Mi primera implementación de mantenimiento predictivo
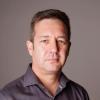
En mayo de 2001 fui contratado por Procesadora de Acero de El Salvador (Proaces) como ingeniero de mantenimiento con el principal objetivo de implementar mantenimiento predictivo en la planta. La planta de Proaces no era desconocida para mí ya que eran clientes de la empresa para la que trabajaba anteriormente, por lo que ya había hecho ahí análisis de vibraciones, balanceos dinámicos y mediciones eléctricas. Los gerentes de Proaces fueron explícitos al decirme que empezaría desde cero.
La implementación del mantenimiento predictivo fue comprar un instrumento y salir a medir. Luego supe que eso es lo que más del 90% de los departamentos de mantenimiento hacen. Pero, ¿cómo decidimos ir por ese camino?
"Comprá un analizador y salí a medir ¡ya!"
Esa consigna que me dio mi jefe, un veterano de la industria del acero, podría parecer simplista y precipitada, pero realmente la orden tenía mucho sentido.
En mi primer día de trabajo, caí en la cuenta que muchos de mis compañeros no sabían que se iba a contratar a alguien para mantenimiento (yo). Ese día, en una reunión improvisada, me presentaron al departamento de mantenimiento y, aunque no quedó claro cuál era mi cargo, sí explicaron que sería yo el encargado de implementar mantenimiento predictivo y “otras cosas” que poco a poco me fueron delegando. En esa reunión entendí que la razón de mi contratación había sido una parada de producción que había hecho perder “mucho dinero” a la empresa. El origen de la tragedia había sido un fallo que típicamente se detecta con análisis de vibraciones.
Era obvio que mi misión era implementar un plan de monitoreo de vibraciones para anticipar ese tipo de fallos, con especial énfasis en las máquinas críticas. El plan de mantenimiento predictivo se limitaba a las rutas de colección de vibraciones y su análisis.
Compramos un equipo marca SKF al único proveedor local que ofrecía esos productos. La empresa de suministro industrial que vendió el equipo era representada en Proaces por el Sr. Polanco, un simpático técnico-comercial quien un día me invitó a almorzar después de hacer unas pruebas de campo con su equipo de demostración. Ante mi negativa de ser invitado, me convenció diciéndome que su empresa pagaba.
Supe que la entrega del equipo se demoró debido a que mi compañero de compras estaba negociando con el Sr. Polanco. En la oferta del Sr. Polanco estaba incluido un entrenamiento en el uso del equipo y un curso básico de análisis de vibraciones. Mi sorpresa fue que el entrenamiento lo daría un ingeniero de SKF Colombia y no el Sr. Polanco, quien tanto parecía saber de vibraciones y del equipo. No esperamos al formador y decidimos empezar nuestras rutas de medición antes del entrenamiento ya que las visitas al país del formador eran según una agenda interna de SKF. Así fue negociado con “compras” a cambio de un descuento en el precio.
Al llegar el equipo a Proaces, hice alarde de mi experiencia en análisis de vibraciones y decidimos desempacarlo y ponerlo en marcha. Sin esperar al entrenamiento, instalamos el software con el CD que venía con el instrumento y a trompicones creamos nuestra primera ruta. En aquel entonces, la única forma de seguir instrucciones era leyendo el manual del equipo, una práctica casi en desuso en mantenimiento 20 años después. El entrenamiento lo recibimos unos meses después y pocas cosas nuevas aprendimos.
El inicio del plan de mantenimiento predictivo
Me asignaron a Beto, un supervisor de mantenimiento mecánico, con evidente experiencia, condición física y buen criterio para toma de decisiones. El día que el gerente de mantenimiento me lo presentó, parecía estar despidiéndose de su hijo predilecto. Junto a Beto diseñamos las rutas de medición y empezamos a colectar los datos de vibraciones. Decidimos que analizaríamos juntos y así le enseñaría los detalles del análisis espectral y trucos para conocer el origen de las vibraciones en máquinas rotativas.
Empezamos a detectar una cantidad de fallos que llamó la atención de mantenimiento y de los gerentes de producción. Ante su escepticismo sobre nuestros diagnósticos, yo les explicaba cómo se pueden detectar los fallos en un espectro de vibraciones. Eso hizo ganarme mi apodo en la planta: “la NASA”, en graciosa alusión a la agencia espacial estadounidense y sus tecnologías espaciales.
La duda del predictivo
Aproximadamente dos meses después de ejecutar el plan de mantenimiento predictivo, un día a primera hora, después de ducharme, vi que mi celular notificaba varias llamadas perdidas entre las 5 y 7 de la mañana provenientes de la oficina del gerente de ingeniería y de otros compañeros de trabajo. En aquel entonces no se acostumbraba a dormir con el celular y no se tenía la costumbre de consultarlo cada vez que fuera posible. Al devolver la llamada, la secretaria del departamento me recomendó con complicidad llegar lo antes posible a la planta ya que pasaba algo grave y me estaban buscando.
Al llegar a planta, me di cuenta que me buscaban no para solucionar el problema, sino para pedirme explicaciones sobre el porqué no anticipé el problema. El puente grúa sobre el laminador (el corazón de la planta) falló. El puente se atascó en un tramo, y dar con el origen de la inmovilidad del puente-grúa ante las órdenes del operador tomó varias horas. Resolver el problema tomó casi un día. La verdadera causa del atasco era desconocida.
Ese día, ante la situación, caí en la cuenta que no sólo dudaban de “el predictivo”, sino que yo era culpable de no haber avisado anticipadamente del problema y haberles dado una sensación que todo estaba bajo control y que no volveríamos a tener paradas de planta. La razón de esto era que hacíamos pruebas de vibraciones en las grúas y nunca detectamos síntomas o señales de fallos en las mismas. Para ser sincero, incluso yo dudé de mis conocimientos y de la tecnología.
Posteriormente se pudo demostrar que el atasco era debido a la desalineación del paralelismo de los rieles y las ruedas del puente. Eso era ajeno al alcance de un análisis de vibraciones, que era básicamente pruebas de run-up y cost-down en el polipasto. Esas aclaraciones pasaron prácticamente desapercibidas ya que habían otro problemas que atender en ese momento. Mis compañeros ya veían las recomendaciones de la NASA y de Beto con ojos de incredulidad y la observación solía ser un burlesco “¿Estás seguro?”.
No puedo decir que nos anticipamos a todos los fallos detectables con análisis de vibraciones, ya que se nos escaparon algunos. Pero sí era evidente la cantidad de fallos que habíamos detectado a tiempo y, gracias al mantenimiento correctivo hecho, pudimos evitar varias paradas y reparaciones costosas de maquinaria.
La esencia del predictivo
Lo habitual en El Salvador era trabajar también los sábados hasta el mediodía. Los efectos de las fiestas de los viernes y las ganas de salir exactamente después de 4 horas de trabajo, me motivaron a utilizar esos días para hacer estadísticas del mantenimiento predictivo para no salir a planta a medir. Nos juntábamos Beto y yo a pasar uno a uno los informes de la semana y clasificar los fallos que habíamos detectado. Se evidenciaba que la mayoría de los fallos detectados no eran por el análisis de vibraciones, sino por las observaciones de Beto mientras colectaba datos. Empezamos así a reflexionar si no hubiese sido mejor idea empezar por rutas de inspección visual y luego comprar un instrumento.
Igualmente, solía suceder que aparecía ante mi algún compañero de producción ofuscado reprochándome que había habido un fallo grave y yo no le había dicho nada con anticipación. Daba igual que el fallo fuera en un panel eléctrico, en las guías de los mandrinos, PLCs o incluso en el aceite de emulsión. Ante eso mi explicación era sencilla: “yo hago análisis de vibraciones, no tengo una bola de cristal”. No obstante, la reflexión de los compañeros era válida: ¿por qué el predictivo sólo es análisis de vibraciones?
A golpes entendí que la esencia del mantenimiento predictivo no es comprar instrumentación, recibir un curso y salir a medir. La esencia es analizar las máquinas críticas, la probabilidad de que fallen, la consecuencia de que fallen, los fallos que pueden tener y, con esa información, seleccionar las tecnologías con las que deben ser analizadas y su periodicidad de inspección. La combinación y el cruce de información de varias técnicas predictivas suelen dar mejores diagnósticos.
¿Qué es Power-MI?
Power-MI es una herramienta en la nube que le permite diseñar y gestionar su mantenimiento predictivo con todas las técnicas en una plataforma. Informes fáciles, órdenes de trabajo automáticas e integración a CMMS.
Leer más