Análisis de vibraciones de turbinas de vapor
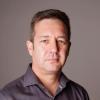
Las turbinas de vapor en las industrias se consideran auxiliares críticos para el funcionamiento en las plantas industriales y manufactureras. Se utilizan principalmente como conductores principales para componentes mecánicos como bombas, compresores, ventiladores y generadores para funciones específicas en los procesos de planta. La función de una turbina de vapor es convertir la energía del vapor en energía mecánica y utilizarla para hacer girar estos componentes mecánicos para producir el trabajo específico deseado (Fig. 1).
Las turbinas de vapor hacen girar estos dispositivos mecánicos a través de enormes estructuras y parecen indestructibles, sin embargo, son una pieza de equipo delicada y precisa en una planta. Para operar una turbina de forma segura y eficiente es importante tener una comprensión básica de su construcción y funcionamiento, así como de las metodologías de protección y monitorización de su funcionamiento en cada momento (Fig. 2).
Los detalles sobre la construcción de la turbina y la forma en que las diferentes partes trabajan juntas para su funcionamiento no formarán parte de las discusiones de este artículo que en cambio se centrarán en los sistemas de protección y monitorización y en el diagnóstico de anomalías en el componente de la máquina. También hablaremos de los principales factores que influyen en el comportamiento del componente durante su funcionamiento y analizaremos los fallos y los indicadores de comportamiento anormal.
Al igual que ocurre con otros componentes de máquinas, en las turbinas de vapor se suelen encontrar diferentes fallos y comportamientos anómalos durante el funcionamiento. La mayoría de los analistas casi siempre consideran estas anomalías como un preludio de problemas potenciales que, si se ignoran y no se investigan, suelen progresar hasta convertirse en situaciones peligrosas, cuando no en sucesos catastróficos. Desgraciadamente, hay numerosos casos de sucesos catastróficos en el pasado en este componente cuando la protección y/o el anuncio de la aparición de un problema inminente son convenientemente ignorados por unos pocos operadores y pasan el problema al siguiente turno, especialmente durante los turnos de noche y sin analistas experimentados cerca para ayudar. Como resultado, por muy adecuadamente protegidas y mantenidas periódicamente, las turbinas de vapor siguen siendo vulnerables a anomalías y fallos durante su operación normal.
Establecer la fuente correcta de la vibración excesiva que afecta al funcionamiento de la turbina de vapor es probablemente la tarea más difícil del análisis de maquinaria. Una vez determinada la fuente de vibración, generalmente es posible evaluar la gravedad del problema comparando el nivel de vibración con una norma de vibración especificada. Como las fuentes de las distintas fuerzas de excitación suelen producirse a diferentes frecuencias. Es muy útil caracterizar las señales de vibración medidas con respecto a la frecuencia. Así, el análisis espectral es un procedimiento básico recomendado para resolver problemas de vibraciones y evaluar la fiabilidad de los equipos[1].
Debemos interpretar las señales de vibración obtenidas mediante el análisis espectral en relación con el diseño de la máquina, la instalación y la fuente de vibración. Para aprovechar al máximo los criterios de vibración, es necesario colocar los transductores de vibración de manera que se pueda identificar por separado la fuente de vibración. A continuación se ofrece una visión general de las fuentes de vibración más comunes en las turbinas de vapor.
Resonancia
La resonancia es probablemente la causa más común de fallos relacionados con las vibraciones. Desgraciadamente, las especificaciones de vibración suelen ignorar completamente las resonancias y dependen del fabricante para estos criterios. Las normas API proporcionan directrices generales sobre los límites de velocidad crítica para la vibración lateral del eje para varios tipos diferentes de equipos rotativos. Por ejemplo, los compresores y las bombas deben tener límites de velocidad crítica lateral del 20% por encima de la velocidad máxima de funcionamiento o del 15% por debajo de la velocidad mínima de funcionamiento. Además, los factores de amplificación no deben exceder de ocho al pasar por las velocidades críticas (Fig. 3). Si la velocidad crítica medida se encuentra dentro del rango excluido, el fabricante debe demostrar que las vibraciones a la velocidad crítica están dentro de los límites de vibración aceptables con un desequilibrio considerablemente mayor del que normalmente se esperaría[1].
Es muy poco lo que se puede hacer para minimizar las vibraciones de los álabes una vez que han surgido como problema en el campo. El principio fundamental para tratar las vibraciones de los álabes es evitar la resonancia. La frecuencia natural del álabe no debe estar dentro del 10% de ninguna frecuencia de excitación identificable en ningún punto del rango de funcionamiento normal, incluidos los múltiplos de la frecuencia de paso del álabe y los múltiplos de la velocidad de funcionamiento. Los fenómenos aerodinámicos son demasiado complejos para ser predecibles y varían mucho de una máquina a otra, y cualquier intento de vivir con una excitación de los cuatro o cinco modos inferiores del álabe es probable que provoque un fallo de pérdida del álabe, independientemente de las predicciones de la fuerza de excitación[1].
Desequilibrio
El desequilibrio es una fuente común de vibraciones en la maquinaria y casi siempre se caracteriza por una vibración radial del eje o de la carcasa que está en perfecta sincronía con la velocidad del rotor (Fig. 4). Esta anomalía es el problema más común en la maquinaria rotativa. El desequilibrio del rotor es una condición de distribución desigual de la masa de cada sección del rotor. En una condición de desequilibrio, la línea central de la masa del rotor no coincide con el eje de rotación.
Durante la rotación, el desequilibrio del rotor genera una fuerza centrífuga de inercia que gira a la frecuencia de rotación del rotor. El desequilibrio representa, por tanto, el primer mecanismo fundamental para transferir la energía de rotación a vibraciones y la condición de desequilibrio más frecuente en los rotores de las turbinas[2].
Las inevitables imperfecciones de la geometría debidas a la fabricación o a la variación de los materiales provocarán un desequilibrio del rotor, de modo que prácticamente todas las máquinas nuevas de alta velocidad requerirán un equilibrado en la fábrica. Algunas máquinas muy sensibles también requerirán un ajuste de equilibrio después de la instalación. Se debe esperar que la vibración cambie gradualmente con el tiempo, ya que los efectos de la erosión, el desgaste y la adhesión de partículas provocan el desequilibrio. Las piezas del rotor, como los collares de empuje, los ventiladores de refrigeración y el acoplamiento, pueden ser fuentes importantes de desequilibrio, pero a menudo se pasan por alto debido a su pequeño tamaño. Para identificar estas fuentes de desequilibrio variable es necesaria una cuidadosa correlación de la vibración con el crecimiento térmico del eje[1].
La localización del vector de respuesta subsíncrona suele presentarse en formato de diagrama de Bode o polar. La señal de vibración del rotor se filtra a la frecuencia de la rotación y normalmente se compensa restando el vector de respuesta de rotación lenta 1 X de balanceo (baja frecuencia). Estos formatos se utilizan extensamente para el diagnóstico y la corrección del desequilibrio (Fig. 5). Los gráficos también permiten detectar fácilmente las frecuencias de resonancia y evaluar el amortiguamiento efectivo del sistema y el factor de amplificación sincrónica utilizando el método de ancho de banda de media potencia[2].
El desequilibrio del rotor se corrige normalmente mediante procedimientos rutinarios de equilibrado de la máquina, que puedan realizarse mediante programas de software de equilibrado comúnmente utilizados por la mayoría de los analistas. El procedimiento también puede realizarse mediante representaciones gráficas de los vectores de los coeficientes de influencia cuando no se dispone de programas de software de equilibrado.
Inestabilidad del aceite en cojinete
El eje giratorio funciona en un fluido dinámico. La interacción entre el rotor y el fluido circundante es significativa si las holguras entre las piezas giratorias y fijas son pequeñas y el rotor funciona con una excentricidad baja dentro de las holguras. Debido a la fricción, la rotación del eje genera un flujo circunferencial del fluido. El fluido, a su vez, produce un efecto dinámico de fuerzas cíclicas que actúan en contraposición al rotor. Este tipo de situaciones se producen en los cojinetes lubricados por fluido con poca carga, en las juntas de los pistones de equilibrio, en los espacios libres entre el estator y los álabes y en las periferias entre el rotor y el estator. Fenómenos similares se producen en todos los casos en los que el fluido se involucra en el movimiento de rotación, como en las centrífugas, los rotores con fluido atrapado o los rotores llenos de fluido. Son bien conocidos los efectos dinámicos finales de tales interacciones entre el rotor y el fluido, llamados las vibraciones subcrónicas autoexcitadas del rotor del tipo "remolino de fluido" y "latigazo de fluido"[1]. Las inestabilidades suelen presentar frecuencias de vibración a aproximadamente 1/2 velocidad de funcionamiento (Fig. 6) y tienen tendencia a aumentar repentinamente su amplitud con resultados desastrosos.
El diagnóstico de las vibraciones de remolino/latigazo del fluido es relativamente fácil, especialmente cuando se dispone de los datos transitorios de arranque/parada. Las mediciones filtradas de la fase de remolino/latigazo permiten identificar la ubicación de la fuente de inestabilidad a lo largo del tren de la máquina. Sin embargo, es más difícil identificar la causa real de la inestabilidad, especialmente cuando sólo están presentes las vibraciones del latigazo[2].
Los datos de la posición de la línea central del eje pueden indicar la inminencia de un mal funcionamiento relacionado con el fluido antes de la aparición real de las vibraciones de remolino/latigazo. Una posición de excentricidad gradualmente decreciente del muñón dentro de la holgura del cojinete debido a cambios en las fuerzas de carga radial o debido al desgaste de la superficie del cojinete advierten que pronto se producirá un remolino o un latigazo del fluido. Las vibraciones axiales y los datos de posición también pueden advertir sobre los cambios en el flujo que pueden conducir a las vibraciones de remolino/latigazo (Fig. 7)[2].
Desalineación
Una desalineación excesiva de los elementos giratorios accionados a través de acoplamientos elásticos suele estar indicada por una gran componente de vibración de segundo orden (Fig. 8).
Ocasionalmente, también se observan grandes vibraciones de primer orden. Unas vibraciones axiales elevadas son otro indicio de que la desalineación es probable. La desalineación del eje se ve afectada por el crecimiento térmico relativo, las fuerzas estáticas aplicadas por las tuberías o los accesorios del condensador, el deterioro del grouting de fijación, etc. La vibración debida a la desalineación de primer orden puede diferenciarse del desequilibrio registrando la vibración en relación con las rpm. La vibración por desequilibrio aumentará con el cuadrado de las rpm, mientras que la vibración por desalineación no cambiará si no hay resonancias. En el caso de las máquinas que no pueden pararse convenientemente, se recomienda hacer un registro del espectro de vibraciones cuando la máquina se pone en marcha por primera vez y está bien alineada. Esto puede utilizarse para una comparación posterior para determinar si la alineación de la máquina sigue siendo satisfactoria[1].
La desalineación excesiva debida a las cargas radiales puede diagnosticarse a partir de los datos de vibraciones. El movimiento orbital anormal, la línea media radial del eje anormal y el movimiento anormal del eje frente a la carcasa son indicativos de cargas radiales excesivas. En la figura 9 se muestran los gráficos que ilustran las características de la desalineación y las precargas radiales excesivas en el rotor. Una precarga radial de acción continua en un rotor que funciona a velocidad constante provoca tensiones periódicas de inversión de frecuencia 1X (más posibles armónicos superiores) en la fibra del rotor. Esta situación puede provocar el agrietamiento del rotor y su fallo prematuro[2].
Roce
El roce entre el rotor y la parte fija de la máquina es una avería grave que conduce a un fallo catastrófico. El roce implica varios fenómenos físicos, como la fricción, el efecto de acoplamiento rígido, el impacto y puede afectar al equilibrio sólido/fluido/térmico en el sistema de la máquina. El roce siempre se produce como efecto secundario de un mal funcionamiento primario, como el desequilibrio, la desalineación o las vibraciones autoexcitadas inducidas por el fluido, que dan lugar a elevadas amplitudes de vibración lateral o a un cambio en la posición de la línea central del eje dentro de las holguras disponibles[2].
Los roces entre un rotor y los componentes estacionarios con poca holgura pueden dañar las juntas y las puntas de las palas. Las características notificadas de las vibraciones inducidas por el roce incluyen subarmónicos fijos del rotor, vibraciones subsíncronas a una frecuencia natural, vibraciones supersíncronas a una frecuencia natural, vibraciones síncronas variables en el tiempo y vibraciones a múltiplos de la velocidad de funcionamiento. Por lo tanto, es difícil hacer afirmaciones generales sobre los roces, y los síntomas del roce están influidos por los materiales en contacto, la impedancia al movimiento de la junta cuando se pone en contacto, la ubicación de las frecuencias naturales, etc. Los roces de los rotores de acero inoxidable parecen ser especialmente dañinos y se sabe que causan una rápida deformación permanente del rotor. Por otro lado, las turbinas de vapor de alto rendimiento se diseñan con holguras del laberinto muy ajustadas y es de esperar que se produzcan roces leves durante las primeras fases de la puesta en marcha. Estos roces temporales pueden provocar un calentamiento localizado y un arqueo temporal del rotor, con el consiguiente desequilibrio elevado, especialmente cuando el rotor funciona por debajo de su primera velocidad crítica. Los síntomas de esta vibración particular inducida por el roce son una variación temporal lenta de la amplitud y la fase de la sincronización, y a menudo una órbita de tipo cuadrado (Fig. 10)[1].
El diagnóstico del roces del rotor a partir de los datos de vibración se basa en (i) la aparición en los vectores de respuesta síncronos del rotor, (ii) la aparición de componentes fraccionarios sub-síncronos que, cuando se filtran, suelen mostrar una órbita invertida, (iii) la aparición de fundamentales de corta duración con frecuencias naturales (debido al carácter transitorio del rozamiento), (iv) la aparición de armónicos superiores de los componentes fundamentales, (v) los cambios en la posición de la línea central del eje (Fig. 11). La órbita invertida parcial o total respecto al rotor es lo más característico en caso de roces, lo que distingue este fallo de los demás[2].
Por supuesto, existen otras fuentes de vibración distintas de las comentadas anteriormente, que pueden provocar fallos en la máquina. Por mencionar algunas son: holgura mecánica entre eje y piezas fijas, desplazamientos del acoplamiento, holgura entre pedestal de soporte del rotor y cimentación, rodamientos sobredimensionados y mal lubricados, holgura excesiva en rodamientos, rodamientos defectuosos, ruido producido por engranajes defectuosos, etc.
Mediciones de las vibraciones y parámetros básicos
Como se ha mencionado anteriormente, las turbinas, aunque tienen una estructura maciza y parecen indestructibles, son componentes delicados por su configuración y por tanto necesitan una protección adecuada y la supervisión del comportamiento de las vibraciones para un correcto funcionamiento. Aunque el mantenimiento preventivo ha demostrado ser beneficioso en términos de aumento de la productividad y reducción del tiempo de paradas no programadas, el mantenimiento basado en la condición ha demostrado que la aplicación de la monitorización de condiciones conlleva a una mejor fiabilidad de la maquinaria que el mantenimiento basado en el tiempo (mantenimiento preventivo).
Esta filosofía de mantenimiento basado en la condición se aplica con éxito cuando el componente de la maquinaria rotativa representa el factor limitante de un sistema, como en las turbinas de vapor. Obviamente, este tipo de programa de mantenimiento predictivo requiere depender de la instrumentación y de la interpretación adecuada de los datos que ésta proporciona. Es importante que se midan y evalúen todos los parámetros disponibles de vibración y posición del rotor. Una simple investigación de la amplitud y la frecuencia por sí sola no proporciona suficiente información sobre el rendimiento de la maquinaria para ofrecer un diagnóstico sólido y preciso.
Parámetros
A continuación se analizan los parámetros básicos de movimiento dinámico (vibración) y posición del rotor que deben medirse y analizarse en el diagnóstico de la maquinaria rotativa en los programas de mantenimiento predictivo:
Movimiento dinámico (vibración)
- Amplitud
La amplitud, ya sea expresada en desplazamiento, velocidad o aceleración, es generalmente un indicador de la gravedad de la anomalía. Intenta responder a la pregunta: "¿Esta máquina funciona con suavidad o con brusquedad?". El movimiento dinámico en las turbinas de vapor se monitoriza y protege mejor utilizando sondas de proximidad instaladas en orientación ortogonal para observar el comportamiento dinámico del eje. La posibilidad de medir el eje con sondas de proximidad ha contribuido en gran medida a proporcionar información más precisa con respecto a la amplitud de las vibraciones. En el pasado, la medición del eje empleada sólo proporciona la amplitud de la vibración era parámetro disponible para la gravedad, e indica la presencia de un mal funcionamiento de la maquinaria. Sin embargo, esta medición resultaba inadecuada para la protección adecuada de la maquinaria. Esto se debe principalmente a la impedancia de transferencia variable entre el movimiento del eje y el movimiento de la carcasa, dependiendo del diseño particular de la máquina, el montaje, las condiciones de funcionamiento y la ubicación de la toma de la carcasa.
La amplitud de la vibración se expresa en desplazamiento pico-pico. Con las sondas de proximidad montadas en los cojinetes o cerca de ellos, se pueden establecer tolerancias de vibración que contemplen el máximo desplazamiento que realiza el eje con respecto al rodamiento. Una máquina de funcionamiento normal tendrá generalmente una lectura de amplitud estable de un nivel bajo aceptable. Cualquier cambio en esta lectura de amplitud indica un cambio en la condición de la máquina y debe considerarse como una justificación para una mayor investigación de la condición particular de la máquina.
- Frecuencia
La frecuencia es un dato importante en el análisis de la maquinaria rotativa y puede ayudar a clasificar las averías, pero es sólo un dato. La frecuencia de la vibración (ciclos por minuto) se expresa más comúnmente en múltiplos de la velocidad de rotación de la máquina. Esto se debe principalmente a la tendencia de las frecuencias de vibración de la máquina a producirse en múltiplos o submúltiplos directos de la velocidad de rotación de la máquina. También proporciona un medio fácil de expresar la frecuencia de la vibración. Sólo es necesario referirse a la frecuencia de las vibraciones en términos tales como una vez las rpm, dos veces las rpm, 43% de las rpm, etc., en lugar de tener que expresar todas las vibraciones en ciclos por minuto o hercios.
Sin embargo, es muy importante tener en cuenta que la relación frecuencia/mal funcionamiento no es mutuamente excluyente. Es decir, una vibración a una frecuencia concreta suele llevar asociada más de una avería. No existe una relación unívoca entre las disfunciones y las frecuencias de vibración. No hay que dejarse llevar fácilmente por el intento de correlacionar directamente ciertas frecuencias con averías concretas. Es necesario evaluar todos los datos antes de llegar a una conclusión.
La forma típica de expresar la frecuencia es la siguiente:
1 x rpm: La frecuencia de la vibración es la misma que la velocidad de rotación de la máquina.
2 x rpm: La frecuencia de la vibración es el doble de la velocidad de rotación de la máquina.
1/2 x rpm: La frecuencia de la vibración es la mitad de la velocidad de rotación de la máquina.
0,43 x rpm: La frecuencia de la vibración es el cuarenta y tres por ciento de la velocidad de rotación de la máquina, etc.
Es importante tener en cuenta una media que diferencia dos tipos de vibración: Síncronas y no síncronas. La vibración sincrónica se produce a una frecuencia que es algún múltiplo directo o fracción entera de la velocidad de rotación de la máquina. Las mediciones básicas de la frecuencia pueden realizarse con el uso de un Keyphasor y un osciloscopio. Es posible, con un mínimo de práctica, ser capaz de distinguir los principales componentes de la vibración presentes en una forma de onda de vibración.
- Ángulo de fase
El ángulo de fase de la vibración ha sido ignorado durante mucho tiempo como un criterio importante para el análisis de la maquinaria rotativa por la gente en muchas áreas de uso de las máquinas rotativas. Sin embargo, las personas sensatas de las industrias de generación de energía y de petróleo y gas han reconocido su valor durante mucho tiempo. La medición del ángulo de fase es un medio para describir la ubicación del rotor en un instante concreto del tiempo. Un buen sistema de medición del ángulo de fase definirá la ubicación del punto alto del rotor en cada ubicación del transductor en relación con algún punto fijo en el tren de la máquina. Al determinar estos puntos altos en el rotor, es posible determinar el estado de equilibrio y la ubicación de los desequilibrios residuales en un rotor. Las mediciones precisas de los ángulos de fase son extremadamente importantes en el equilibrado de los rotores, y pueden ser muy importantes en el análisis de averías particulares de la máquina. Los ángulos de fase del rotor determinados por varios transductores a lo largo de un tren de máquinas pueden proporcionar información valiosa sobre el rendimiento del tren de máquinas. Es este ángulo de fase el que proporciona información de tiempo que ayuda a responder a las preguntas: ¿Qué ocurre, dónde, cuándo y cómo?
El ángulo de fase también es valioso para determinar la ubicación en rpm de la resonancia natural de equilibrio del rotor ("crítica"). El medio más preciso y fiable para medir el ángulo de fase es el uso de un Keyphasor (referencia del eje). La medición ganó rápidamente aceptación como un parámetro muy importante para el diagnóstico de la maquinaria rotativa, así como para las operaciones de equilibrado, y generalmente se incluye como parte del paquete de instrumentación para las grandes turbinas de vapor en servicio de generación de energía y dispositivos mecánicos de accionamiento como compresores, bombas o ventiladores.
- Forma de vibración
La forma de la vibración es quizás el medio más importante de presentar los datos de vibración para su análisis. Es a través de este tipo de presentación que se puede comprender el comportamiento de una máquina en particular. Los tres parámetros anteriormente discutidos han sido cantidades medibles que pueden ser mostradas en un medidor o pantalla digital, mientras que la "forma de vibración" es la forma de onda en bruto en sí misma, mostrada en un osciloscopio o en la actualidad con un programa de software. La forma de vibración puede separarse en dos categorías distintas: (1) presentación de la base de tiempo; y (2) presentación orbital. La presentación en base al tiempo se proporciona mostrando las entradas del transductor en el osciloscopio/programa de software en el modo de base al tiempo. En este modo, la forma de onda de tipo sinusoidal se muestra representando el eje relativo al transductor de entrada frente al tiempo horizontalmente a través del punto de referencia. En este modo, el osciloscopio/programa de software muestra el movimiento de la línea central del eje en esa ubicación horizontal a lo largo del rotor. Si las sondas están montadas en el rodamiento, la órbita es una presentación del movimiento de la línea central del eje con relación al rodamiento.
Estas dos presentaciones ofrecen a los ingenieros/analistas la mayor cantidad de datos en una sola presentación. La amplitud básica, la frecuencia y el ángulo de fase se pueden determinar viendo la forma de vibración. Las presentaciones de la forma de vibración ayudan intrínsecamente al individuo a entender "lo que la máquina está haciendo", observando el movimiento real de la parte observada. Este es un concepto importante. La forma de vibración permite la transición de determinar cuáles son las amplitudes y las frecuencias, a determinar "lo que la máquina está haciendo". Este es el parámetro final que se intenta medir en cualquier programa de mantenimiento preventivo o predictivo.
- Forma de modo de vibración
Una práctica recomendada para proporcionar información sobre una máquina rotativa es proporcionar un conjunto extra de sondas X-Y (separadas 90o) a cierta distancia del cojinete. Estas sondas extra-horizontales normalmente no serían monitoreadas pero estarían disponibles para el diagnóstico. El conjunto extra-horizontal proporciona una tercera dimensión a los datos de la maquinaria y permite una estimación de la forma del modo del rotor de la máquina para la determinación de los puntos nodales. Es importante reconocer que cualquier conjunto de sondas X-Y a lo largo del tren de la máquina proporcionará el movimiento del rotor en esa ubicación horizontal a lo largo de la máquina. Utilizando el conjunto adicional de sondas X-Y en una ubicación horizontal diferente a lo largo del tren de la máquina, podemos intentar determinar la forma del modo básico del propio rotor. Esta forma de modo puede ayudar a dar estimaciones más cercanas a las holguras internas entre los elementos del rotor y del estator y a dar una estimación de los puntos nodales a lo largo del eje del rotor.
Mediciones de posición
Otros parámetros que también deben medirse y evaluarse para el rendimiento total de la maquinaria entran en la categoría de mediciones de posición estáticas o cuasiestáticas. Dependiendo del diseño particular de la máquina y del mal funcionamiento de la misma, estas mediciones pueden ser importantes en la evaluación y el análisis. A continuación se presenta una discusión de estas mediciones de tipo de posición:
- Posición de excentricidad
La posición de excentricidad es la medición de la posición de estado estable del eje en los cojinetes de deslizamiento. En funcionamiento normal, sin precargas internas o externas en el eje, el eje de la mayoría de los diseños de máquinas se desplazará donde lo coloque la presa de presión de aceite. Sin embargo, en cuanto la máquina recibe alguna precarga de tipo externo o interno, (fuerza de estado estable), la posición de excentricidad del eje en el cojinete de deslizamiento puede estar en cualquier lugar. Esta medición de la posición de excentricidad puede ser un excelente indicador del desgaste del cojinete y de las condiciones de precarga pesada, como la desalineación.
La posición de excentricidad también debe ser observada de cerca durante el arranque de la máquina. Durante el arranque de una máquina con una sonda de proximidad montada verticalmente, normalmente se espera que el eje se eleve desde el fondo del cojinete. Esto se debe fundamentalmente a que el aceite que fluye bajo el eje hace que éste se eleve en el rodamiento. En general, se cree que la película de aceite tiene un grosor de aproximadamente un milímetro. Las observaciones realizadas en muchos cojinetes muestran que, con mayor frecuencia, es de aproximadamente 1/3 del juego del cojinete en la dirección de precarga del eje.
Es importante que el sistema de transductor de la sonda de proximidad tenga un rango lineal largo suficiente para permitir que se produzcan estos cambios de posición de excentricidad sin que el eje se mueva fuera del rango lineal de la sonda de proximidad. Esto es especialmente cierto en máquinas de gran tamaño en las que normalmente hay grandes holguras en los rodamientos. Es importante documentar la posición de excentricidad en frío y la posición de excentricidad en caliente para establecer un marco de referencia para comparar la posición de excentricidad en fechas posteriores.
- Posición de empuje axial
La posición de empuje axial es la medición de la posición relativa del collarín de empuje con respecto al cojinete de empuje. Esta medición es quizás uno de los parámetros más importantes que se monitorean en una turbina de vapor y/o compresor centrífugo. El propósito principal de un monitor de posición de empuje axial es proteger contra un roce axial entre el rotor y el estator. Los fallos de los cojinetes de empuje axial pueden ser catastróficos y debe hacerse todo lo posible para evitar este fallo de la máquina.
Se debe montar al menos una sonda de posición de empuje axial, preferiblemente dos, para proporcionar protección de posición de empuje axial. Se debe tener cuidado en la selección de las ubicaciones de montaje de la sonda para asegurar el mínimo efecto del crecimiento térmico del rotor y el mínimo efecto de la elasticidad del conjunto de cojinete de empuje en la precisión de la lectura. En las primeras aplicaciones de las sondas de proximidad para la medición de la posición de empuje axial, se observó con mucha frecuencia, que los puntos de ajuste de alarma y peligro se establecían demasiado cerca de la zona de flotación fría inicial de la máquina. Se descubrió que se producen desviaciones en los conjuntos de cojinetes de empuje y se produce un crecimiento térmico del rotor, de modo que en condiciones normales de funcionamiento la posición del rotor puede parecer más amplia que la zona normal de flotación en frío del rotor dentro de su cojinete de empuje. Es importante señalar que la mayoría de las máquinas tienen suficiente holgura axial entre el rotor y el estator para que puedan establecerse puntos de ajuste amplios que permitan que el collarín de empuje limpie severamente el babbitt de las zapatas del cojinete de empuje sin que haya roces entre el rotor y el estator. En condiciones normales de funcionamiento de un compresor centrífugo o de una turbina de vapor, la posición de empuje puede variar con la carga de la máquina, por lo que no es raro que varíen las mediciones de la posición de empuje bajo cargas y condiciones diferenciales de una máquina. La medición de la posición de empuje también puede ser importante en la determinación de las condiciones de sobretensión incipiente.
Si la vibración axial va a ser monitorizada o utilizada para el diagnóstico de una máquina en particular, es necesario que la superficie observada sea lisa y esté perpendicular a la línea central del rotor. Esto minimizará cualquier efecto de desviación mecánica de la salida dinámica de la sonda, proporcionando así lecturas de vibración axial precisas.
- Excentricidad Slow-Roll (excentricidad pico-pico)
En las grandes turbinas de vapor para el servicio de generación de energía y en algunas turbinas de gas industriales, es muy a menudo deseable indicar la excentricidad slow-roll, también llamada excentricidad pico-pico. La excentricidad slow roll es la cantidad de inclinación que toma el rotor cuando está en reposo (condición de engranaje de giro). La medición de pico a pico de la corriente continua que cambia lentamente puede indicar esta inclinación desde el proximímetro a medida que el rotor gira en el engranaje de giro. Cuando la amplitud pico a pico está en un nivel bajo aceptable, la máquina puede arrancarse sin temor a que se dañen las juntas y/o los roces del rotor causados por el arco residual y su correspondiente desequilibrio. La mejor forma de medir la excentricidad del rodamiento es con una sonda montada lejos del rodamiento (o al final del tren de la máquina) para poder medir las máximas desviaciones del arco.
- Expansión diferencial
En máquinas muy grandes, como las grandes turbinas de vapor en servicio de generación de energía, es extremadamente importante que durante el arranque la carcasa y el rotor crezcan térmicamente a la misma velocidad. Si el rotor o la carcasa crecen a ritmos diferentes, existe la posibilidad de que se produzcan daños en la máquina causados por roces axiales. Para medir esta expansión diferencial, se monta una sonda de proximidad en el extremo de la máquina opuesto al cojinete de empuje, donde se puede observar el crecimiento relativo entre la carcasa y el rotor. El rango típico de esta sonda de proximidad es de 1 pulgada. En máquinas muy grandes, este rango requerido del sistema de sonda de proximidad puede ser tan grande como 2 o 3 pulgadas.
- Expansión de la caja
En máquinas muy grandes también es muy común proporcionar, además de la expansión diferencial, una medición de la expansión de la caja. Esta medición de la dilatación de la caja suele realizarse mediante un transformador diferencial variable lineal (LVDT) de contacto montado en el exterior de la caja de la máquina y referenciado a los cimientos. Esta medición de la expansión de la caja ayuda a proporcionar información sobre el crecimiento relativo del rotor con respecto a la caja, como se describió en el párrafo sobre la expansión diferencial. Conociendo la cantidad de crecimiento de la carcasa y la cantidad de crecimiento diferencial es posible determinar qué está creciendo a un ritmo más rápido: el rotor o la carcasa. Si la carcasa no está creciendo adecuadamente, las "patas de deslizamiento" de la carcasa pueden estar atascadas.
Otros parámetros
- Velocidad (rpm)
La medición de la velocidad (rpm) del rotor es un procedimiento estándar desde hace mucho tiempo. La mayoría de los principales trenes de máquinas centrífugas han tenido una indicación continua de las rpm de la máquina. Con la llegada de nuevos y fiables circuitos digitales, los tacómetros digitales se han hecho más populares para la indicación de la velocidad. Además de ser más preciso y fácil de leer, el tacómetro digital se presta muy bien a proporcionar una protección redundante contra el exceso de velocidad. La indicación digital de las rpm elimina muchos de los antiguos problemas asociados a la medición de las rpm. La indicación precisa y fácilmente legible de las rpm se proporciona generalmente en la sala de control para que los operadores la observen.
Las entradas del transductor para los tacómetros digitales pueden ser de una variedad de entradas. Entre las más populares están la entrada de la sonda de proximidad Keyphasor, la captación fotoeléctrica y la captación magnética. Todos estos transductores están diseñados para observar un número de eventos por revolución del eje. Esta entrada, básicamente digital, se traduce en una lectura directa de las revoluciones por minuto mediante el circuito del tacómetro digital.
La correlación de la medición de las vibraciones con las rpm puede ser importante para el análisis final del rendimiento mecánico de una determinada máquina. Los equipos centrífugos están diseñados para funcionar en un rango de velocidades que no coincidirá con la resonancia de equilibrio de esa máquina en particular, y a velocidades que no excitarán estas resonancias particulares. Una información inicial importante para determinar la resonancia de equilibrio es un gráfico X-Y de la amplitud y el ángulo de fase de la vibración frente a las rpm de la máquina. Al trazar y correlacionar estos parámetros, es posible determinar fácilmente la resonancia de equilibrio de la máquina (crítica).
- Medición de la temperatura
En el análisis final del estado de una determinada pieza de maquinaria rotativa, otros parámetros también adquieren importancia. Uno de los parámetros más populares e importantes que aún no se ha discutido es el de las mediciones de temperatura. La temperatura de los cojinetes, tanto radiales como axiales, es cada vez más popular. Una correlación de esta información de temperatura con las mediciones de vibración y/o posición ayuda a dar una mejor indicación de posibles fallos en la maquinaria.
- Correlación
La correlación de las temperaturas, las presiones, el flujo y otros parámetros externos que podrían afectar al funcionamiento de una pieza de maquinaria es extremadamente importante para el análisis global del sistema de la máquina en servicio. Es a través de esta correlación que se puede establecer un buen programa de mantenimiento predictivo. La capacidad del ingeniero para utilizar toda la información disponible en la determinación de la condición de funcionamiento mecánico de la pieza de maquinaria es extremadamente importante en el objetivo general de mantener el buen funcionamiento y el servicio continuo en línea de cualquier pieza de equipo.
El ingeniero que tenga un conocimiento profundo de los parámetros discutidos en este artículo tendrá un buen comienzo hacia la comprensión del rendimiento mecánico de los equipos centrífugos. Es a través de la comprensión de estos parámetros que en última instancia será capaz de determinar "lo que una pieza particular de la maquinaria está haciendo".
[1] More Comprehensive Vibration Limits for Rotating Machinery, ASME 86-GT-148 - A. Lifshits, H. R. Simmons, A. J. Smalley.
[3] Bently Nevada Mechanical Diagnostics Services (MDS) Reports 1987-1990.
¿Qué es Power-MI?
Power-MI es una herramienta en la nube que le permite diseñar y gestionar su mantenimiento predictivo con todas las técnicas en una plataforma. Informes fáciles, órdenes de trabajo automáticas e integración a CMMS.
Leer más