Categorías de mantenimiento: Una guía integral basada en ISO 14224
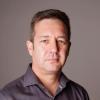
En el sector industrial el mantenimiento es mucho más que una tarea rutinaria; es el pilar de la seguridad, la confiabilidad y la eficiencia operativa. Durante mis más de 20 años en gestión de mantenimiento he presenciado de primera mano cómo una estrategia de mantenimiento bien estructurada puede transformar las operaciones. Esta guía profundiza en las categorías de mantenimiento descritas en ISO 14224:2016, enriquecida con conocimientos prácticos.
Visión general de las categorías de mantenimiento
ISO 14224 ofrece un marco estandarizado para clasificar las actividades de mantenimiento, divididas principalmente en dos categorías principales:
- Mantenimiento preventivo (2a)
- Mantenimiento correctivo (2b)
Estas categorías nos ayudan a entender cuándo ocurren las actividades de mantenimiento en relación con la falla del equipo—ya sea antes (proactivo) o después (reactivo) de un incidente.
Mantenimiento preventivo (2a)
El mantenimiento preventivo implica medidas proactivas para prevenir fallas en el equipo y asegurar una operación continua. Al anticipar posibles problemas, los abordamos antes de que escalen a problemas significativos, salvaguardando así la integridad operativa.
Mantenimiento basado en la condición - CBM (3a)
El mantenimiento basado en la condición es un enfoque dinámico que se basa en monitorear la condición real del equipo para tomar decisiones de mantenimiento informadas. Esta estrategia aprovecha datos en tiempo real y evaluaciones periódicas para detectar anomalías tempranas.
Ejemplo: En una refinería, monitorear continuamente los niveles de vibración de compresores y bombas ayuda a identificar desgaste de rodamientos o desalineaciones. La detección temprana permite intervenciones oportunas, evitando paradas inesperadas y costosas reparaciones.
Otro ejemplo: Utilizar cámaras termográficas para monitorear paneles eléctricos puede revelar componentes sobrecalentados. Identificar estos "puntos calientes" temprano previene fallas que podrían llevar a interrupciones en la producción o riesgos de seguridad.
Pruebas e inspecciones (4a)
Las pruebas e inspecciones regulares evalúan tanto el rendimiento funcional como la integridad estructural del equipo. Este enfoque sistemático descubre posibles problemas que no son evidentes durante la operación normal.
Ejemplo: Realizar mediciones de espesor por ultrasonido en tanques de almacenamiento para detectar corrosión interna. En la industria petroquímica, esta práctica es esencial para prevenir fugas o fallas catastróficas de tanques que podrían tener implicaciones ambientales y de seguridad.
Monitoreo de condición (4b)
El monitoreo de condición implica la evaluación continua o periódica de la salud del equipo utilizando herramientas de diagnóstico avanzadas y sensores.
Ejemplo: Implementar programas de análisis de aceite para cajas de engranajes críticas. Al analizar las propiedades del lubricante y detectar contaminantes, podemos predecir patrones de desgaste y programar el mantenimiento antes de que ocurra una falla.
Mantenimiento predeterminado (3b)
El mantenimiento predeterminado, a menudo referido como mantenimiento programado o basado en tiempo, implica realizar actividades de mantenimiento en intervalos establecidos, independientemente de la condición actual del equipo. Este enfoque se basa en datos estadísticos, recomendaciones del fabricante o mejores prácticas de la industria.
Pruebas periódicas (4c)
Realizar pruebas en intervalos regulares asegura que el equipo continúe cumpliendo con los estándares operativos y de seguridad.
Ejemplo: Probar la resistencia de aislamiento de motores de alta tensión anualmente. Esta práctica ayuda a prevenir fallas eléctricas que podrían interrumpir la producción y representar riesgos de seguridad.
Reemplazo programado (4d)
Reemplazar componentes en base a un programa fijo, informado por ciclos de vida esperados, previene fallas debido al desgaste.
Ejemplo: Cambiar placas de desgaste en trituradoras cada seis meses para mantener la eficiencia en operaciones mineras. Este reemplazo proactivo evita tiempo de inactividad inesperado y mantiene tasas de producción consistentes.
Servicio programado (4e)
Servicios de rutina como limpieza, lubricación y ajustes se realizan en momentos predeterminados para mantener un rendimiento óptimo del equipo.
Ejemplo: Lubricar rodamientos de transportadores cada tres meses en una planta de empaque. La lubricación regular previene desgaste excesivo, reduce el consumo de energía y extiende la vida útil del equipo.
Mantenimiento correctivo (2b)
El mantenimiento correctivo implica acciones tomadas después de que ha ocurrido una falla, con el objetivo de restaurar el equipo a su estado operativo. Aunque es de naturaleza reactiva, un mantenimiento correctivo efectivo minimiza el tiempo de inactividad y previene problemas recurrentes.
Mantenimiento correctivo inmediato (4f)
Reparaciones urgentes realizadas inmediatamente después de una falla que impacta significativamente las operaciones. El objetivo es restaurar la funcionalidad lo más rápido posible.
Ejemplo: Abordar rápidamente una caldera averiada en una planta de energía para restablecer la generación de electricidad. La acción inmediata es crucial para evitar cortes prolongados y satisfacer la demanda de energía.
Mantenimiento correctivo diferido (4g)
Reparaciones que pueden posponerse sin afectar severamente las operaciones, programadas para un momento más conveniente cuando los recursos están disponibles.
Ejemplo: Planificar la reparación de una unidad de HVAC no crítica durante el próximo paro programado. Al diferir el mantenimiento, optimizamos la asignación de recursos sin impactar las necesidades operativas inmediatas.
Mantenimiento oportunista
Aunque no está definido explícitamente en ISO 14224, el mantenimiento oportunista es un enfoque práctico donde las tareas de mantenimiento se realizan durante tiempos de inactividad no programados o junto con otras actividades de mantenimiento. Esta estrategia maximiza la eficiencia y minimiza el tiempo de inactividad adicional.
Ejemplo: Durante una parada inesperada de la línea de producción, reemplazar componentes que se acercan al final de su vida útil. Este enfoque reduce la frecuencia de paradas programadas y hace un uso eficiente de las ventanas de mantenimiento disponibles.
Ventajas y desventajas de cada tipo de mantenimiento
Desarrollar una estrategia de mantenimiento efectiva requiere comprender las fortalezas y limitaciones de cada enfoque.
Mantenimiento basado en la condición
Advantages include early failure detection, which identifies potential issues before they become critical. Optimized maintenance scheduling allows maintenance to be performed based on actual equipment condition, reducing unnecessary interventions. Cost efficiency is achieved by preventing catastrophic failures, thereby reducing repair costs and downtime.
Ventajas:
- Detección temprana de fallas: Identifica problemas potenciales antes de que se vuelvan críticos.
- Programación de mantenimiento optimizada: El mantenimiento se realiza en función de la condición real del equipo, reduciendo intervenciones innecesarias.
- Eficiencia de costos: Previene fallas catastróficas, reduciendo costos de reparación y tiempo de inactividad.
Desventajas:
- Inversión inicial: Requiere equipos de monitoreo avanzados y capacitación.
- Gestión de datos: Generar y analizar grandes cantidades de datos puede ser un desafío sin sistemas adecuados.
Ejemplo: El análisis de vibraciones puede detectar desalineación en bombas temprano, previniendo fallas. Sin embargo, configurar tales sistemas requiere inversión en sensores y personal calificado para interpretar los datos.
Mantenimiento predeterminado
Ventajas:
- Simplicidad: Fácil de planificar y programar.
- Reducción del riesgo de fallas: El mantenimiento regular reduce la probabilidad de fallas inesperadas.
Desventajas:
- Potencial de sobre-mantenimiento: Puede conducir a trabajo innecesario si el equipo aún está en buenas condiciones.
- Implicaciones de costos: El reemplazo rutinario de piezas que pueden no necesitarlo incrementa los gastos.
Ejemplo: Cambiar el aceite en generadores cada tres meses asegura confiabilidad pero puede ser innecesario si el equipo no ha sido utilizado intensamente.
Mantenimiento correctivo inmediato
Ventajas:
- Restauración rápida: Minimiza el tiempo de inactividad al abordar fallas rápidamente.
- Esencial para equipos críticos: Necesario cuando la falla del equipo detiene las operaciones.
Desventajas:
- Altos costos: Las reparaciones urgentes a menudo implican horas extras y envío expedito de piezas.
- Estrés en el personal: Las situaciones de emergencia pueden llevar a fatiga y errores.
Ejemplo: Reparar una cinta transportadora rota en una operación minera inmediatamente es costoso pero esencial para mantener el flujo de producción.
Mantenimiento correctivo diferido
Ventajas:
- Optimización de recursos: Permite una mejor planificación y asignación de recursos de mantenimiento.
- Ahorro de costos: Diferir reparaciones no críticas puede reducir gastos inmediatos.
Desventajas:
- Riesgo de deterioro: Las reparaciones retrasadas pueden conducir a una mayor degradación del equipo.
- Potenciales riesgos de seguridad: Los problemas no abordados podrían representar riesgos para el personal.
Ejemplo: Posponer el reemplazo de una válvula con fugas hasta el próximo paro ahorra costos ahora pero requiere monitoreo cuidadoso para prevenir escalamiento.
Conclusión: Integrando estrategias de mantenimiento para un rendimiento óptimo
En mis tres décadas de experiencia, he aprendido que ninguna estrategia de mantenimiento única se adapta a todos los escenarios. La clave para la excelencia operativa radica en integrar diversos enfoques adaptados a las necesidades específicas de cada activo y operación. Implementar las directrices de ISO 14224:2016 proporciona un marco robusto para categorizar y ejecutar actividades de mantenimiento de manera efectiva.
Puntos clave
- Planes de mantenimiento personalizados: Desarrollar estrategias basadas en la criticidad del activo, frecuencia de fallas e impacto operativo.
- Enfoque holístico: Combinar mantenimiento preventivo, correctivo y oportunista para un cuidado integral de los activos.
- Mejora continua: Revisar y ajustar regularmente las prácticas de mantenimiento basadas en datos de rendimiento y estándares industriales en evolución.
Reflexiones finales
La gestión efectiva del mantenimiento es un viaje de aprendizaje y adaptación continuos. Exige experiencia técnica, planificación estratégica y una comprensión profunda tanto del equipo como de las personas. Como ingenieros de mantenimiento, aportamos una rica perspectiva que valora el trabajo duro, la innovación y la comunidad. Al fomentar la colaboración y adoptar las mejores prácticas como las descritas en ISO 14224, podemos impulsar nuestras industrias hacia una mayor eficiencia, seguridad y sostenibilidad.
Al integrar estas estrategias de mantenimiento de manera reflexiva, no solo mejoramos la confiabilidad del equipo sino que también contribuimos al éxito general y la competitividad de nuestras industrias. Continuemos aprendiendo, compartiendo y aplicando nuestro conocimiento para construir un futuro industrial más fuerte y resiliente.
Referencias:
ISO 14224:2016 - Petroleum, petrochemical and natural gas industries — Collection and exchange of reliability and maintenance data for equipment.
Mobley, R. K. (2002). An Introduction to Predictive Maintenance. Butterworth-Heinemann.
Campbell, J. D., & Reyes-Picknell, J. V. (2015). Uptime: Strategies for Excellence in Maintenance Management. Productivity Press.
¿Qué es Power-MI?
Power-MI es una herramienta en la nube que le permite diseñar y gestionar su mantenimiento predictivo con todas las técnicas en una plataforma. Informes fáciles, órdenes de trabajo automáticas e integración a CMMS.
Leer más