspecciones visuales. Esto debe hacerse utilizando una metodología adecuada, basada en el análisis de activos y alineada con las metas de confiabilidad de la empresa. Este enfoque asegura que los datos recopilados visualmente —básicos, accesibles y a menudo de bajo costo— se integren de manera efectiva en el marco de mantenimiento predictivo (PdM). Las inspecciones visuales son fundamentales porque proporcionan la primera línea de defensa contra las fallas. Son accesibles, intuitivas y pueden detectar muchos problemas comunes en los activos, incluyendo fugas, pernos sueltos, suciedad y corrosión, mucho antes de que los instrumentos avanzados detecten una anomalía sutil.
Las inspecciones visuales son importantes porque dan a las organizaciones la oportunidad de identificar, registrar y comunicar las condiciones de los activos en tiempo real. Son la puerta de entrada a estrategias de mantenimiento basadas en datos, funcionando como la base para otras tecnologías PdM como el análisis de vibraciones, la termografía, el ultrasonido y el análisis de aceite. Cuando se realizan de manera sistemática, las inspecciones visuales pueden mejorar la seguridad, reducir costos y aumentar la confiabilidad de la maquinaria. En una era en la que las empresas se esfuerzan por la transformación digital, la humilde inspección visual —digitalizada, estandarizada e integrada— es un poderoso impulsor de la excelencia operativa.
¿Por qué las inspecciones visuales son importantes para el mantenimiento basado en condición?
Las inspecciones visuales preceden a todos los métodos modernos de monitoreo de condición. Antes de los sensores, el software y la analítica predictiva, los técnicos de mantenimiento confiaban en sus sentidos —particularmente la vista— para determinar el estado de un activo. Hoy en día, aunque las tecnologías digitales pueden detectar anomalías microscópicas, las inspecciones visuales siguen siendo esenciales. Son fáciles de implementar, rentables y capaces de detectar una amplia gama de fallas.
Las inspecciones visuales sobresalen en la identificación de problemas que a menudo pasan desapercibidos para la instrumentación. Por ejemplo, un operador de línea de producción podría notar una fuga de aceite, pintura descascarada en un tanque, pernos sueltos en la carcasa de una máquina o decoloración alrededor de los rodamientos. Estas señales visibles son críticas, ya que pueden indicar problemas subyacentes: problemas de lubricación, corrosión, debilidades estructurales o temperaturas anómalas.
Al diseñar e integrar adecuadamente las inspecciones visuales en el plan de mantenimiento predictivo, las empresas pueden aprovechar estos datos básicos pero invaluables. La integración asegura que las anomalías detectadas visualmente se almacenen de forma digital, se procesen y se correlacionen con datos de otras tecnologías PdM. El resultado es una comprensión más holística del estado del activo, ahorros de costos gracias a la detección temprana de fallas y una mejor toma de decisiones.
La importancia de las inspecciones visuales en la gestión de activos
Las inspecciones visuales son pruebas no destructivas que dependen de la porción visible del espectro electromagnético. Ya sea a simple vista, con ayudas ópticas, boroscopios o drones, los inspectores detectan cambios en las condiciones de la superficie, las formas, los colores y las configuraciones. Históricamente, la teoría y el desarrollo académico de la inspección visual tienen sus raíces en el campo de las pruebas no destructivas (NDT). Hoy en día, en el mantenimiento predictivo, las inspecciones visuales se reconocen como clave para el monitoreo del estado de los activos.
Incorporar las inspecciones visuales en un marco de gestión de activos se alinea con estándares internacionales reconocidos de gestión de activos. Al integrar los datos de inspección visual con estrategias de mantenimiento centradas en la confiabilidad, las empresas pueden reducir el tiempo medio entre fallas (MTBF) y extender la vida útil de los activos. Los datos de inspección visual aseguran que las decisiones de mantenimiento se basen en una imagen completa. Por ejemplo, si el análisis de vibraciones genera una alerta, una rápida verificación visual podría confirmar pernos sueltos o suciedad en las aletas de enfriamiento.
Las inspecciones visuales son versátiles. Pueden monitorear el estado de prácticamente cualquier activo tangible. Requieren capacitación mínima e instrumentación básica. Incluso a medida que avanza la transformación digital y las herramientas predictivas avanzadas ganan protagonismo, las inspecciones visuales siguen siendo la base del monitoreo de condición. Sin un enfoque estructurado, sin embargo, las empresas corren el riesgo de subutilizar esta técnica y no integrar sus hallazgos en el ecosistema PdM más amplio.
Riesgos laborales documentados
Realizar inspecciones visuales expone a los inspectores a riesgos laborales. La seguridad es primordial. Antes de recopilar datos, los inspectores deben conocer los posibles riesgos en el entorno. Entre los riesgos comunes se incluyen el trabajo en altura, riesgos eléctricos, partes de maquinaria en movimiento, exposición a productos químicos, espacios confinados y pérdida de apoyo o equilibrio. Cada ruta de inspección debe resaltar estos riesgos para que los inspectores puedan tomar medidas preventivas, usar el equipo de protección personal (EPP) adecuado y seguir protocolos específicos del sitio.
Al digitalizar las inspecciones visuales y utilizar tabletas o teléfonos inteligentes, las empresas pueden informar automáticamente a los inspectores sobre peligros conocidos antes de que se acerquen a un activo. Esta integración de la seguridad ocupacional en el plan de inspección evita accidentes y garantiza el cumplimiento de las normativas de salud y seguridad en el trabajo. Las pautas de seguridad y las evaluaciones de riesgos deben integrarse en el sistema de gestión del mantenimiento, de modo que los inspectores reciban recordatorios e instrucciones durante cada ruta de inspección.
Fallas detectables mediante inspecciones visuales
Las inspecciones visuales pueden detectar una amplia gama de fallas. Cada tipo de falla corresponde a síntomas observables:
- Parámetros de proceso anómalos: Indicadores legibles como manómetros o caudalímetros podrían mostrar valores fuera de rango.
- Obstrucción: Filtros, tuberías, conductos o válvulas podrían estar bloqueados por suciedad, escombros u objetos extraños.
- Roturas: Grietas visibles, partes fracturadas o componentes rotos.
- Deformación: Estructuras dobladas o deformadas, formas distorsionadas de tuberías, carcasas o protectores de máquinas.
- Deterioro: Desgaste gradual, erosión, partes oxidadas, pintura descascarada o materiales degradados.
- Suciedad: Acumulación de mugre, polvo, aceite o grasa en superficies, filtros o componentes sensibles.
- Alta temperatura: Decoloración, aislamiento derretido, deformaciones inducidas por calor o lecturas de temperatura fuera de los rangos normales.
- Humedad: Condensación, moho o humedad en áreas que deberían estar secas.
- Fugas: Escapes de fluidos, goteo de aceite, vapor, fugas de gas o manchas visibles alrededor de sellos y juntas.
- Pernos sueltos: Sujetadores que se han aflojado o están visiblemente sueltos, causando vibración o desalineación.
- Mala conexión (eléctrica): Marcas de quemadura, terminales decoloradas, cables sueltos o evidencia de arcos.
- Pérdida de hermeticidad: Tanques o recipientes que ya no están sellados, permitiendo la fuga de fluidos o gases.
- Problema de lubricación: Falta de lubricante, grasa contaminada, aceite espumoso o lubricante con color inadecuado.
- Desajuste: Componentes fuera de alineación, desalineación del eje o ajuste inadecuado de piezas.
- Componentes faltantes: Piezas o accesorios que no están donde deberían estar.
- Ruido anormal: Un siseo por fuga, una correa chirriante, una carcasa que vibra, detectados por el oído del inspector.
- Corrosión: Óxido, picaduras u oxidación en superficies metálicas.
- Problemas estructurales: Grietas o inestabilidad en soportes, cimientos, pasarelas o estructuras.
Al definir estos modos de falla y capacitar a los inspectores, las inspecciones visuales se convierten en una técnica estandarizada. En lugar de observaciones vagas, los inspectores reportan categorías de fallas conocidas, lo que permite un análisis más ágil y una toma de decisiones más rápida.
Metodología: el marco Visual-PdM
Implementar las inspecciones visuales de manera sistemática y con datos de calidad implica varios pasos. Piénselo como un ciclo continuo que integra las inspecciones visuales en un plan de mantenimiento predictivo.
Inventario y clasificación de activos
Comience creando una taxonomía jerárquica de todos los activos. Clasifíquelos por criticidad, considerando su función, impacto en el tiempo de inactividad, implicaciones de seguridad y datos históricos de fallas. Los activos críticos pueden requerir inspecciones más frecuentes o disparadores basados en condición.
Encuestas de inspección visual y directrices
Defina puntos de inspección para cada activo. Para cada punto, especifique la condición normal, las posibles fallas, los límites aceptables de los parámetros y las unidades de medida. Integre esta información en las directrices o listas de verificación de inspección. Al hacerlo, los inspectores cuentan con una referencia que garantiza uniformidad y coherencia.
Instrumentación y ayudas ópticas
Las inspecciones visuales van más allá de la simple vista. Lámparas, lupas, espejos, boroscopios, endoscopios, indicadores de temperatura, manómetros y vibrómetros pueden mejorar la precisión. Considere tabletas o smartphones con cámaras integradas para la documentación. Las fibras ópticas, lámparas halógenas y linternas ayudan a inspeccionar lugares oscuros y confinados. Algunas inspecciones pueden requerir herramientas especializadas como calibradores Vernier, micrómetros o relojes comparadores para mediciones dimensionales.
Integración digital
La digitalización de las inspecciones es crucial. Las tabletas y los smartphones reemplazan los formularios en papel, eliminando la necesidad de doble ingreso de datos. Los datos se registran en tiempo real, acompañados de fotografías, notas de voz y lecturas de parámetros. Una vez completadas las inspecciones, los datos se sincronizan automáticamente con una plataforma de mantenimiento predictivo. Allí pueden correlacionarse con resultados de vibración, termografía o análisis de aceite. Esta integración es la piedra angular del mantenimiento predictivo, permitiendo una evaluación holística del estado de los activos.
Diseño de tareas e integración de la seguridad
Cada ruta de inspección debe incluir instrucciones sobre riesgos laborales, EPP requerido y procedimientos de seguridad. Por ejemplo, antes de que un inspector revise una bomba en un espacio confinado, la tableta debería mostrar advertencias de peligro. Asimismo, si los datos de vibración sugieren un modo de falla, la ruta de inspección puede ajustarse dinámicamente para centrarse en esa máquina en particular.
Planificación y optimización de rutas
Optimizar las rutas de inspección ahorra tiempo y recursos. Algoritmos propietarios pueden considerar la ubicación de los activos, su criticidad y disparadores basados en condición. Por ejemplo, si la termografía indica un punto caliente, la siguiente ronda de inspección incluye una verificación visual enfocada en esa zona. Esta adaptabilidad asegura la detección oportuna de problemas emergentes.
Formación y mejora continua
Capacite a los inspectores para reconocer fallas y utilizar las herramientas digitales de manera efectiva. Con el tiempo, revise los datos para mejorar las directrices y refinar la frecuencia de inspección. Analice tendencias en fallas, compare con otros datos PdM y ajuste las estrategias. La mejora continua garantiza que las inspecciones visuales evolucionen con las condiciones de la planta, las nuevas tecnologías y las lecciones aprendidas.
Consideraciones prácticas, aplicaciones integrativas
Los estudios de caso destacan los beneficios de integrar las inspecciones visuales con otras técnicas PdM. Considere una central eléctrica que utiliza análisis de vibraciones para detectar anomalías en turbinas. Cuando los niveles de vibración superan un umbral, la planta envía un inspector a buscar problemas visibles: fugas, pernos sueltos o grietas estructurales. Si el inspector encuentra pernos sueltos, el equipo de mantenimiento los ajusta de inmediato, evitando una posible falla catastrófica. Esta sinergia reduce el tiempo de inactividad y ahorra costos al intervenir tempranamente.
Otro ejemplo podría incluir drones para áreas inaccesibles, como la parte superior de una góndola de turbina eólica. En lugar de enviar personal a gran altura, un dron equipado con una cámara realiza la inspección visual. Si el dron captura imágenes de deformación o grietas en las palas, el equipo de mantenimiento planifica acciones correctivas. Del mismo modo, robots en espacios confinados pueden realizar video-endoscopias para detectar corrosión interna en tuberías sin exponer a los inspectores a entornos peligrosos.
La tecnología vestible, la realidad aumentada (AR) y la realidad virtual (VR) mejoran aún más la capacitación y la asistencia remota. AR puede guiar a los inspectores superponiendo instrucciones en la imagen de la cámara en vivo, señalando puntos de inspección, áreas de riesgo o puntos problemáticos conocidos. VR se puede utilizar para entrenamiento, simulando escenarios reales de inspección en un entorno seguro.
Todas estas herramientas y técnicas, cuando se integran en un único ecosistema de mantenimiento predictivo, se potencian mutuamente. Los datos de inspección visual pueden confirmar sospechas planteadas por sensores, proporcionar contexto a lecturas anómalas o guiar pruebas más avanzadas. El resultado es una defensa robusta y de múltiples capas contra fallas e ineficiencias.
Monitoreo, medición de KPI y optimización a largo plazo
Para asegurar la mejora continua, los gerentes de mantenimiento deben rastrear indicadores clave de rendimiento (KPI). Algunos ejemplos incluyen:
- Cobertura de inspección: Porcentaje de puntos de inspección identificados que realmente se revisan por ruta.
- Calidad de datos: Integridad y claridad de los registros de inspección, incluidas fotos y lecturas de parámetros.
- Tiempo de respuesta: Qué tan rápido los hallazgos visuales anómalos desencadenan acciones correctivas.
- Tasa de fallas: Reducción de fallas inesperadas como resultado de la detección visual oportuna.
- Ahorro de costos: Reducción cuantificable en costos de mantenimiento debido a la intervención temprana y menos fallas catastróficas.
El análisis de tendencias a lo largo del tiempo permite a las empresas refinar los intervalos de inspección, las rutas de inspección y los umbrales de activación. A medida que el aprendizaje automático (ML) y la inteligencia artificial (AI) avanzan, los datos visuales pueden procesarse automáticamente para detectar anomalías. Los algoritmos de reconocimiento de imágenes pueden identificar puntos de corrosión o grietas, señalando problemas sin intervención humana. Combinados con datos históricos, las herramientas impulsadas por AI pueden predecir qué activos tienen mayor riesgo, guiando a los inspectores al lugar correcto en el momento adecuado.
A largo plazo, integrar las inspecciones visuales en un plan estratégico de mantenimiento predictivo significa que estas inspecciones dejan de ser una actividad aislada. Se convierten en un insumo clave de un ecosistema más amplio de datos y análisis. La cultura de mantenimiento de la empresa pasa de ser reactiva a proactiva, respaldada por flujos de datos estables y confiables de múltiples fuentes.
Conclusión
Las inspecciones visuales, aunque a menudo subestimadas, forman la capa fundamental de cualquier estrategia sólida de mantenimiento predictivo. Proporcionan información inmediata e intuitiva sobre las condiciones de los activos. Al formalizar las inspecciones visuales mediante un diseño adecuado, digitalización e integración, las empresas pueden convertir una técnica simple y de bajo costo en una poderosa herramienta de mantenimiento predictivo. A medida que la transformación digital remodela el mantenimiento industrial, las inspecciones visuales se vuelven insustituibles como fuentes de datos, complementando y reforzando las tecnologías avanzadas de monitoreo de condición.
Carlos, al adoptar una metodología estructurada —como el marco Visual-PdM— aseguras que tus inspecciones visuales ya no sean solo una formalidad o un ejercicio en papel. En cambio, se convierten en componentes dinámicos de una estrategia basada en datos. Este enfoque conduce a una mayor seguridad, ahorros de costos significativos, mayor confiabilidad del equipo y, en última instancia, una ventaja competitiva más sólida.
Puntos clave
- Comienza tu viaje de mantenimiento basado en condición digitalizando las inspecciones visuales.
- Integra los datos de inspecciones visuales con otras técnicas de mantenimiento predictivo.
- Utiliza categorías de fallas estandarizadas y directrices para mejorar la coherencia y el análisis de datos.
- Incorpora la seguridad ocupacional en cada ruta de inspección, garantizando el bienestar del inspector.
- Optimiza las rutas de inspección con algoritmos y ajusta las frecuencias de inspección según datos en tiempo real.
- Adopta nuevas tecnologías como drones, AR, VR y sistemas de iluminación avanzados para mejorar la calidad de las inspecciones.
- Realiza un seguimiento continuo de los KPI, analiza tendencias y ajusta estrategias para la optimización a largo plazo.
- Considera las inspecciones visuales como una técnica predictiva central, no como una idea tardía.
References
Armstrong, M. (2010). Condition Monitoring, Asset Management, and Maintenance. Industrial Press.
ASNT (2010). Visual Testing (VT) Handbook. American Society for Nondestructive Testing.
Beebe, R. (2004). Predictive Maintenance of Pumps Using Condition Monitoring. Elsevier.
ISO 14224:2006. Petroleum, Petrochemical and Natural Gas Industries—Collection and Exchange of Reliability and Maintenance Data for Equipment.
ISO 45001:2018. Occupational Health and Safety Management Systems—Requirements with Guidance for Use.
ISO 55000:2014. Asset Management—Overview, Principles and Terminology.
Jardine, A.K.S., Lin, D., & Banjevic, D. (2006). A Review on Machinery Diagnostics and Prognostics Implementing Condition-Based Maintenance. Mechanical Systems and Signal Processing, 20(7), 1483–1510.
Moubray, J. (1997). Reliability-Centered Maintenance. Industrial Press.
Maintenance Intelligence LLC. Designing a Comprehensive and Adaptive Visual Inspection Methodology for Integration into Predictive Maintenance Programs. Internal White Paper.
¿Qué es Power-MI?
Power-MI es una herramienta en la nube que le permite diseñar y gestionar su mantenimiento predictivo con todas las técnicas en una plataforma. Informes fáciles, órdenes de trabajo automáticas e integración a CMMS.
Leer más