La curva P-F: una piedra angular en el mantenimiento basado en la condición
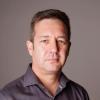
En el panorama industrial actual, la eficiencia y la confiabilidad son críticas. Los tiempos de inactividad no planificados y las fallas de equipos conducen a pérdidas financieras, interrupciones en la producción y problemas de seguridad. El mantenimiento basado en la condición (CBM) se ha convertido en una estrategia clave para garantizar la confiabilidad y longevidad de los activos, con la curva P-F desempeñando un papel central. Esta herramienta conceptual representa la progresión de la degradación de un activo desde el punto inicial de falla potencial hasta la falla funcional completa.
Esta publicación de blog es parte de una serie de artículos académicos sobre mantenimiento basado en la condición. El concepto de la curva P-F es particularmente importante para gerentes de mantenimiento, gerentes de planta, ingenieros de confiabilidad e ingenieros industriales que buscan mantener los activos funcionando al máximo rendimiento. En esta publicación, exploramos los orígenes de la curva P-F, su aplicación práctica utilizando un ejemplo de falla de un rodamiento y su impacto en las estrategias de mantenimiento. También destacamos los beneficios económicos del mantenimiento predictivo y cómo la curva P-F apoya la optimización de costos.
Orígenes del concepto de la curva P-F
Originalmente, las estrategias de mantenimiento eran reactivas, abordando las fallas solo después de que ocurrían. Este enfoque resultaba en altos costos y largos tiempos de inactividad. El mantenimiento preventivo marcó un progreso al implementar intervenciones programadas, pero aún carecía de precisión. La introducción del mantenimiento centrado en la confiabilidad (RCM), pionero por expertos como John Moubray, enfatizó la comprensión de los modos de falla y el desarrollo de estrategias de mantenimiento a medida. Dentro de este marco, la curva P-F emergió como una herramienta visual clave que representa el proceso de deterioro de la condición, permitiendo una mejor predicción y prevención de fallas.
Falla de rodamiento: un ejemplo práctico de la curva P-F
Para comprender la curva P-F, consideremos un rodamiento en una máquina industrial.
- Punto P (Falla Potencial): Este es el momento en que una anomalía se vuelve detectable a través de técnicas de monitoreo de condición pero aún no ha afectado el rendimiento del activo. Para un rodamiento, esto podría ser el inicio de micropitting, que solo puede detectarse mediante técnicas avanzadas como el análisis de vibraciones.
- Punto F (Falla Funcional): Ocurre cuando la máquina ya no puede desempeñar correctamente su función principal. Bajo el concepto de RCM, la falla funcional significa que el rendimiento de la máquina está comprometido hasta el punto de no cumplir su propósito previsto. Si la máquina se detiene, también puede causar daños secundarios. En el ejemplo del rodamiento, esto podría significar daños en la carcasa del rodamiento o incluso un eje roto, aumentando los costos de reparación y el tiempo de inactividad.
El intervalo P-F
El intervalo P-F es el lapso de tiempo entre los puntos P y F, representando la ventana de oportunidad para la intervención de mantenimiento. En el ejemplo del rodamiento, la detección temprana permite a los equipos de mantenimiento reparar o reemplazar el rodamiento durante tiempos de inactividad programados, evitando paradas inesperadas.
Implicaciones de mantenimiento de la curva P-F
- Optimización de intervalos de inspección: Comprender el intervalo P-F ayuda a optimizar los horarios de inspección para maximizar las posibilidades de detectar problemas temprano. Una práctica común es programar inspecciones en menos de la mitad del intervalo P-F para asegurar múltiples oportunidades de identificar fallas potenciales.
- Beneficios económicos: Abordar los problemas en el punto P es mucho más rentable en comparación con manejar fallas en el punto F. Los ahorros en costos (Ahorros = Cost_F - Cost_P) incluyen gastos de personal, repuestos y tiempos de inactividad no planificados, haciendo del mantenimiento predictivo un enfoque financieramente sólido.
Implementación del mantenimiento basado en la condición
La curva P-F enfatiza la importancia de estrategias de mantenimiento proactivas:
- Recolección de datos: Utilizar herramientas de monitoreo de condición para recopilar datos sobre la salud del activo.
- Análisis e informes: Analizar los datos para detectar fallas potenciales y emitir recomendaciones accionables.
- Ejecución de mantenimiento: Abordar los problemas dentro del intervalo P-F para prevenir tiempos de inactividad inesperados.
Mejorando la colaboración entre analistas y equipos de mantenimiento
Un desafío común en el mantenimiento predictivo es la desconexión entre analistas y equipos de mantenimiento. Para mejorar la colaboración, los analistas deben proporcionar recomendaciones claras y accionables, y las empresas deben utilizar sistemas integrados que agilicen el proceso de convertir informes de análisis en órdenes de trabajo.
Avances tecnológicos que impactan la curva P-F
- IoT y sensores inteligentes: Los datos en tiempo real de sensores inteligentes permiten la detección temprana de anomalías, proporcionando información inmediata sobre la salud del activo.
- Aprendizaje automático: Los algoritmos predictivos mejoran la precisión de las estimaciones del intervalo P-F y ayudan a optimizar los horarios de mantenimiento.
Conclusiones
La curva P-F es una herramienta fundamental para el mantenimiento predictivo, permitiendo a las organizaciones prevenir fallas, reducir costos y mejorar la confiabilidad de los activos. Al enfocarse en la intervención temprana, optimizar los intervalos de inspección y aprovechar la tecnología, los equipos de mantenimiento pueden mejorar la eficiencia y contribuir a un resultado final más sólido.
Puntos clave
- La curva P-F es un concepto para entender cómo anticipar fallas y programar mantenimiento oportuno.
- Actuar dentro del intervalo P-F minimiza costos y tiempos de inactividad que pueden cuantificarse en términos monetarios.
- La integración tecnológica, incluyendo IoT y aprendizaje automático, mejora la efectividad del mantenimiento predictivo.
Para maximizar los beneficios del mantenimiento predictivo, establezca procesos claros, mejore la comunicación del equipo y enfoque en el impacto económico de las intervenciones tempranas.
Referencias
Moubray, J. (1997). Reliability-Centered Maintenance. Industrial Press Inc.
Smith, A. M., & Hinchcliffe, G. R. (2003). RCM: Gateway to World Class Maintenance. Elsevier.
Mobley, R. K. (2002). An Introduction to Predictive Maintenance. Butterworth-Heinemann.
Wienker, M., Henderson, K., & Volkerts, J. (2016). The Computerized Maintenance Management System: An Essential Tool for World Class Maintenance. Procedia Engineering, 138, 413-420.
Gupta, P., & Mishra, D. K. (2016). Predictive maintenance of industrial machines using IoT. International Journal of Computer Applications, 975, 8887.
Torres, C. E. "How to Calculate Condition-Based Maintenance Savings." Reliable Plant [en línea]. Disponible en: www.reliableplant.com/Read/31988/how-to-calculate-conditon-based-maintenance-savings, [acceso 29 de octubre de 2024].
¿Qué es Power-MI?
Power-MI es una herramienta en la nube que le permite diseñar y gestionar su mantenimiento predictivo con todas las técnicas en una plataforma. Informes fáciles, órdenes de trabajo automáticas e integración a CMMS.
Leer más